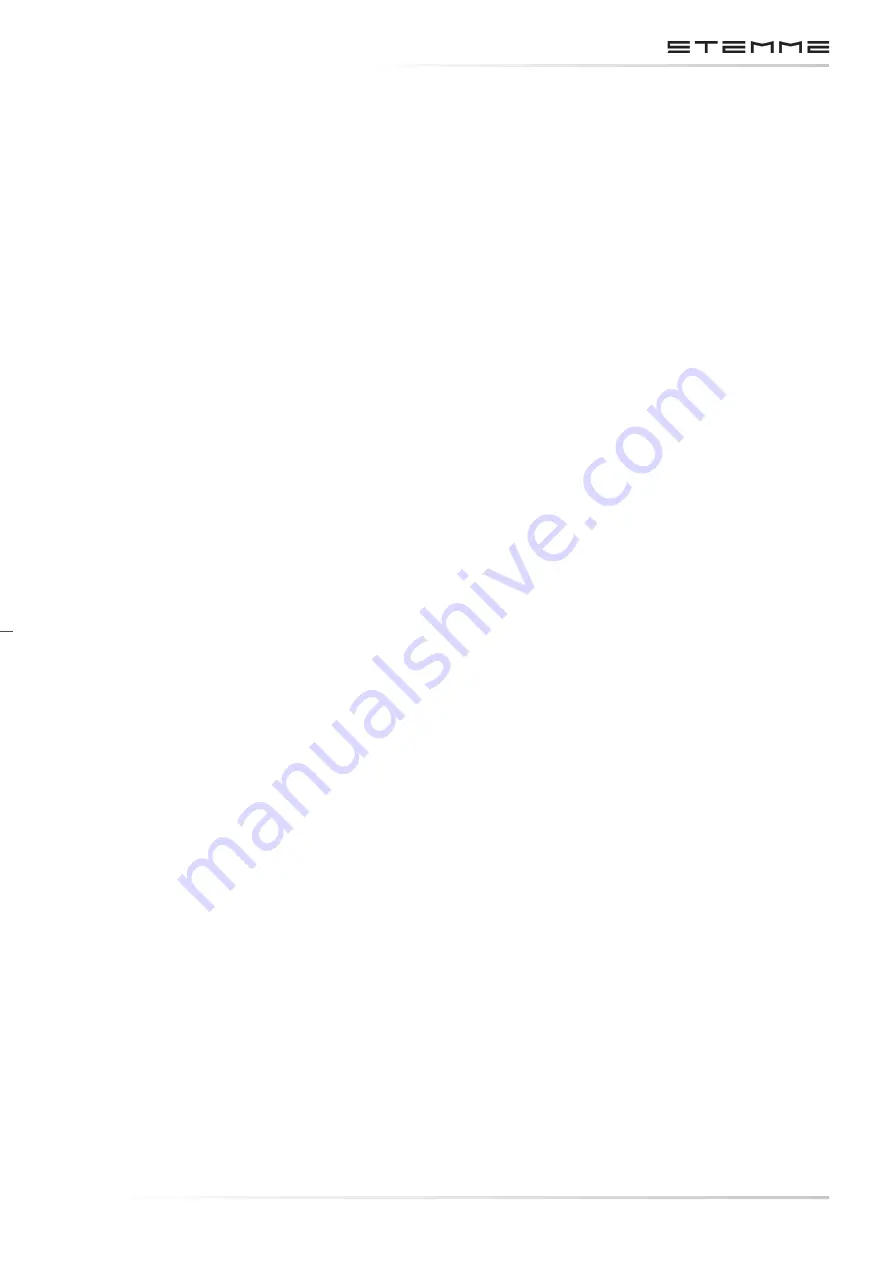
DOCUMENT NUMBER:
L500-912.820 ISSUE JUL 20, 2016
AMENDMENT: 00
DATE: --
CHAPTER-
PAGE 3-27
MAINTENANCE MANUAL STEMME S12
3.4.13 OPERATION MECHANISM OF THE PROPELLER FOLDING SYSTEM
3.4.13.1
NOSE-CONE
The nose-cone forms the fuselage nose in front of the cockpit section and covers the folded pro-
peller during flight in glider configuration. To change from gliding to powered flight, the nose-
cone can be shifted forward to allow the propeller unfold and rotate after starting the engine. In
the forward position locking and unlocking of the nose-cone lever simultaneously operates the
engine master switch (see section »3.7.11«).
The nose-cone consists of a CFRP shell, a GFRP frame and an aluminum tube, which provides sus-
pension of the nose-cone at the front fuselage. The aluminum tube is guided through the hollow
propeller drive shaft into an aluminum tubular guided pipe, including Teflon slip rings to allow
axial sliding of the nose-cone tube. The tubular guided pipe is firmly bonded to the GFRP guide
block in the forward cockpit.
Shifting the nose-cone is by means of the nose-cone handle, installed in the lower section of
the instrument panel (see figure »3.2.3.a«). The pull rod of the handle is connected to the nose-
cone sliding tube via a milled aluminum bracket, which is screwed to the rear tube terminal and
guided in a slot at the guide block. The bracket and the handle guide assy. prevent rotation of
the nose-cone. The handle assy. includes a spring which acts towards the locked (down) position
of the handle.
3.4.13.2
PROPELLER POSITIONING
The propeller positioning assy. allows rotation of the propeller drive shaft after engine shut down
and braking the propeller to a full stop, to the position so that the folded propeller fits into the
nose-cone contour. It is operated by a pull handle on the lower instrument panel next to the
propeller brake handle (see figure »3.2.3.a«).
The propeller positioning is driven by a Bowden cable. The bowden cable is routed from the handle
to and around an aluminum disc, which is pivoted on the guide block of the nose-cone sliding
tube in the forward cockpit. When the handle is pulled, the disc rotates against a circumferential
spring force until reaching a screw stop, which is adjustable and defines the final position of the
propeller. The spring is wound around the nose-cone guide block and rotates the disc back toward
its initial position when the handle is released.
A spring-loaded catch lever is installed on the disc and is connected to the bowden cable rotating
the disc. If not operated, the spring acts on the catch lever, so it is clear of the propeller brake
drum, mounted on the rear propeller drive shaft of the front gear. When the handle is pulled the
spring force unlocking the catch lever is over-balanced by the circumferential spring force acting
on the disc and the catch will engage in one of two notches of the brake drum, thus rotating
the drive shaft until reaching the screw stop of the disc. The two notches of the brake drum are
opposed; therefore the propeller rotates a maximum 180° as the handle is pulled to the stop.
Summary of Contents for S12
Page 1: ......
Page 3: ......
Page 97: ......
Page 238: ......
Page 240: ......
Page 242: ......
Page 244: ......
Page 246: ......
Page 248: ......
Page 250: ......
Page 255: ...A FLIGHT CONTROLS PITCH CONTROL AND TRIM ...
Page 256: ......
Page 257: ...B FLIGHT CONTROLS LATERAL CONTROL WING FLAP AILERON ...
Page 258: ......
Page 259: ...C FLIGHT CONTROLS AIRBRAKE CONTROL ...
Page 260: ......
Page 261: ...D FLIGHT CONTROLS RUDDER CONTROL ...
Page 262: ......
Page 263: ......
Page 264: ......
Page 265: ...E PROPULSION SYSTEM ...
Page 266: ......
Page 268: ......
Page 270: ......
Page 272: ......
Page 274: ......
Page 276: ......
Page 278: ......
Page 280: ......
Page 282: ......
Page 284: ......
Page 286: ......
Page 288: ......
Page 290: ......