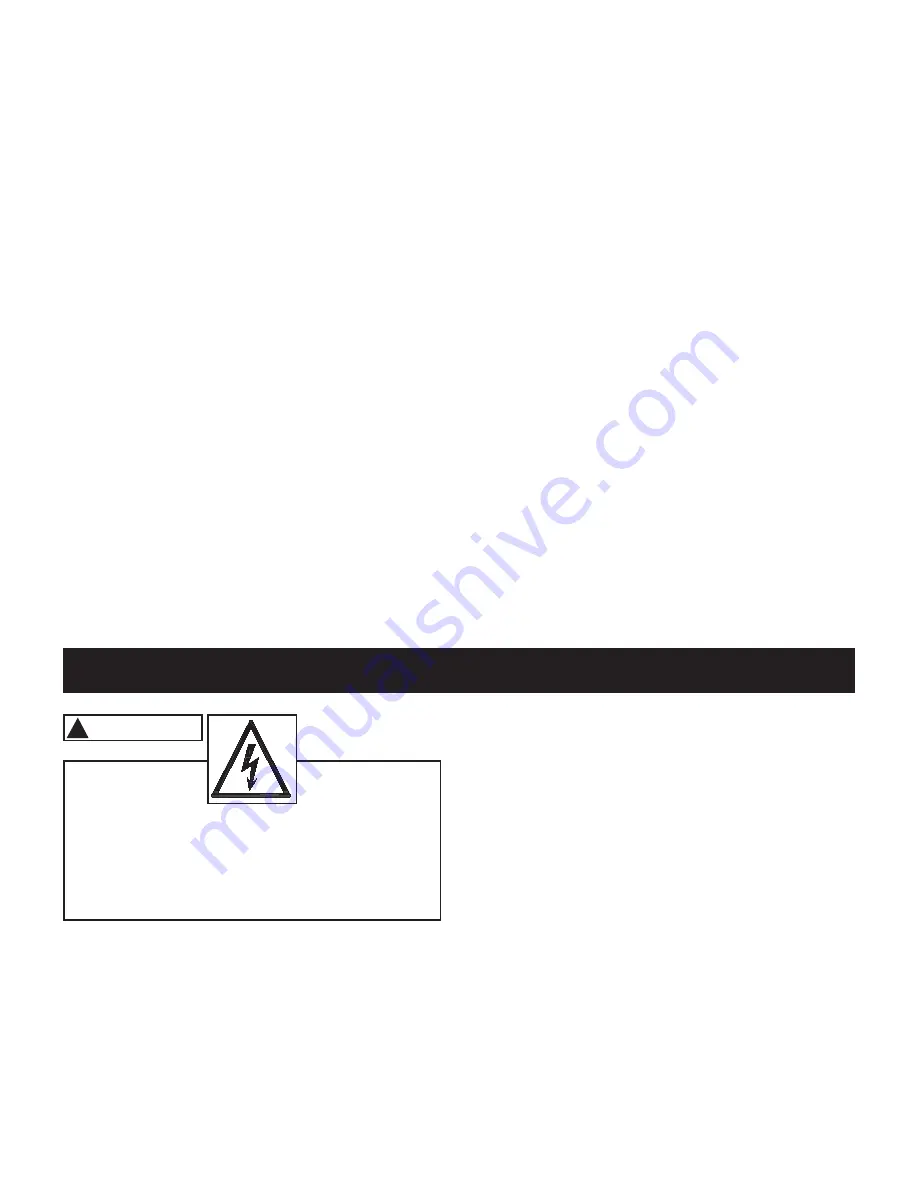
7
15.
ENSURE
that the machine sits firmly on the floor
before using. If the machine wobbles or is unstable,
correct the problem by using shims or blocks prior
to operation.
16.
MATCH
the blade type and size to the workpiece
being cut.
17.
MAKE SURE
that the blade tension is set appropri-
ately for the size of blade being used.
18.
MAKE SURE
that the blade is tracking properly by
manually turning the wheels before starting the
machine.
10.
USE
accessories only recommended by Steel City.
11.
DO NOT
pull the bandsaw by the power cord.
NEVER
allow the power cord to come in contact
with sharp edges, hot surfaces, oil or grease.
12.
DO NOT
unplug the bandsaw by pulling on the
power cord.
ALWAYS
grasp the plug, not the cord.
13.
REPLACE
a damaged cord immediately.
DO NOT
use a damaged cord or plug.
DO NOT USE
if the
bandsaw is not operating properly, or has been
damaged, left outdoors or has been in contact with
water.
14.
DO NOT
use the bandsaw as a toy.
DO NOT
use
near or around children.
19.
ADJUST
all blade guides as specifided in the
operating instructions.
20.
ADJUST
the upper guide to a point about 1/4”
above the workpiece being cut.
21.
DO NOT
cut workpieces that do not have a flat
bottom without properly supporting the piece to
maintain a stable position.
22.
KEEP
hand and fingers away from blade.
23.
HOLD
workpiece firmly and use a moderate feed
speed.
24.
MAKE
“relief” cuts before cutting curves.
25.
TURN OFF
machine before backing the workpiece
out of an incomplete cut.
26.
TURN OFF
the machine before removing scrap
pieces.
27. With the machine
TURNED OFF
, clean dust
build-up around lower blade guides regularly.
ELECTRICAL REQUIREMENTS
To reduce the risk of electric shock, follow all electri-
cal and safety codes, including the National Electric
Code (NEC) and the Occupational Safety and Health
Regulations (OSHA). All electrical connections and
wiring should be made by qualified personnel only.
WARNING
!
The switch provided with your saw is designed to func-
tion at 115 volts. The switch and saw come prewired for
115 volt operation.