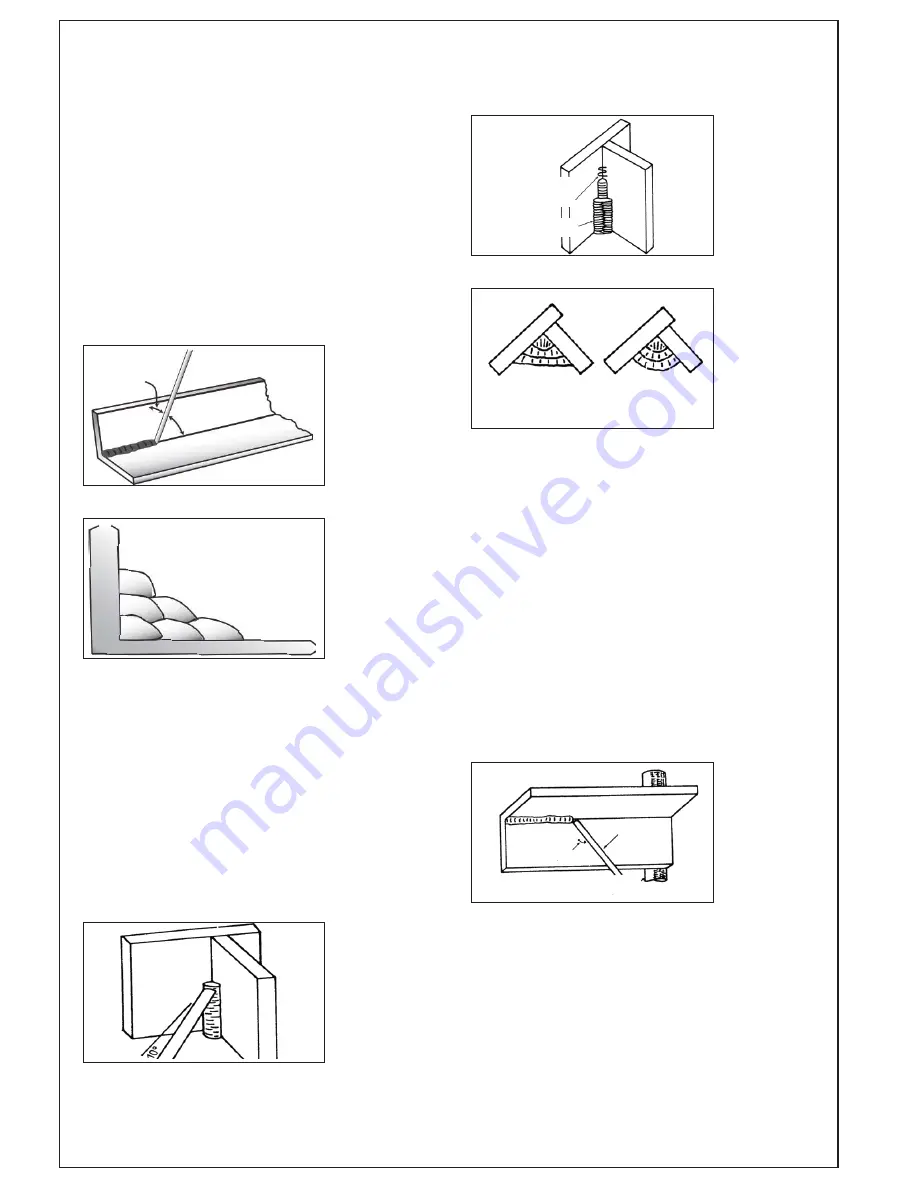
B. Fillet Welds
These are welds of approximately triangular cross-section made by depositing
metal in the corner of two faces meeting at right angles. Refer to Figure 1-14,
1-23 and 1-24.
A piece of angle iron is a suitable specimen with which to begin, or two lengths
of strip steel may be tacked together at right angles. Using a 3.2mm E7014 Stick
electrode at 100 amps, position angle iron with one leg horizontal and the other
vertical. This is known as a horizontal-vertical (HV) fillet.
Strike the arc and immediately bring the electrode to a position perpendicular
to the line of the fillet and about 45º from the vertical. Some electrodes require
being sloped about 20º away from the perpendicular position to prevent slag
from running ahead of the weld. Refer to Figure 1-23.
Do not attempt to build up much larger than 6.4mm width with a 3.2mm
electrode, otherwise the weld metal tends to sag towards the base, and
undercut forms on the vertical leg. Multi-runs can be made as shown in Figure
1-24. Weaving in HV fillet welds is undesirable.
Electrode Position for HV Fillet Weld (Fig 1-23)
45
o
from vertical
60
o
-70
o
from
line of weld
Multi-Runs in HV Fillet Weld (Fig 1-24)
1
3
6
5
2
4
C. Vertical Welds
1. Vertical Up
Tack weld a three feet length of angle iron to your work bench in an upright
position. Use a 3.2mm E7014 Stick electrode and set the current at 100 amps.
Make yourself comfortable on a seat in front of the job and strike the arc in the
corner of the fillet. The electrode needs to be about 10º from the horizontal to
enable a good bead to be deposited. Refer Figure 1-25.
Use a short arc, and do not attempt to weave on the first run. When the first
run has been completed de-slag the weld deposit and begin the second run
at the bottom. This time a slight weaving motion is necessary to cover the first
run and obtain good fusion at the edges.
At the completion of each side motion, pause for a moment to allow weld metal
to build up at the edges, otherwise undercut will form and too much metal
will accumulate in the centre of the weld. Figure 1-26 illustrates multi-run
technique and Figure 1-27 shows the effects of pausing at the edge of weave
and of weaving too rapidly.
Single Run Vertical Fillet Weld (Fig 1-25)
Multi Run Vertical Fillet Weld (Fig 1-26)
Weaving motion
for second and
subsequent runs
Pause at edge
of weave
Examples of Vertical Fillet Welds (Fig 1-27)
CORRECT
Pause at edge of
weave allows weld
metal to build up and
eliminates undercut
Note weld contour
when insufficient
pause at edge of
weave
INCORRECT
2. Vertical Down
The E7014 Stick electrode makes welding in this position particularly easy. Use
a 3.2mm electrode at 100 amps. The tip of the electrode is held in light contact
with the work and the speed of downward travel is regulated so that the tip of
the electrode just keeps ahead of the slag. The electrode should point upwards
at an angle of about 45º.
3. Overhead Welds
Apart from the rather awkward position necessary, overhead welding is not
much more difficult that down hand welding.
Set up a specimen for overhead welding by first tacking a length of angle iron
at right angles to another piece of angle iron or a length of waste pipe. Then
tack this to the work bench or hold in a vice so that the specimen is positioned
in the overhead position as shown in the sketch.
The electrode is held at 45º to the horizontal and tilted 10º in the line of travel
(Figure 1-28). The tip of the electrode may be touched lightly on the metal,
which helps to give a steady run. A weave technique is not advisable for
overhead fillet welds.
Use a 3.2mm E6013 Stick electrode at 100 amps, and deposit the first run by
simply drawing the electrode along at a steady rate. You will notice that the
weld deposit is rather convex, due to the effect of gravity before the metal
freezes.
Overhead Fillet Weld (Fig 1-28)
45
O
to plate
Tilted 10
O
in
line of travel
Angle tacked to pipe
ZZZVWUDWDFRQ]