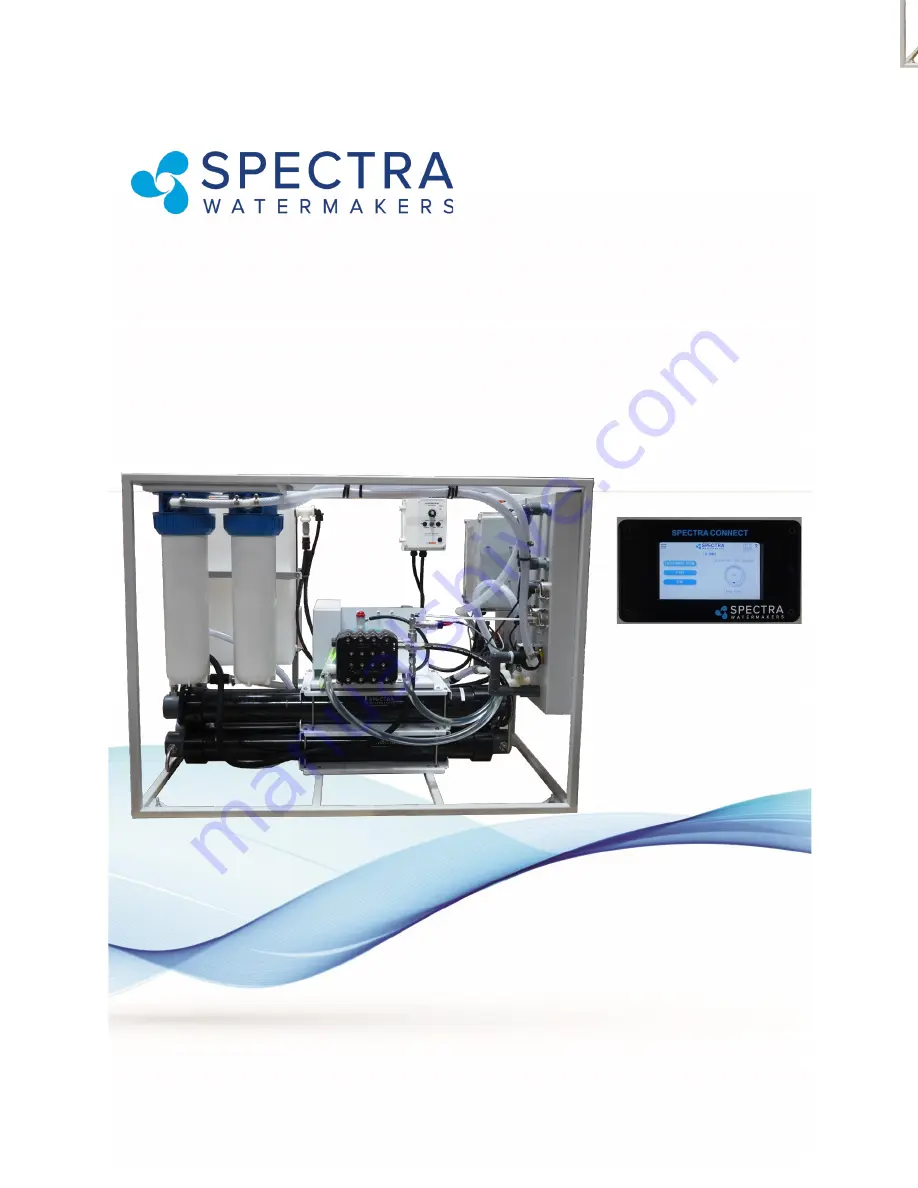
Spectra Watermakers
Katadyn Desalination LLC.
2220 S. McDowell Blvd. Petaluma, CA 94954
Phone: 415-526-2780 Fax: 415-526-2787
[email protected]
www.spectrawatermakers.com
Updated August 2019 from S/N 5566
LB-1800C
LB-2800C
LB-4000C
Watermakers with Spectra Connect
Installation and Operating Manual
Summary of Contents for LB-1800C
Page 2: ...2 Page Intentionally blank...
Page 4: ...4 Page Intentionally blank...
Page 33: ...33 Black Parker tube fittings...
Page 34: ...34 John Guest Super Speedfit Fittings...
Page 48: ...48...
Page 49: ...49...
Page 50: ...50...
Page 51: ...51...
Page 52: ...52...