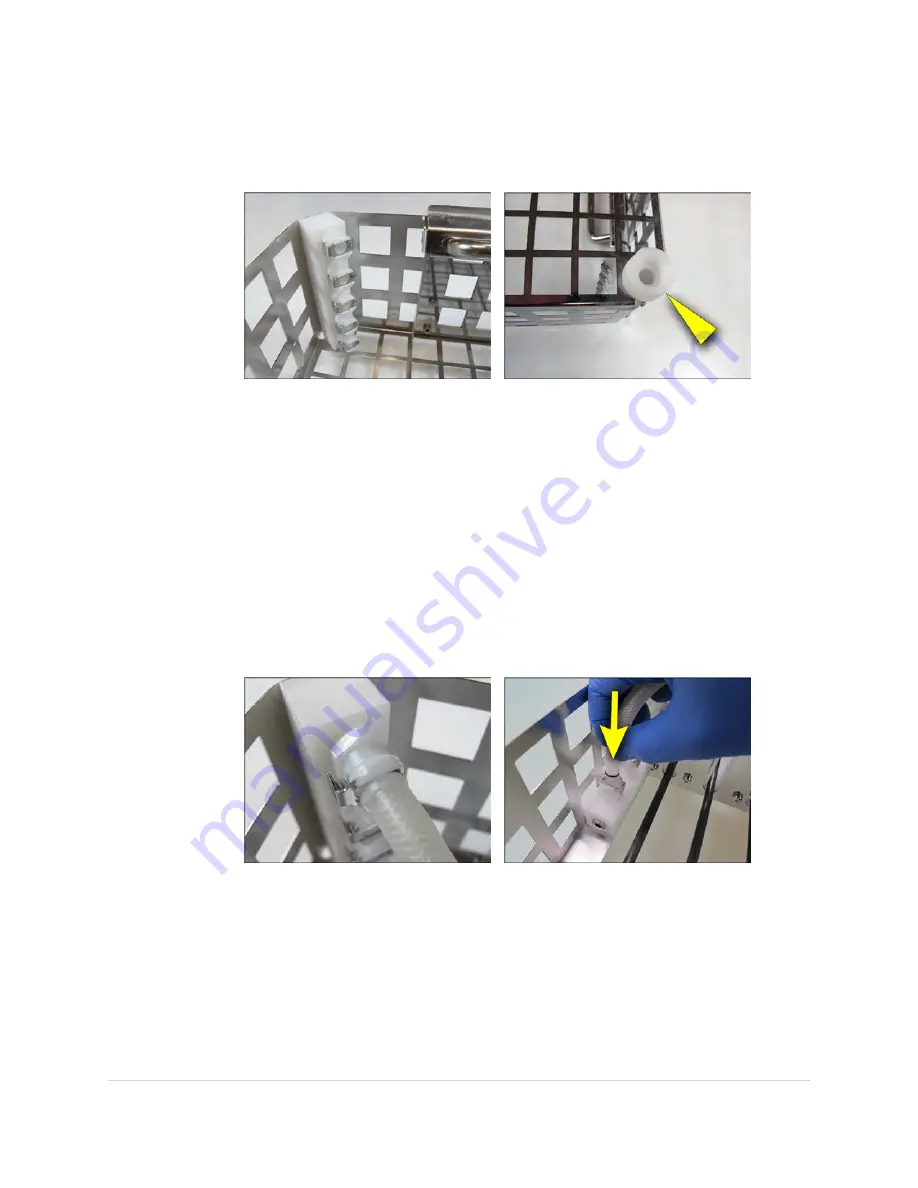
The basket manifolds connect with ports within the tank. If a connection is
compromised through damage to the manifold inlet, pressure to the flush ports is
lost, and instruments cannot be effectively irrigated.
5.2.3
Basket Flush Ports — Care
Basket flush ports should always be treated with care. Avoid impacting the flush
ports when loading and unloading instruments and at all other times. Only use luer
hoses and nozzles that are compatible with the basket type.
When attaching or detaching a luer hose or nozzle do not use excessive force to
push or pull the connector. Do not poke anything into a flush port, or use any tool to
detach nozzles or hoses.
If a nozzle or hose cannot be secured with the port retaining clip, the connection is
compromised and cannot be used. If a basket has any damaged flush ports, it
cannot be used and should be replaced.
34
USING INSTRUMENT BASKETS
InnoWave PCF Sonic Irrigator
Operator Manual
Summary of Contents for InnoWave PCF Sonic Irrigator
Page 1: ...InnoWave PCF Sonic Irrigator Operator Manual ENGLISH ...
Page 2: ......
Page 20: ...12 This page intentionally blank InnoWave PCF Sonic Irrigator Operator Manual ...
Page 86: ...78 This page intentionally blank InnoWave PCF Sonic Irrigator Operator Manual ...
Page 98: ...90 This page intentionally blank InnoWave PCF Sonic Irrigator Operator Manual ...
Page 110: ...102 This page intentionally blank InnoWave PCF Sonic Irrigator Operator Manual ...
Page 120: ...112 This page intentionally blank InnoWave PCF Sonic Irrigator Operator Manual ...
Page 138: ...130 This page intentionally blank InnoWave PCF Sonic Irrigator Operator Manual ...
Page 156: ...148 This page intentionally blank InnoWave PCF Sonic Irrigator Operator Manual ...
Page 160: ...152 APPENDICES InnoWave PCF Sonic Irrigator Operator Manual This page intentionally blank ...
Page 162: ...154 APPENDICES InnoWave PCF Sonic Irrigator Operator Manual This page intentionally blank ...
Page 164: ...156 APPENDICES InnoWave PCF Sonic Irrigator Operator Manual This page intentionally blank ...