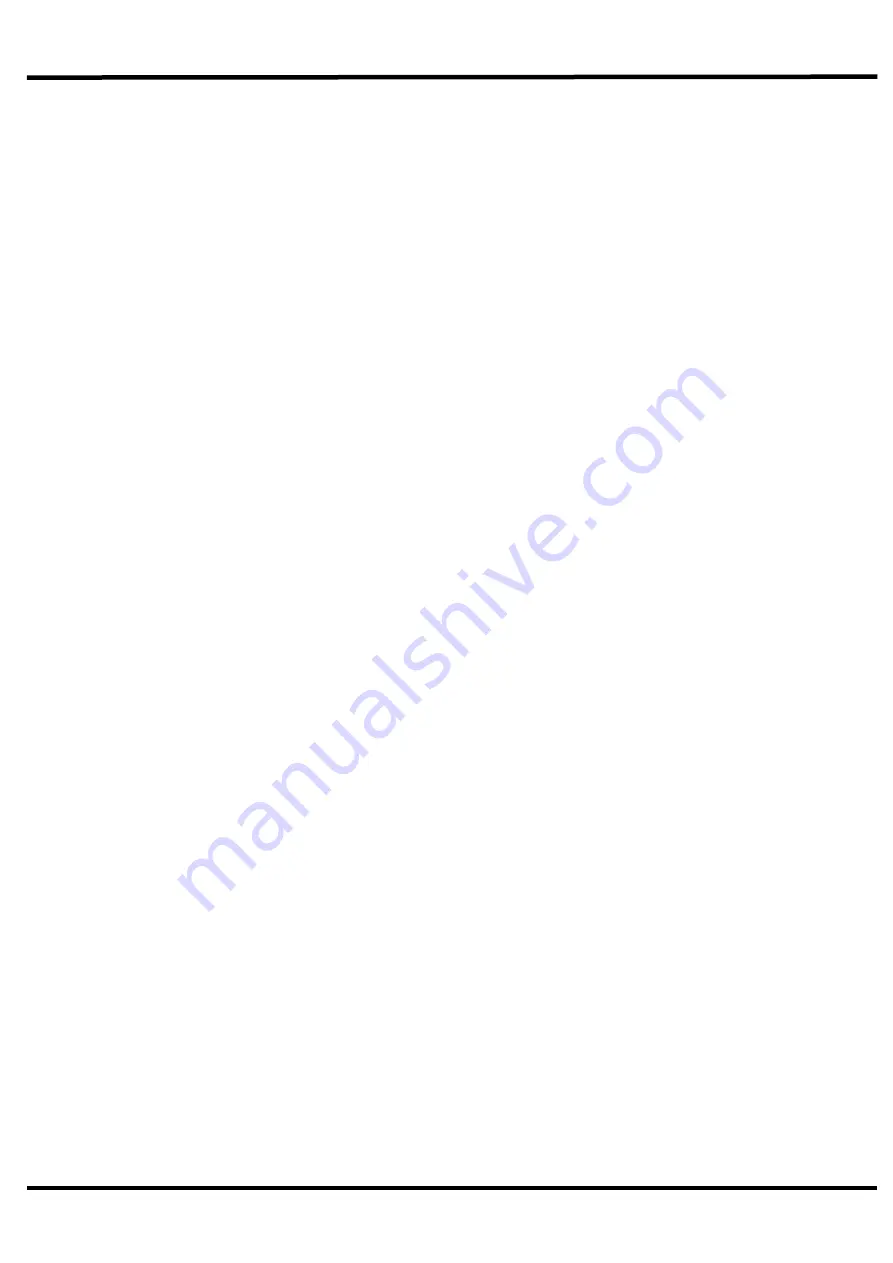
Spearhead Swipe
E
150/
E
180/
E
210
24
24
24
24
Extended Warranty
Extended Warranty
Extended Warranty
Extended Warranty
As an extension to the 12-month warranty set out above, Spearhead will provide an
additional 12-month warranty cover subject to the Spearhead Warranty Conditions
above and the Extended Warranty Conditions below.
Extended Warranty Conditions
Extended Warranty Conditions
Extended Warranty Conditions
Extended Warranty Conditions
1. The extended warranty applies to hydraulic pumps, motors, valves and
gearboxes only. It does not apply to other parts, to consumables such as
lubricants, seals or filters or to labour charges.
2. The machinery must have had an annual service carried out by an Authorized
Spearhead Dealer or a Spearhead Service Engineer within 1 month of the
first anniversary of the date of sale and the Service Report form must have
been completed and stamped by the servicing dealer or Spearhead Service
Engineer and sent to Spearhead within 14 days after the first annual service.
3. The extended warranty does not cover costs of transportation of the
machinery to or from the dealer or Spearhead or the call out costs or traveling
expenses of on-site visits
Transfer of Warranty
Transfer of Warranty
Transfer of Warranty
Transfer of Warranty
The Spearhead warranty may be transferred to a subsequent owner of the machinery
(for use within the UK) for the balance of the warranty period subject to all of the
warranty conditions and provided that the Change of Owner form is completed and
sent to Spearhead within 14 days of change of ownership.
Spearhead reserves the right to make alterations and improvements to any
machinery without notification and without obligation to do so.