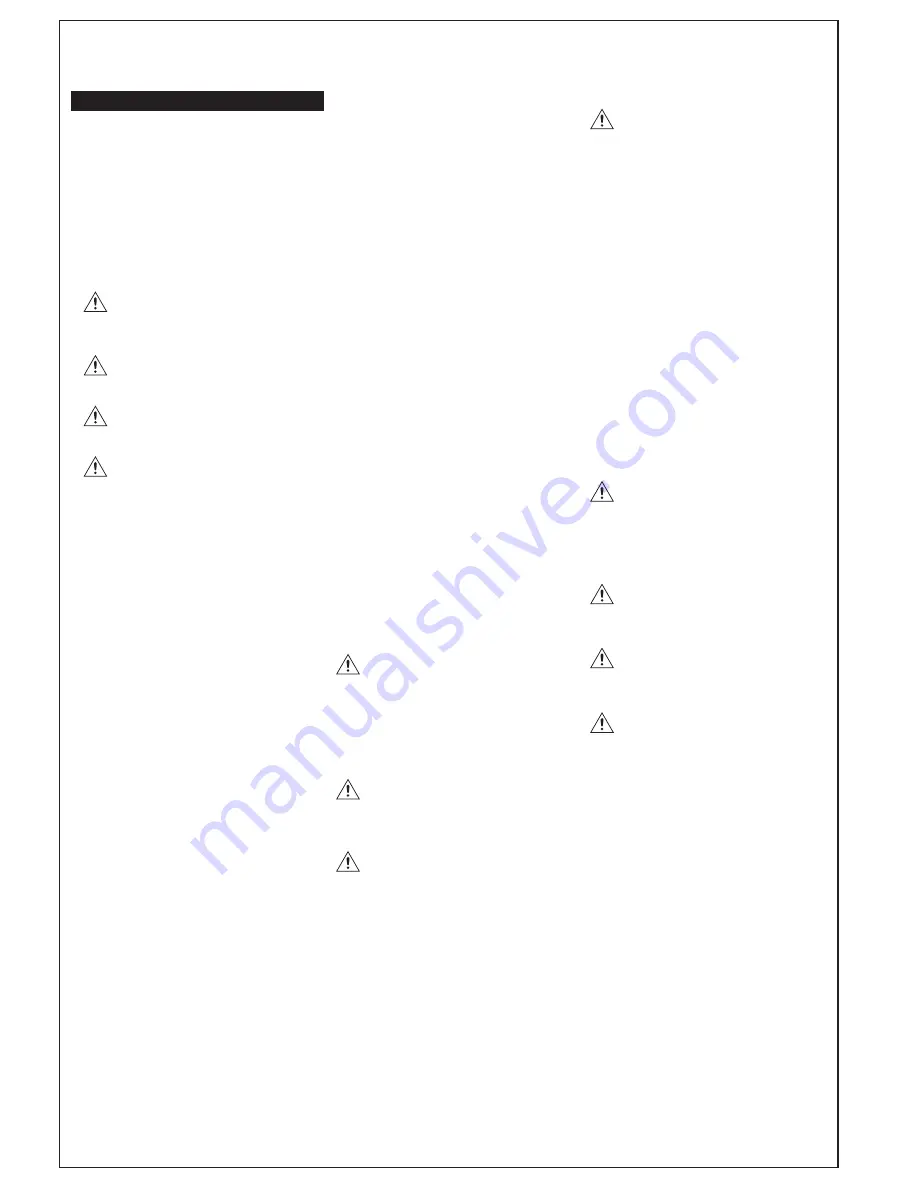
SAFETY INFORMATION
STORE AND RETAIN THIS MANUAL
Retain this manual for the safety warnings and
precautions, assembly, operating, inspection,
maintenance and cleaning procedures. Write the
product’s serial number into the NOTES section at
the rear, and keep this manual and the receipt in a
safe and dry place for future reference.
IMPORTANT SAFETY INFORMATION
Failure to follow the warnings and instructions may
result in electric shock, fire, serious injury and/or
death. Save all warnings and instructions for future
reference.
This is the safety alert symbol to alert you to
potential personal injury hazards. Obey all safety
messages that follow this symbol to avoid possible
injury or death.
DANGER
indicates a hazardous situation
which, if not avoided, will result in death or serious
injury.
WARNING
indicates a hazardous situation
which, if not avoided, could result in death or
serious injury.
CAUTION
, used with the safety alert symbol,
indicates a hazardous situation which, if not
avoided, could result in minor or moderate injury.
NOTE
, used to address practices not related to
personal injury.
CAUTION
, without the safety alert symbol, is used to
address practices not related to personal injury.
GENERAL SAFETY WARNINGS
1.
0DLQWDLQODEHOVDQGQDPHSODWHVRQWKHZHOGHU
7KHVHFDUU\LPSRUWDQWLQIRUPDWLRQ,I
XQUHDGDEOHRUPLVVLQJFRQWDFW\RXUQHDUHVW
675$7$6WRUHIRUDUHSODFHPHQW
2. Avoid unintentional starting.
Make sure the welder
is setup correctly and you are prepared to begin work
before turning on the welder.
3. Unplug before performing maintenance.
Always
unplug the Welder from its electrical outlet before
performing any inspection, maintenance, or clean-
ing procedures.
4. Never leave the welder unattended while ener-
gised.
Turn power off before leaving the welder
unattended.
5. Do not touch live electrical parts.
Wear dry,
insulating gloves. Do not touch the electrode or the
conductor tong with bare hands. Do not wear wet or
damaged gloves.
6. Protect yourself from electric shock.
Do not use
the welder outdoors. Insulate yourself from the
work piece and the ground. Use non-flammable,
dry insulating material if possible, or use dry rubber
mats, dry wood or plywood, or other dry insulating
material large enough to cover the area of contact
with the work or the ground.
7. Avoid inhaling dust.
Some dust created by power
sanding, sawing, grinding, drilling, cutting, welding
and other construction activities, contain chemicals
known to cause cancer, birth defects or other harm.
Your risk from these exposures varies, depending
on how often you do this type of work. To reduce
your exposure to these chemicals, work in a
well-ventilated area, and work with approved safety
equipment, such as dust masks that are specially
designed to filter out microscopic particles.
8. People with pacemakers should consult their
physician(s) before using this machine.
WARNING
Electromagnetic fields in close proximity to a heart
pacemaker could cause interference, or failure of
the pacemaker. The use of a Welder is NOT
RECOMMENDED for pacemaker wearers. Consult
your doctor.
9. Ensure that the unit is placed on a stable location
before use.
WARNING
If this unit falls while plugged in, severe injury,
electric shock, or fire may result.
10. Transportation Methods
CAUTION
Disconnect input power conductors from
de-energized supply line before moving the welding
power source.
Lift unit with the handles provided, or use a
handcart or similar device of adequate capacity.
If using a fork lift vehicle, secure the unit to a skid
before transporting.
11. Exericse good work practices.
The warnings,
precautions, and instructions discussed in this
instruction manual cannot cover all possible
conditions and situations that may occur. It must be
understood by the operator that common sense and
caution are factors which cannot be built into this
product, but must be considered by the operator.
WELDING SAFETY INSTRUCTIONS & WARNINGS
WARNING
PROTECT YOURSELF AND OTHERS FROM
POSSIBLE SERIOUS INJURY OR DEATH.
KEEP CHILDREN AWAY. READ THE OPERATING/
INSTRUCTION MANUAL BEFORE INSTALLING,
OPERATING OR SERVICING THIS EQUIPMENT.
HAVE ALL INSTALLATION, OPERATION,
MAINTENANCE, AND REPAIR WORK PERFORMED
BY QUALIFIED PEOPLE.
If an operator does not strictly observe all safety
rules and take precautionary actions, welding
products and welding processes can cause serious
injury or death, or damage to other equipment or
property.
Safe practices have developed from past
experience in the use of welding and cutting.
These practices must be learned through study
and training before using this equipment. Some of
these practices apply to equipment connected to
power lines; other practices apply to engine driven
equipment. Anyone not having extensive training in
welding and cutting practices should not attempt
to weld.
Safe practices are outlined in the European
Standard EN60974-1 entitled: Safety in welding
and allied processes.
WARNING
Only use safety equipment that has been approved
by an appropriate standards agency. Unapproved
safety equipment may not provide adequate
protection. Eye and breathing protection must be
AS/NZS compliant for the specific hazards in the
work area.
DANGER
Always wear AS/NZS compliant safety glasses and
a full face shield fitted with the appropriate filter
shade number. (Refer Filter Table on page 6.)
CAUTION
Heavy-duty work gloves, non-skid safety shoes and
hearing protection used for appropriate conditions
will reduce personal injuries.
CAUTION
Have the equipment serviced by a qualified repair
person using identical replacement parts. This will
ensure that the safety of the power tool is
maintained.
ZZZVWUDWDFRQ]