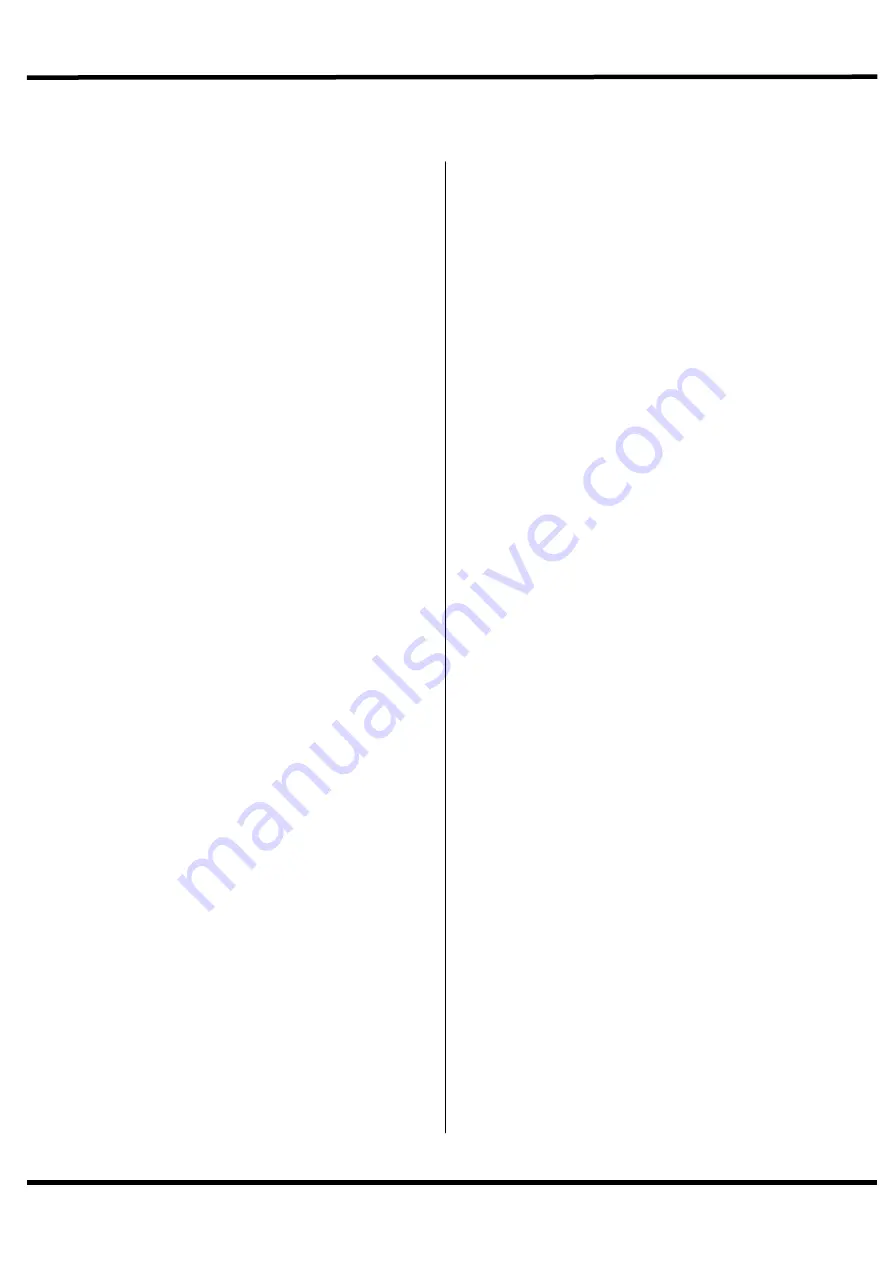
Spearhead
Multicut
460
23
Trouble Shooting Guide
Broken or damaged blades
1.
Raise cutting height to avoid
striking the ground
2.
Remove or avoid obstacles
such as rocks
3.
Check rotor speed
4.
Ensure a steady feed into drive
(Do not snatch the PTO)
5.
Fit optional stump jumpers
Damaged blade holder
1.
As above
2.
Failure to keep tight centre
retaining nut
Damage gearboxes
1.
Seized slip clutch.
2.
Telescopic shafts bottoming out
3.
Engaging drive with too much
power / revs
4.
Lack of grease on sliding tubes
of drive shaft
Damage to PTO shaft
1.
Seized slip clutch
2.
Telescopic tube bottoming out
3.
Engaging drive with too much
power / revs
4.
Turning too sharp
5.
Not enough overlap
6.
Lack of grease
7.
Build up of Debris under drive
shaft
Gearbox overheating
1.
Incorrect oil level
2.
Incorrect grade of oil
3.
Incorrect operating speed
4.
Machine overloaded
5.
Rubbish around the gearbox
reducing air circulation
Slip clutches overheating
1.
Machine overloaded
2.
Incorrect operating speed
3.
Incorrect setting
4.
Blades hitting the ground
Oil leak from gearbox
1.
Damaged shaft seal check for
foreign matter (wire-string)
2.
Faulty breather
3.
Damaged gasket
4.
Incorrect oil level
Metal fatigue on frame
1.
Too fast a traveling / operating
speed for conditions
2.
Wings not floating i.e. following
the ground contours (check tractor spool)
3.
Used in a manner or condition
contra to its intended purpose
Excessive skid wear
1.
Set skids above the ground