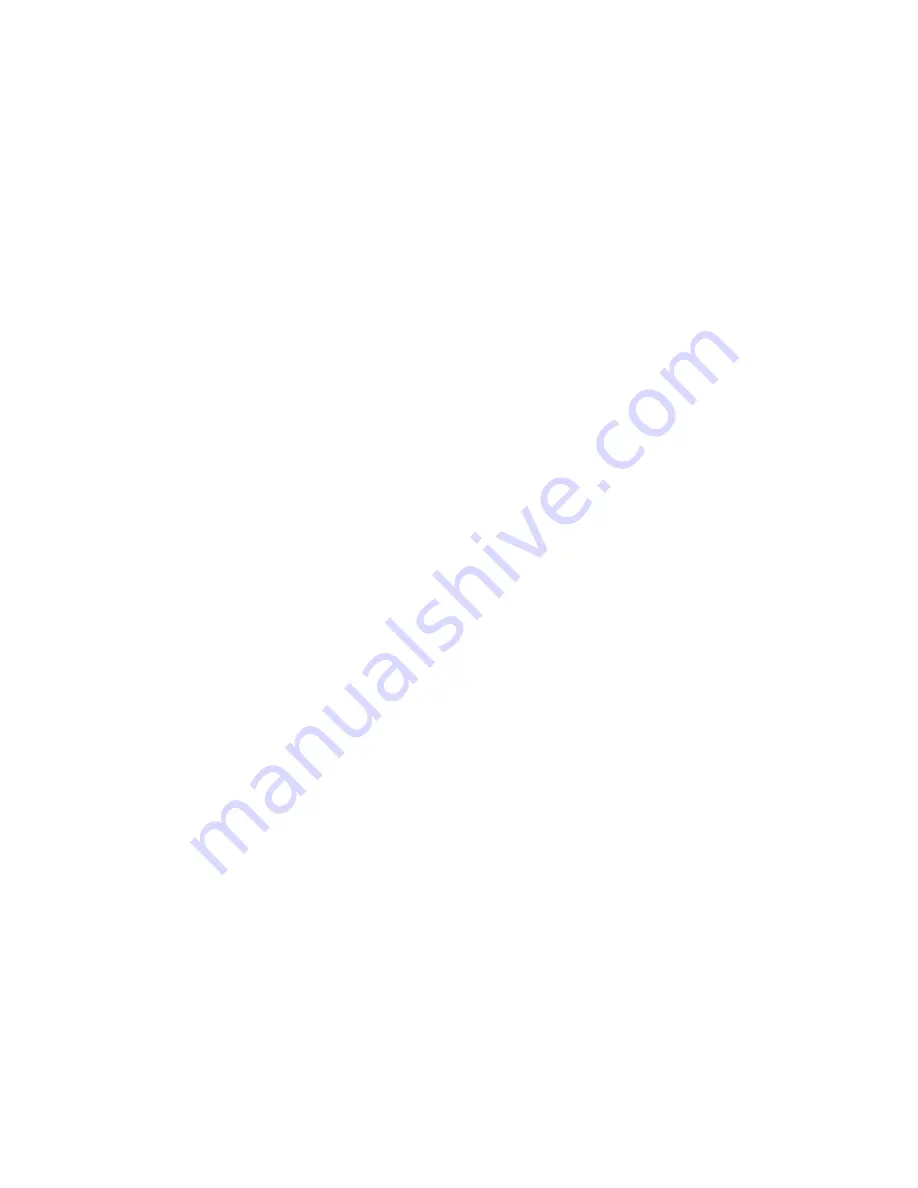
- 11 -
2.2 Component
Description
1) System
Computer.
Runs MetLogix M3-CNC software under Windows 7 professional. The
computer is an 24” touch screen monitor and PC for AV300 M3 systems, or a rack-mount PC with
a separate 24” touch-screen monitor for AV350 and AV450 M3 systems. In either case, the PC is
connected to the system’s video camera via a first USB cable and to the system’s M3 controller
via a second USB cable. The monitor displays parts views, geometrical constructs, and readings.
Operator inputs can be via the PC’s touch-screen or a wireless keyboard and mouse. M3
software operation is provided in a separate M3 manual by MetLogix.
2) MetLogix M3 CNC Control Unit.
Interfaces all-in one PC to metrology unit. Reads liner enco-
ders, reads output of joystick and trackball unit, drives motors for CNC operation, and controls
lighting. Located on benchtop or inside workstation (AV300), or inside machine pedestal (AV350
and AV450).
3) Metrology System Base.
Cast aluminum for AV300, granite for AV350 and AV450.
4) X-Y
Stage.
Motorized with DC servo or stepper motors under control of M3 CNC software. Made
from precision machined aluminum. Surface mounting holes allow customer-designed fixtures for
part support. Travel is 300 x 150 mm (12” x 6”) for AV300, 350 x 350 mm (14” x 14”) for AV350,
and 450 x 350 mm (18” x 14”) for AV450.
5) Z-Column.
Motorized with DC servo or stepper motors under control of M3 CNC software.
Supports video probe and ring light, which can be a fixed ring light or Dark Field Quad (QDF) ring
light on a motorized Z-track. Height adjustment is 135 mm (5.5”) for AV300, and 200 mm (8”) for
AV350 and AV450.
6) Optical Probe Assembly.
Captures the part image for display and for video edge detection
(VED). The imaging system, as ordered, can be a 1.3 Mpixel color CCD camera with factory
installed 6.5:1 or 12:1 zoom optics, or a 2 Mpixel color video camera with a bayonet lens mount
which accepts 6.5:1 motorized zoom optics or any of six available fixed-magnification telecentric
lenses (0.30X, 0.50X, 0.80X, 1.0X, 2.0X, 4.0X). The bayonet mount allows quick change of optics.
The settings of the video camera are preset at the factory and should not be modified. For all
optics, focus is determined by the height of the optical probe over the surface to be analyzed. This
height is controlled by M3 software. For the zoom optics, an optional 0.5X auxiliary lens can
double the field of view while cutting magnification in half, and optional 1.5X and 2.0X auxiliary
lenses can increase magnification by 1.5X or 2.0X while reducing the field of view.
7) Surface Illumination.
Provided by ring lighting at the base of the optical probe. The standard ring
light is fixed to the optical probe and provides even illumination from all directions. The light source
can be LEDs in the ring or a 150W quartz-halogen lamp with fiber-optic delivery, as ordered. An
optional quad bright-field LED ring light alternative allows LED intensity to be individually adjusted
in four quadrants. An optional add-on LED quad dark-field (QDF) ring light can fit around the
standard LED ring light. It allows LED intensity to be individually adjusted in four quadrants and
can further be adjusted in height by 100 mm (4”) under CNC control by M3 software. Intensity con-
trol of all lighting alternatives is via M3 software for repeatable illumination.
8) Coaxial
Illumination.
Provides surface illumination along the optical axis of the camera.
Achieved by applying light from the side via a beam-splitting mirror at the base of the optical
probe. The light source can be LEDs or a 150W quartz-halogen lamp with fiber-optic delivery, as
ordered. Intensity control of both lighting alternatives is via M3 software.
9) Silhouette Illumination.
Provided by a sub-stage light. The light source can be LEDs in the sub-
stage light or a 150W quartz-halogen lamp with fiber-optic delivery, as ordered. Intensity control of
both lighting alternatives is via M3 software.