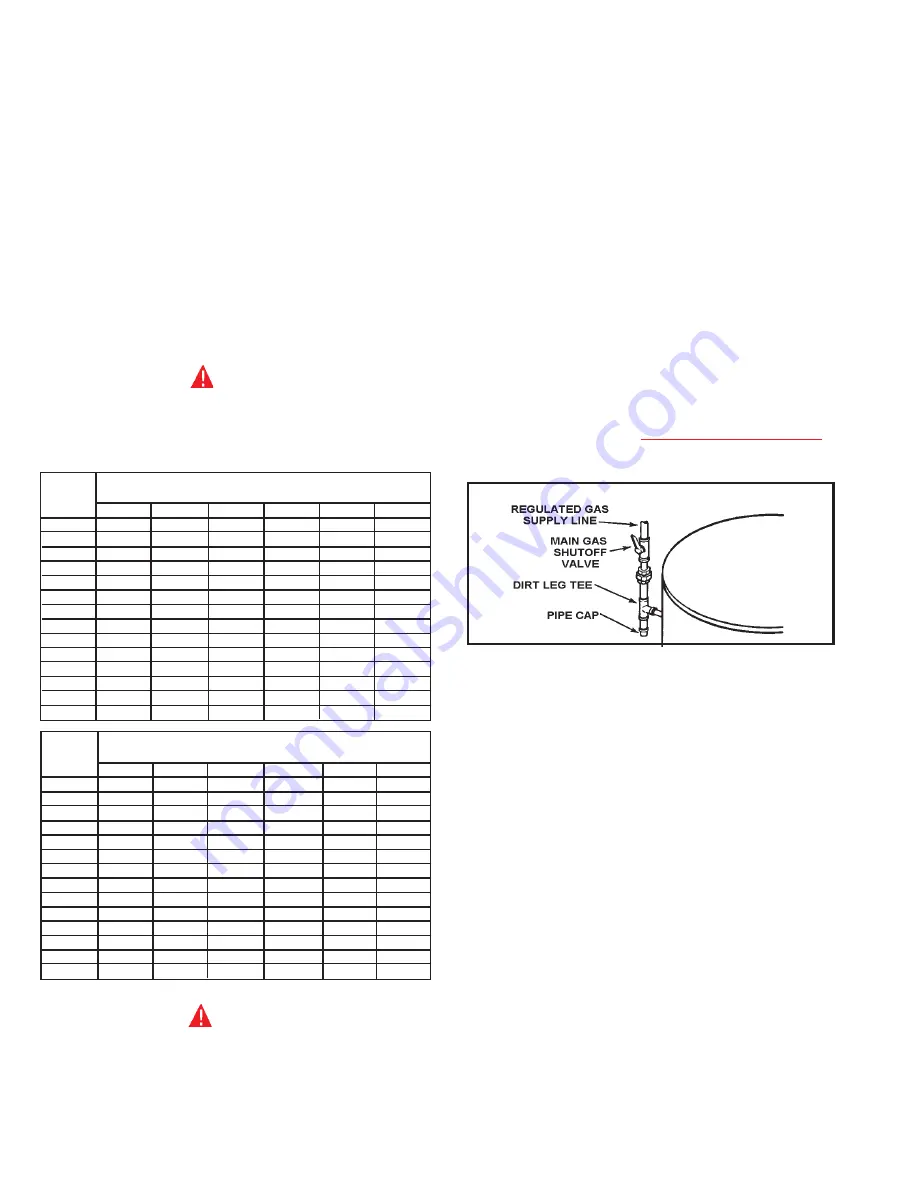
14
HOT SURFACE IGNITER
The Hot Surface Igniter is a device that ignites the main burner by
high temperature (>1800°F or >982°C). When 120VAC is applied
to the igniter, sufficient heat is generated to ignite the main burner.
Although improvements have been made to strengthen the igniter,
it is fragile and care must be taken when handling the igniter to
prevent breakage.
GAS PIPING
Contact your local gas service company to ensure that adequate
gas service is available and to review applicable installation codes
for your area.
Size the main gas line in accordance with Table 3. The figures
shown are for straight lengths of pipe at 0.5 in. W.C. (125Pa)
pressure drop, which is considered normal for low pressure
systems Note that fittings such as elbows and tees will add to the
pipe pressure drop.
CAUTION
DO NOT USE FLEXIBLE GAS PIPING.
TABLE 3. MAXIMUM CAPACITY OF PIPE IN CUBIC FEET OF GAS
PER HOUR (Based upon a Pressure Drop of 0.5 inch Water Column
and 0.6 Specific Gravity Gas and max. gas pressure of 0.5 psig).
WARNING
THE HEATER IS NOT INTENDED FOR OPERATION AT HIGHER
THAN 11.0" WATER COLUMN (2.74 Kpa) FOR NATURAL GAS
AND 14.0" W.C. (3.49kPa) FOR PROPANE GAS SUPPLY
PRESSURE. HIGHER GAS SUPPLY PRESSURES REQUIRE
SUPPLEMENTAL REDUCING SERVICE REGULATION.
EXPOSURE TO HIGHER GAS SUPPLY PRESSURE MAY CAUSE
DAMAGE TO THE GAS CONTROLS WHICH COULD RESULT IN
FIRE OR EXPLOSION. IF OVERPRESSURE HAS OCCURRED
SUCH AS THROUGH IMPROPER TESTING OF GAS LINES OR
EMERGENCY MALFUNCTION OF THE SUPPLY SYSTEM THE
GAS VALVE MUST BE CHECKED FOR SAFE OPERATION. MAKE
SURE THAT THE OUTSIDE VENTS ON THE SUPPLY
REGULATORS AND THE SAFETY VENT VALVES ARE
PROTECTED AGAINST BLOCKAGE. THESE ARE PARTS OF
THE GAS SUPPLY SYSTEM, NOT THE HEATER. VENT
BLOCKAGE MAY OCCUR DURING ICE STORMS. IT IS
IMPORTANT TO GUARD AGAINST GAS VALVE FOULING
FROM CONTAMINANTS IN THE GAS WAYS. SUCH FOULING
MAY CAUSE IMPROPER OPERATION, FIRE OR EXPLOSION.
IF COPPER SUPPLY LINES ARE USED THEY MUST BE
INTERNALLY TINNED AND CERTIFIED FOR GAS SERVICE.
BEFORE ATTACHING THE GAS LINE BE SURE THAT ALL GAS
PIPE IS CLEAN ON THE INSIDE.
TO TRAP ANY DIRT OR FOREIGN MATERIAL IN THE GAS SUPPLY
LINE, A DIRT LEG (SOMETIMES CALLED A SEDIMENT TRAP OR
DRIP LEG) MUST BE INCORPORATED IN THE PIPING (SEE FIG.
14). THE DIRT LEG MUST BE READILY ACCESSIBLE AND NOT
SUBJECT TO FREEZING CONDITIONS. INSTALL IN
ACCORDANCE WITH RECOMMENDATIONS OF SERVING GAS
SUPPLIERS. REFER TO THE NATIONAL FUEL GAS CODE OR
THE NATURAL GAS AND PROPANE INSTALLATION CODE CSA
B149.1.
FIGURE 14.
CONNECTION OF GAS PIPE
1. When connecting gas pipe to unit, apply wrench to flange only.
Note: Do not use wrench on gas valve or gas bracket.
2. PERFORM THE GAS LEAK TEST ANY TIME WORK IS DONE
ON A GAS SYSTEM TO AVOID THE POSSIBILITY OF FIRE OR
EXPLOSION WITH PROPERTY DAMAGE, PERSONAL INJURY
OR LOSS OF LIFE.
The Gas Leak Test is performed as follows: Paint pipe connections
upstream of gas control with a rich soap and water solution to test
for leaks before operating main burner. Bubbles indicate gas leak.
To stop leak, tighten pipe connections. After piping connections are
checked, turn on main burner. With main burner in operation, paint
pipe joints (including flanges), pilot gas tubing connections and
control inlet and outlet with rich soap and water solution. Bubbles
indicate gas leak. To stop leak, tighten flange screws, joints and
pipe connections. Replace part if leak can’t be stopped.
To prevent damage, care must be taken not to apply too much torque
when attaching gas supply pipe to gas valve inlet.
Apply joint compounds (pipe dope) sparingly and only to the male
threads of pipe joints. Do not apply compound to the first two threads.
Use compounds resistant to the action of liquefied petroleum gases.
DISCONNECT THE APPLIANCE AND ITS MANUAL GAS SHUTOFF
VALVE FROM THE GAS SUPPLY PIPING SYSTEM DURING ANY
SUPPLY PRESSURE TESTING EXCEEDING 1/2 PSIG (3.45Kpa). GAS
SUPPLY LINE MUST BE CAPPED WHEN DISCONNECTED FROM
LENGTH
NORMAL IRON PIPE SIZES (INCHES)
IN
INPUT IN THOUSANDS BTU/HR
FEET
1 1/4"
1 1/2"
2"
2 1/2"
3"
4"
10
1400
2100
3960
6300
11000
23000
20
950
1460
2750
4360
7700
15800
30
770
1180
2200
3520
6250
12800
40
660
990
1900
3000
5300
10900
50
580
900
1680
2650
4750
9700
60
530
810
1520
2400
4300
8800
70
490
750
1400
2250
3900
8100
80
460
690
1300
2050
3700
7500
90
430
650
1220
1950
3450
7200
100
400
620
1150
1850
3250
6700
125
360
550
1020
1650
2950
6000
150
325
500
950
1500
2650
5500
175
300
460
850
1370
2450
5000
200
430
800
1280
2280
4600
LENGTH
NORMAL IRON PIPE SIZES (INCHES)
IN
INPUT IN KW
METERS
1 1/4"
1 1/2"
2"
2 1/2"
3"
4"
3.0
410
615
1160
1845
3221
6735
6.1
278
428
805
1277
2255
4626
9.1
225
346
644
1031
1830
3748
12.2
193
290
556
878
1552
3192
15.2
170
264
492
776
1391
2840
18.3
155
237
445
703
1259
2577
21.3
143
220
410
659
1142
2372
24.4
135
202
381
600
1083
2196
27.4
126
190
357
571
1010
2108
30.5
117
182
337
542
952
1962
38.1
105
161
299
483
864
1757
45.7
95
146
278
439
776
1610
53.3
88
135
249
401
717
1464
61.0
126
234
375
688
1347