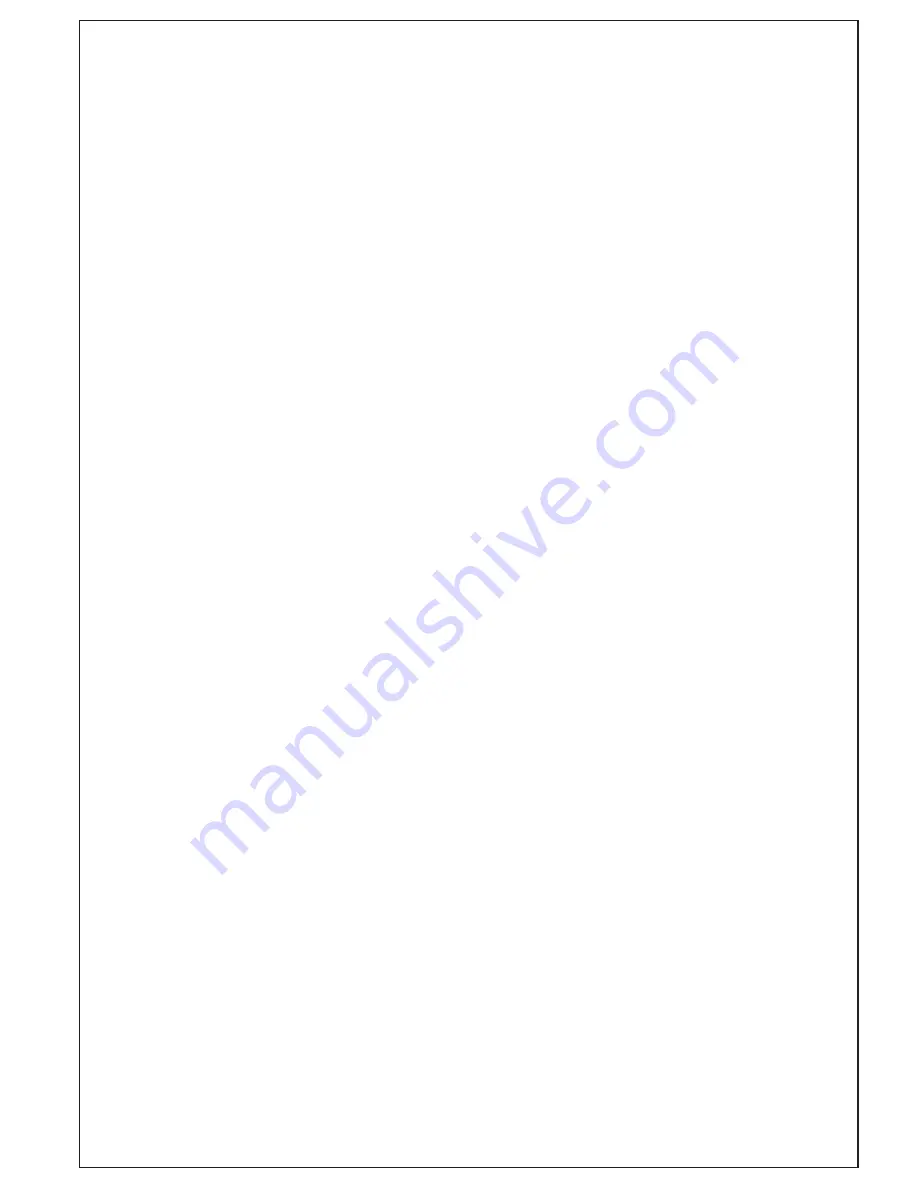
For flux cored ‘soft’ wire, such as that used in gasless MIG welding, the drive
roller groove has a serrated profile (knurled). For solid core ‘hard’ MIG wire, the
drive roller groove used has a ‘V’ shaped profile. For Aluminium solid core ‘soft’
MIG wire, the drive roller required has a ‘u’ shaped groove. If necessary, remove
and change the drive roller by unthreading the Drive Roller Retainer (28).
Once the correct Drive Rollers (27) are selected and fitted, manually feed the
wire through the Wire Drive Inlet Guide (24) through the drive roller grooves
and into the brass outlet wire guide tube. Ensuring that the wire is correctly
seated in the drive roller grooves, replace the Wire Feed Tension Arms (25) and
lock them into place by rotating the Wire Feed Tension Adjustment (26) to the
vertical position.
2. Adjusting Wire Feed Tension
Wind the knob on the Tension Adjustment (26). Clockwise will increase
tension, anti-clockwise will decrease drive tension. Ideal tension is as little as
possible, while maintaining a consistent wire feed with no drive roller slippage.
Before increasing wire feed tension, check all other causes of excess wire
feed friction first, such as: incorrect/worn drive roller, worn/damaged torch
consumables, and/or blocked/damaged torch wire guide liner. There is a
number scale on the Tension Adjuster (26) to indicate the adjustment position.
The higher the number, the higher the tension that is set.
CAUTION:
The use of excessive feed tension will cause rapid and premature
wear of the drive roller, the support bearing and the drive motor/ gearbox.
3. Connecting The Welder
Connect the MIG Torch Euro connector to the MIG torch Euro Connection
Socket (7) on the front of the machine. Secure by hand tightening (clockwise)
the threaded collar on the MIG Torch connector.
Re-check that the correct MIG wire, Drive Rollers (27) and MIG Torch tip are
fitted.
Connect the machine to suitable mains power using the Mains Input Power
Lead (21). Switch the Mains Power Switch (16) to ON to power up the machine.
Set the Welding Mode Switch (12) to MIG position, set the LIFT TIG Switch (13)
to OFF, set Spool Gun Switch (17) to OFF, set the Trigger Control Switch (14) to
‘2T’ position.
The
;0352
has an auto ‘soft start’ wire feed function. This means that until
the arc is started, using the torch trigger the wire feed will only run at a slow
speed, regardless where the Wire Feed Speed Control Adjustment Knob (5) is
set. The wire feed speed will ramp up to the selected speed on the knob once
the arc is started. This function serves 2 purposes. Firstly it gives a much
smoother start to the weld with the wire not starting full speed into the ‘cold’
weld pool. Secondly the soft start also limits the high inrush start up current
that is normally experienced by the power supply when the arc is first started,
putting less stress on the power supply circuit.
It is recommended to use the Wire Feed (Inching) Switch (15) to feed the
wire through the torch cable before welding. Activating the switch operates
the wire drive at full speed - it is much safer, as it does not activate the main
welding power circuit. With the tip removed from the torch and the torch laid
out as straight as possible, activate the Wire Feed (Inching) Switch (15) until
the wire feeds out through the end of the MIG Torch. Replace the tip on the
MIG Torch and trim off any excess wire.
4. Gasless Welding Operation - MIG (FCAW)
Connect the Work Lead/Clamp Quick Connector to the positive welding power
output socket (8). Connect the Clamp to the work piece. Contact with the work
piece must be firm with clean, bare metal, with no corrosion, paint or scale.
Connect the MIG power connection lead to the MIG Torch Power Connection
Socket (11) and the negative welding power output socket (9). Note if this
connection is not made, there will be no electrical connection to the welding
torch!
Set the Welding Voltage Adjustment Knob (4), Wire Speed Control Knob (5) and
Inductance Control Knob (6) to the desired positions.
You are ready to weld!
5. Gas Shielded Welding Operation - MIG (GMAW)
Connect the Work Lead/Clamp Quick Connector to the Negative Welding
Power Output Socket (9) Connect the clamp to the work piece. Contact with
the work piece must be firm with clean, bare metal, with no corrosion, paint or
scale.
Connect the MIG Power Connection Lead to the MIG Torch Power Connection
Socket (11) and the Positive Welding Power Output Socket (8). Note if this
connection is not made, there will be no electrical connection to the welding
torch!
Connect the gas regulator to a gas cylinder (not included with machine)
and connect the gas hose from the regulator to the Gas Inlet on the rear of
the machine (22). Ensure all hose connections are tight. Open gas cylinder
valve and adjust regulator, flow should be between 10-25 l/min depending on
application. Re-check regulator flow pressure with torch triggered as static
gas flow setting may drop once gas is flowing.
Set the Welding Voltage Adjustment Knob (4), Wire Speed Control Knob (5) and
Inductance Control Knob (6) to the desired positions.
You are ready to weld!
127(0,*ZHOGLQJZLWKDOXPLQLXPSURYLGHVDXQLTXHFKDOOHQJHGXHWR
WKHORZFROXPQVWUHQJWKRIDOXPLQLXPZHOGLQJZLUHyWKHDOXPLQLXPZLUH
GHIRUPVDVLWLVSXVKHGWKURXJKWKHWRUFKOLQHU*RRG0,*ZHOGLQJUHVXOWVDUH
GHSHQGHQWRQDVPRRWKZLUHIHHGE\PLQLPLVLQJIULFWLRQLVVXHV)RUDVWDQGDUG
tSXVKuIHGWRUFK675$7$UHFRPPHQGVDPD[LPXPWRUFKOHDGOHQJWKRI
PHWUHVZLWKDVSHFLDO7H
n
RQ39&OLQHUUDWKHUWKDQWKHFRQYHQWLRQDOVWHHO
OLQHU$OVRWKHFRUUHFWVW\OHGULYHUROOHUPXVWEHXVHGZLWKDQDOXPLQLXPW\SH
WRUFKFRQWDFWWLSRUDVWDQGDUGWLSLQRQHVL]HRYHUVL]HHJIRUPP
DOXPLQLXPZLUHXVHVWDQGDUGPPFRQWDFWWLS:KHQDPDFKLQHLV
IUHTXHQWO\VZDSSHGEHWZHHQDOXPLQLXPDQGVWHHOZHOGLQJLWLVTXLWHFRPPRQ
IRURSHUDWRUVWRKDYHDQH[WUD0,*7RUFKVSHFL
m
FDOO\VHWXSIRUHDFKVSHFL
m
F
XVHy$OXPLQLXPDQG6WHHO7KHKHDY\GXW\UROOHUJHDUHGZLUHIHHGHURIWKH
;0352
ZLOOH[KLELWDVPRRWKHUDQGPRUHFRQVWDQWZLUHIHHGZKHQ
FRPSDUHGWRVWDQGDUGUROOHUPDFKLQHV7RIXUWKHURYHUFRPHIULFWLRQLVVXHV
ZKHQZHOGLQJDOXPLQLXPXVHD6SRRO*XQ7KH
;0352
LVVSRROJXQ
FDSDEOHUHIHUIROORZLQJVHFWLRQIRUXVHZLWKD6SRRO*XQ
6. Spool Gun Operation
127(
6SRRO*XQLVDQRSWLRQDOH[WUDIRUWKH
;0352
Spool Gun Overview
The Spool Gun is a very useful addition to a MIG welder and can be used for
all types of MIG welding. A Spool Gun has two primary advantages over a
conventional ‘push’ wire feeder.
The main advantage is that the distance the wire has to travel is very short;
the shorter ‘push distance’ significantly reduces the wire feed friction, greatly
enhances wire feed smoothness and consistency, and results in improved
weld performance and quality. This is especially so with ‘soft’ wires such as
Aluminium, which is difficult to feed smoothly in welding machines equipped
with standard design wire feeders, even with special torch liners and relatively
short torch lengths.
The second advantage is that the gun can allow the use of small D100 wire
spools at a significant distance from the welding power source (This distance
is only limited by the length of the spool gun lead). This is advantageous for
high cost wire which is used infrequently, such as stainless steel or MIG
brazing wire, by saving on the initial outlay for a larger and more expensive
D200 or D300 spool.
Connect the Work Lead/Clamp Quick Connector to the Negative Welding
Power Output Socket (9) Connect the clamp to the work piece. Contact with
the work piece must be firm with clean, bare metal, with no corrosion, paint
or scale.
Connect the MIG Power Connection Lead to the MIG Torch Power Connection
Socket (11) and the Positive Welding Power Output Socket (8). Note: If this
connection is not effective, there will be no electrical connection to the
welding torch!
Connect the Spool Gun Interface Plug to the Spool Gun Connection Socket (10).
Set the Spool Gun Switch (17) to ON position.
Connect the gas regulator to a gas cylinder (not included) and connect the gas
hose from the regulator to the gas inlet on the rear of the machine (22). Ensure
all hose connections are tight. Open gas cylinder valve and adjust regulator,
flow should be between 10-25 l/min depending on application. Re-check
regulator flow pressure with torch triggered as the static gas flow setting may
drop once gas is flowing.
Set the Welding Voltage Adjustment Knob (4), Wire Speed Control Knob (5) and
Inductance Control Knob (6) to the desired positions.
You are ready to weld!
ZZZVWUDWDFRQ]