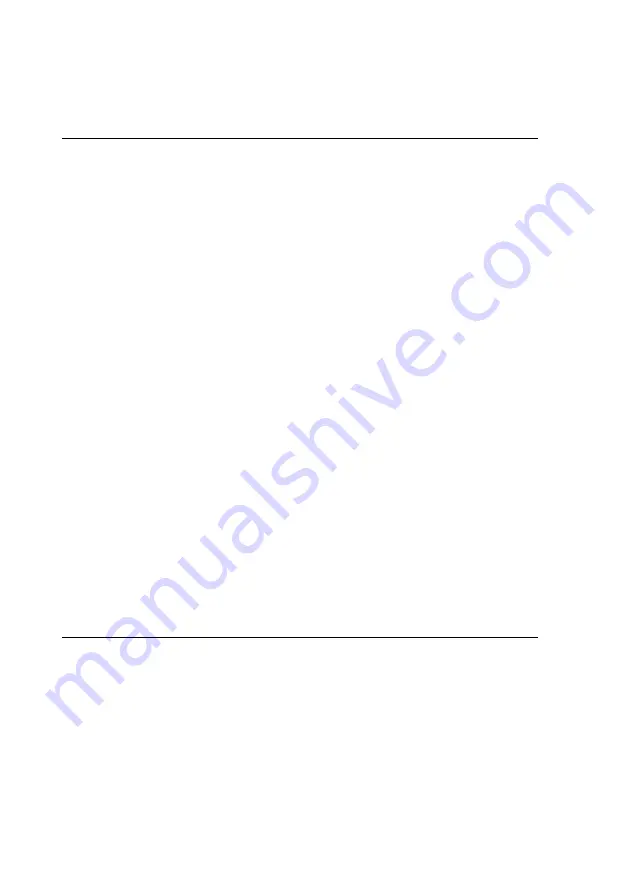
User Manual
42
9. Legend – Bubble Number Part Identification
(
1
) Thermal cut-off switch.
(
2
) Top cooling block assembly.
(
3
) Lower cooling block assembly.
(
4
) Top heated pressing surface chamber.
(
5
) Lower heated pressing surface assembly.
(
6
) Quick Connect body coupling.
(
7
) Quick Connect insert coupling.
(
8
) Top bolster pressing surface (of the lead screw).
(
9
) Lead screw (of the Press).
(
10
) Safety guard lower screw stop (of Manual Hydraulic Press).
(
11
) Safety guard lifting knob (of Manual Hydraulic Press).
(
12
) Loading handle of High Temperature Film Maker Accessory.
(
13
) Top polished pressing surface.
(
14
) Lower polished pressing surface.
(
15
) Side support bracket.
(
16
) Lifting handle on Top Half Assembly (of Film Maker Accessory).
(
17
) Top resting slot in side support bracket.
(
18
) Spacer ring.
(
19
) Lower pressing piston surface (of Press).
(
20
) Spacer bar (aluminium cylinder block).
(
21
) Aluminium foil disc (40mm diameter).
(
22
) Aluminium foil sample cup.
(
23
) Aluminium foil sample cup cover.
(
24
) Cup making tool.
(
25
) Foam pad for cup making tool.
10. Spares and Consumables
P/N GS15627 Packet of (200) aluminium foils (40mm diameter).
P/N GS15805 Atlas™ High Temperature Film Maker Accessory
replacement spacer rings (set of 6 – sizes A to F).
P/N GS03800 Packet of (100) Specacards (25mm diameter aperture).
P/N GS03810 Packet of (100) Specacards (10mm x 25mm aperture).
P/N GS03820 Magnetic film holder (25mm diameter aperture).
Summary of Contents for Atlas GS15800
Page 1: ...Atlas High Temperature Film Maker Accessory User Manual 2I 15800 Issue 15...
Page 2: ......
Page 3: ...Atlas High Temperature Film Maker Accessory User Manual 2I 15800 Issue 15...
Page 45: ...Atlas High Temperature Film Maker Accessory 43...
Page 46: ...User Manual 44 Notes for Use of Atlas High Temperature Film Maker Accessory...