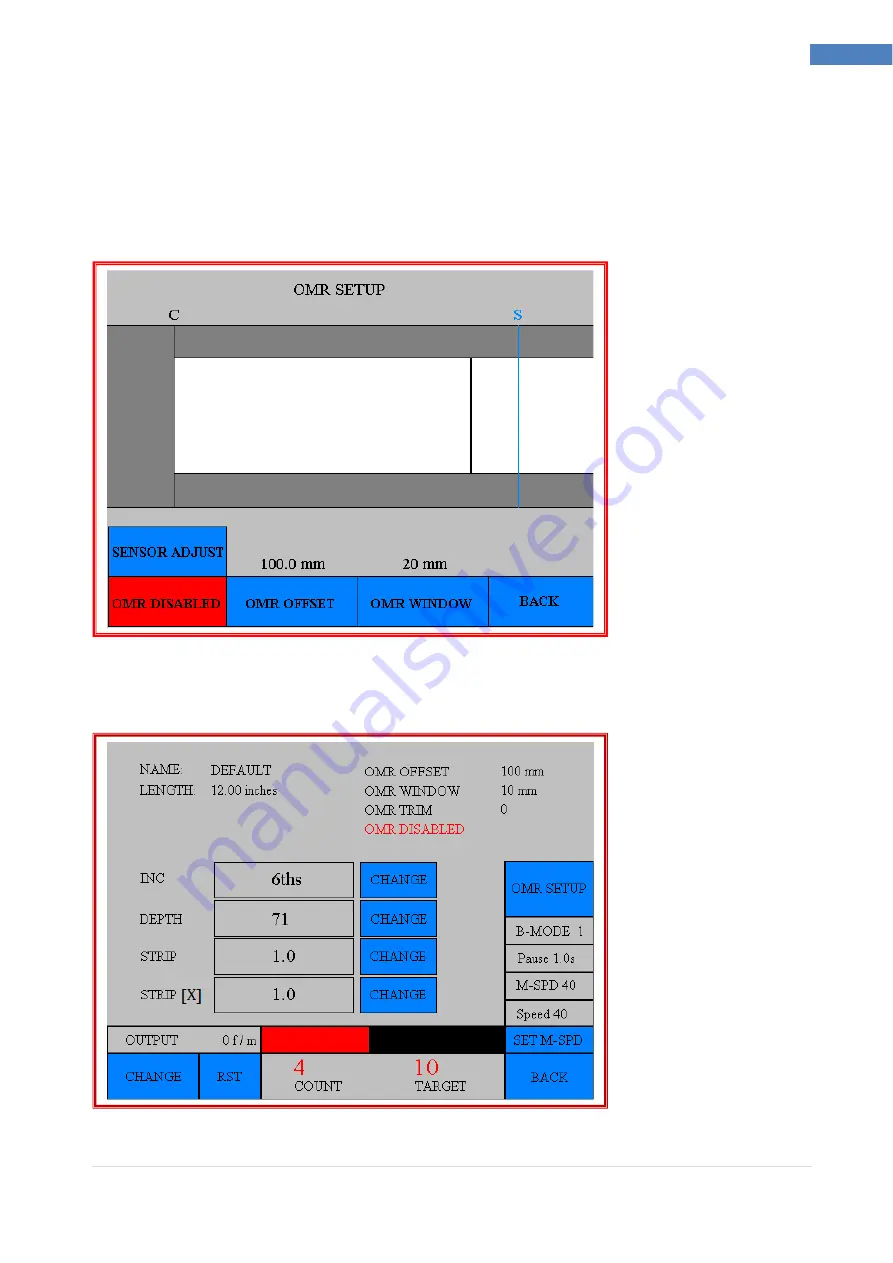
39 |
S p e d o 2 6 0 0 O p e r a t o r M a n u a l
S p e d o U K L t d
39
Spedo 2600 Pinless Cutter Operator Manual
ENABLE/DISABLE the OMR sensor:
It is possible to run the 2600 Forms Cutter without using the OMR registration sensor active. This should
only be done where small a quantity of unprinted stock needs to be run though during the setup process.
Running with the OMR registration sensor disabled during production is not recommended as registration
of the forms will be lost.
To ENABLE or DISABLE the OMR registration sensor press the OMR ENABLE/DISABLED button.
The button will turn red when the sensor is disabled. Press the BACK button the return to the job setup
screen to run the cutter with the sensor disabled.