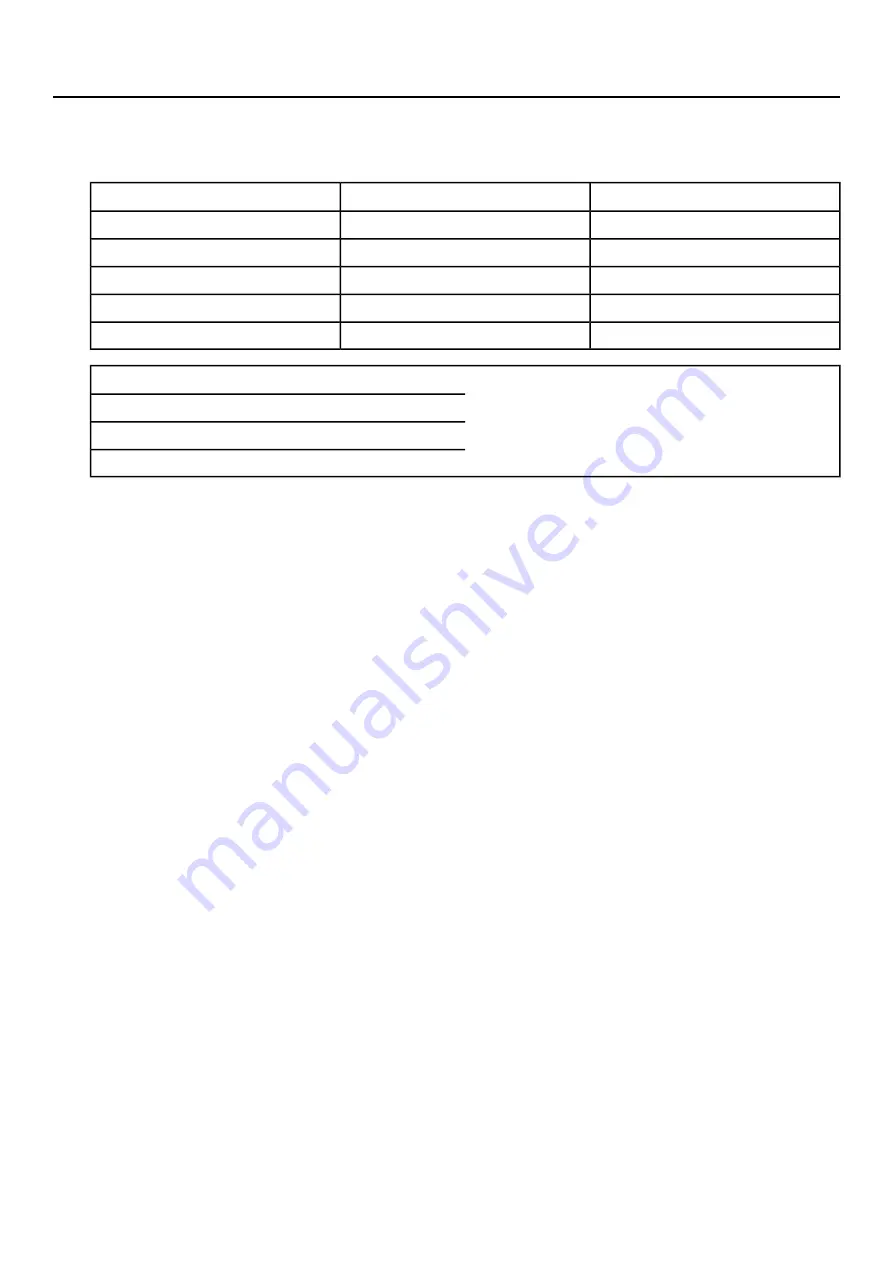
9.10. Feedback
Steelwrist continuously strives to improve products and processes.
If you have any remarks, suggestions for improvements or other views on this publication, please make a copy of
this page and post, fax or email it to us at one of the following addresses.
By Email
By Fax
By Letter
+46 (0)8 626 07 15
Steelwrist AB
Dept. Support
Bäckvägen 18
SE-192 54 Sollentuna
Sweden
From
Name:
Organization:
How we can reach you:
Regarding document number:__________________________
Page(s):__________________________________
Suggestion/Reason___________________________________________________________________________________
___________________________________________________________________________________________________
___________________________________________________________________________________________________
___________________________________________________________________________________________________
___________________________________________________________________________________________________
___________________________________________________________________________________________________
___________________________________________________________________________________________________
___________________________________________________________________________________________________
___________________________________________________________________________________________________
___________________________________________________________________________________________________
___________________________________________________________________________________________________
___________________________________________________________________________________________________
___________________________________________________________________________________________________
___________________________________________________________________________________________________
___________________________________________________________________________________________________
___________________________________________________________________________________________________
_________________________________________________________________________________________________
Date:_________________________________________
Name:_________________________________________
62
| User Manual tiltrotator with Front pin lock
™
| 9. Maintenance
Summary of Contents for Tiltrotator Front pin lock X04
Page 2: ......
Page 16: ......
Page 26: ......
Page 48: ......
Page 54: ......
Page 55: ...Chapter 8 8 Environmental aspects Topics Environmental information ...
Page 63: ......
Page 64: ...Steelwrist AB Bäckvägen 18 192 54 Sollentuna Sweden 46 626 07 00 www steelwrist com 700347ENA ...