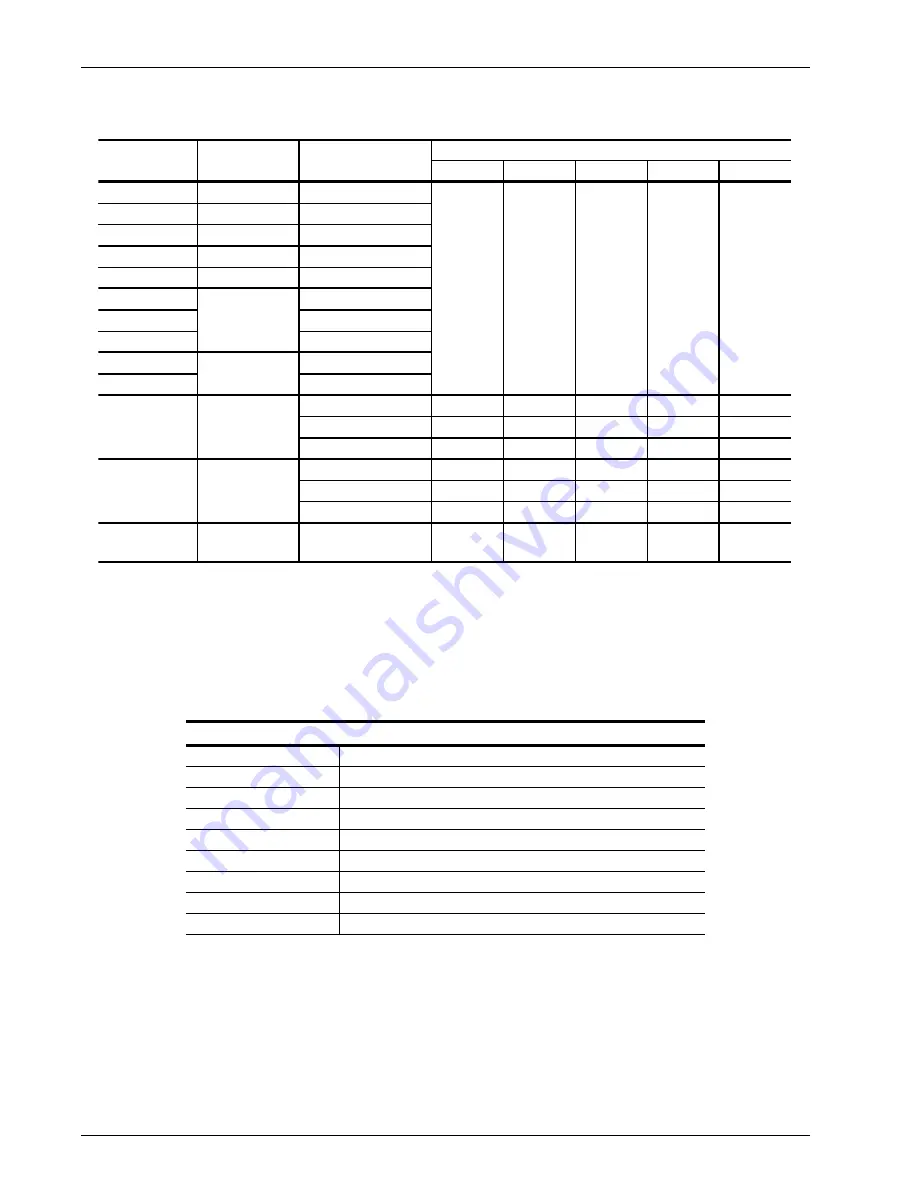
6x84
6x72
6x48
6x36
6x24
410SS
LL900127
CELCON
LL900129
BRASS
LL916284
17-7 SS
LL900124
PEEK
LL118683
410SS
LL125801
BRASS
LL918089
17-7 SS
LL919100
CELCON
LL900133
PEEK
LL121856
N/A
8
4
N/A
2
128675M1
N/A
2
2
N/A
N/A
128675M2
N/A
2
2
N/A
N/A
LL926752
N/A
8
4
N/A
2
LL926752M1
N/A
2
2
N/A
N/A
LL926752M2
N/A
2
2
N/A
N/A
POLY
For 5-1/4”
shaft only
LL3005185
N/A
12
8
N/A
2
HE100-004
QUANTITY
MATERIAL
REMARKS
PART NO.
DELRIN
16
12
8
For 5-1/4”
shaft only
For 5-1/4”
shaft only
28
24
410SS
Open Style
with holes
Open Style
PART NUMBER
DESCRIPTION
LL927603
Corrosion Prevention
LL725499
Caution/Warning Shaft Guard
LL119170
Danger - Contents Under Pressure
LL125098
3-A Label
LL119169
Safety Instructions
LL930514
SPX/WCB Logo Horizontal
LL930513
SPX/WCB Logo Vertical
LL931360
Caution/Warning Product Head Locking Latch (Vertical)
LL931407
Caution/Warning Product Head Locking Latch (Vertical)
Parts Lists
Waukesha Cherry-Burrell
Page 78
95-03057
11/2012
Votator II Blades
Labels