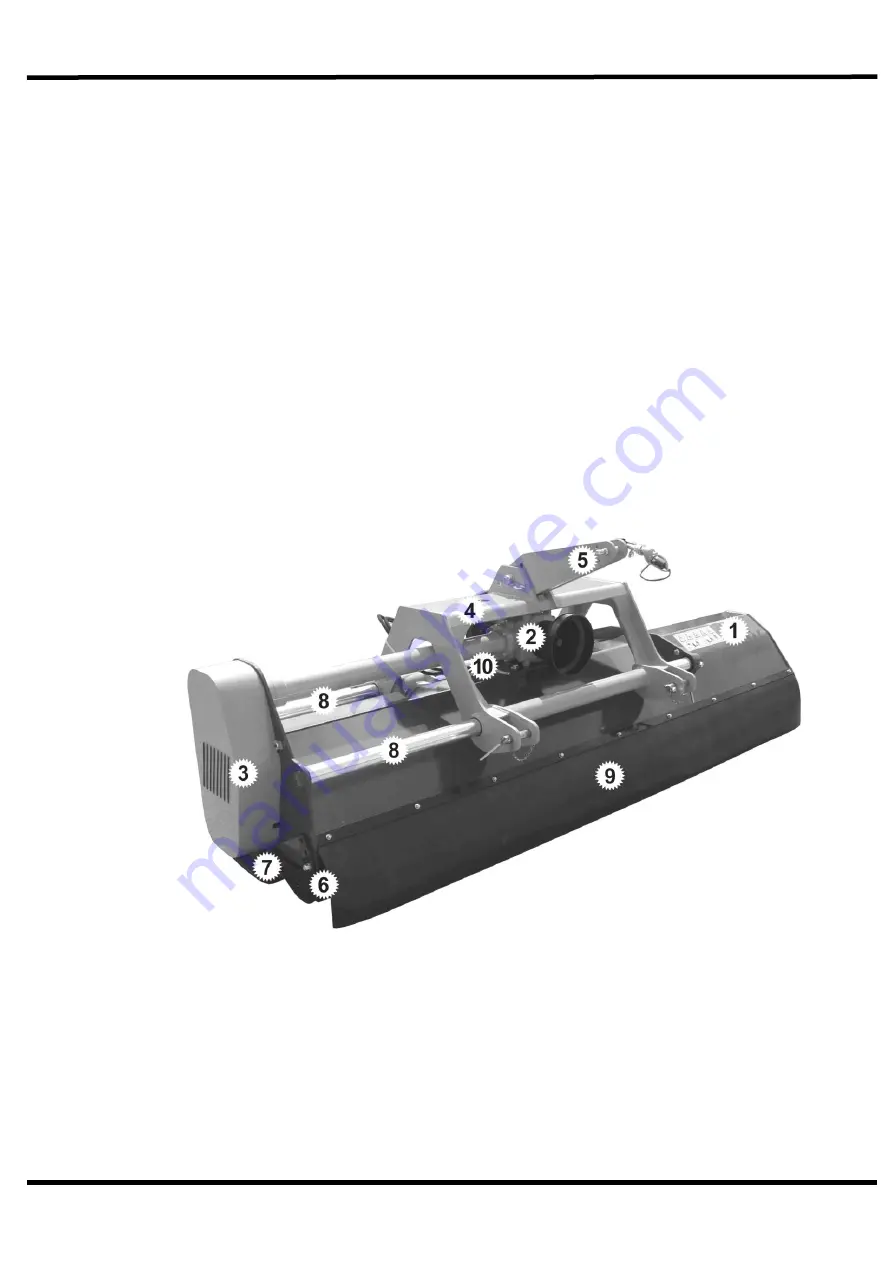
RHD Series RHD
230/250/280
9
1.
Main Frame
2. Gearbox
3. Belt Drive / Belt Guard
4. 3-Point Linkage
5. Upper Linkage
6. Rear Roller
7. Skid
8. Sliding Tubes
9. Rubber Guard
10. Hydraulic Ram
Machine Identification
Each machine is fitted with an identification plate with the following
information:
1. Machine (Part Number)
2. Machine Serial No.
3. Machine Weight
When ordering spares or replacement parts from your local dealer it is
important to quote both Part Number and Serial Number as stated on the
identification plate so the machine and model can be quickly and correctly
identified.
Technical Data
Component Identification