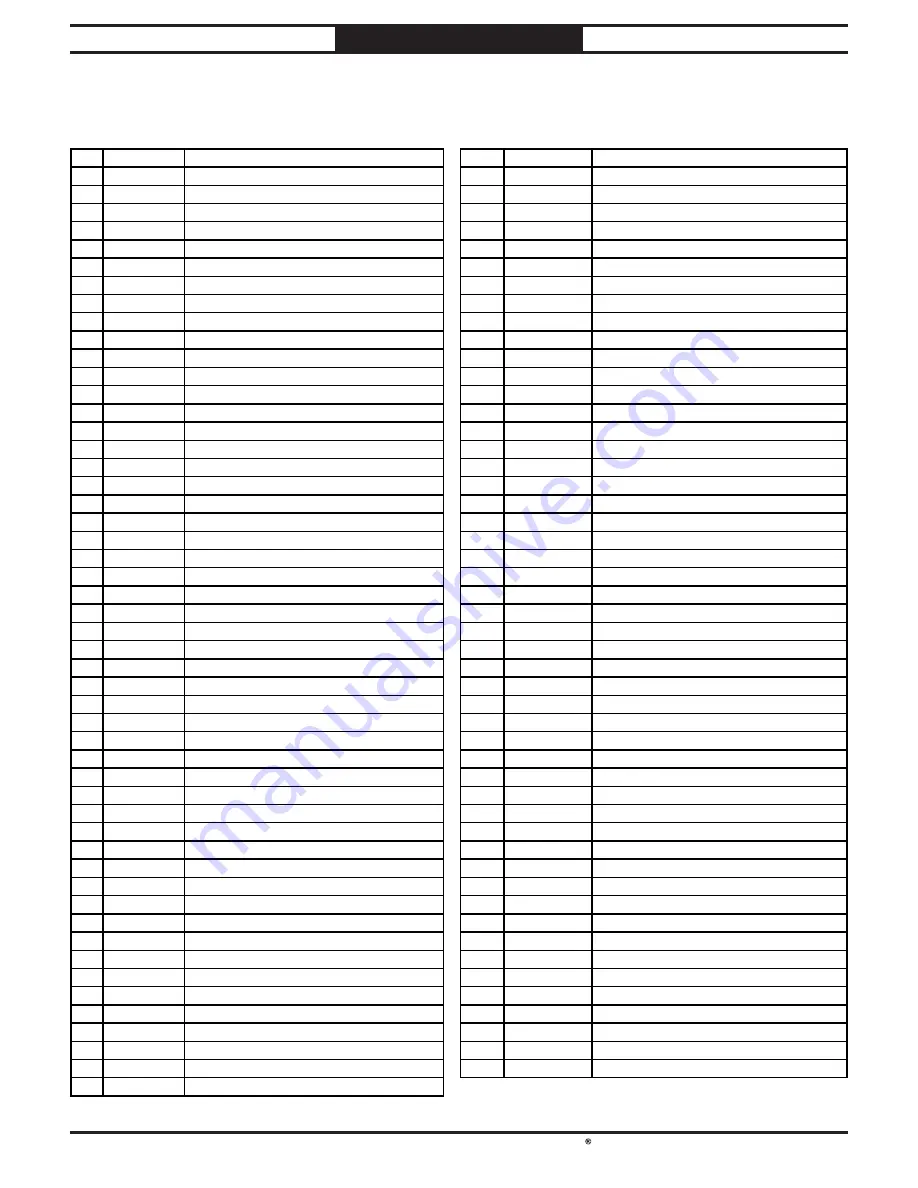
-70-
For Machines Mfd. Since 3/21
South Bend Tools
Model SB1119/SB1120
P A R T S
Motor & Handwheel Parts List (Cont.)
REF PART #
DESCRIPTION
REF
PART #
DESCRIPTION
52
PSB1119052 EXT TOOTH WASHER 25MM
111
PSB1119111
CAP SCREW M10-1.5 X 40
53
PSB1119053 BEARING RETAINING NUT M25-1.5
112
PSB1119112
ROLL PIN 4 X 20
54
PSB1119054 TAP SCREW M3 X 6
113
PSB1119113
COMPRESSION SPRING 1 X 12 X 38
55
PSB1119055 DUST COVER
114
PSB1119114
FIXED HANDLE 25 X 90
56
PSB1119056 SENSOR BOX
115
PSB1119115
LOCK NUT M20-1.5
57
PSB1119057
MAGNETIC HEAD
116
PSB1119116
FLAT WASHER 20MM
58
PSB1119058 TAP SCREW M2 X 6
117
PSB1119117
MOTOR BRACKET
60
PSB1119060 GROMMET 12.3 X 18 X 10.4MM
118
PSB1119118
MOTOR BRACKET PIVOT SHAFT
62
PSB1119062 DRAWBAR 5/8-11 X 10-5/16
119
PSB1119119
HOSE CLAMP 3"
68
PSB1119068 HEX NUT M20-1.5
120
PSB1119120
DUST CHUTE 3" X 11-3/4"
69
PSB1119069 STANDOFF-HEX MF M20-1.5 X 44, M12-1.75
121
PSB1119121
TENSION PIVOT SHAFT
70
PSB1119070
FLAT WASHER 12MM
122
PSB1119122
POLY V-BELT 10V X 25L RIBBED
71
PSB1119071
LOCK WASHER 12MM
123
PSB1119123
MOTOR 3HP 230V 3-PH (SB1119)
72
PSB1119072
CAP SCREW M12-1.75 X 80
123-1
PSB1119123-1
MOTOR JUNCTION BOX (SB1119)
73
PSB1119073
BUSHING
123-2 PSB1119123-2 MOTOR FAN COVER (SB1119)
74
PSB1119074
GAS STRUT BRACKET
123-3 PSB1119123-3 MOTOR FAN (SB1119)
75
PSB1119075
ELEVATION HOUSING
123-4 PSB1119123-4 BALL BEARING 6206-2NSE (FRONT) (SB1119)
76
PSB1119076 SET SCREW M5-.8 X 5
123-5 PSB1119123-5 BALL BEARING 6204-2NSE (REAR) (SB1119)
77
PSB1119077
BEVEL GEAR
123
PSB1120123
MOTOR 5HP 230V 3-PH (SB1120)
78
PSB1119078
FLAT WASHER 19.1 X 25.4 X 1.6MM
123-1
PSB1120123-1 MOTOR JUNCTION BOX (SB1120)
79
PSB1119079
KEY 5 X 5 X 12 RE
123-2 PSB1120123-2 MOTOR FAN COVER (SB1120)
80
PSB1119080 WOODRUFF KEY 5 X 20
123-3 PSB1120123-3 MOTOR FAN (SB1120)
81
PSB1119081
HANDWHEEL SHAFT
123-4 PSB1120123-4 BALL BEARING 6206-2NSE (FRONT) (SB1120)
82
PSB1119082 SET SCREW 5/16-18 X 5/16
123-5 PSB1120123-5 BALL BEARING 6204-2NSE (REAR) (SB1120)
83
PSB1119083 COLLAR
124
PSB1119124
FENDER WASHER 10MM
84
PSB1119084 FLAT HD CAP SCR M6-1 X 12
125
PSB1119125
HEX BOLT M10-1.5 X 25
85
PSB1119085 HANDWHEEL TYPE-24 200D X 20B-N X M10-1.5
126
PSB1119126
HEX BOLT M10-1.5 X 55
86 PSB1119086 FOLDING HANDLE 30 X 90, M6-1 X 12
127
PSB1119127
HEX NUT M10-1.5
87
PSB1119087 KNOB BOLT M10-1.5 X 25, 8-LOBE, D60
128
PSB1119128
FIXED HANDLE 38 X 110, M10-1.5 X 15
88
PSB1119088 ELEVATION HOUSING PLATE
129
PSB1119129
TENSION BLOCK
89
PSB1119089 SENSOR MOUNTING BRACKET
130
PSB1119130
HEX BOLT M8-1.25 X 45
90
PSB1119090 CAP
131
PSB1119131
TENSION BRACKET
91
PSB1119091
SET SCREW M8-1.25 X 35
132
PSB1119132
LOCK NUT M8-1.25
92
PSB1119092 HEX NUT M8-1.25
133
PSB1119133
TENSION ASSEMBLY MOUNTING BRACKET
93
PSB1119093 CAP SCREW M10-1.5 X 20
134
PSB1119134
BUTTON HD CAP SCR M8-1.25 X 20
94
PSB1119094 LOCK NUT M10-1.25
173
PSB1119173
KEY 5 X 5 X 25 RE
95
PSB1119095 FENDER WASHER 10MM
174
PSB1119174
MOTOR PULLEY
96
PSB1119096 HEIGHT SENSOR PLATE
175
PSB1119175
FENDER WASHER 8MM
97
PSB1119097
SPACER 10.8 X 20 X 50
176
PSB1119176
CAP SCREW M8-1.25 X 20
98
PSB1119098 BEVEL GEAR
177
PSB1119177
WIRE NUT 10-22 AWG
99
PSB1119099 THRUST BEARING 51202
178
PSB1119178
STRAIN RELIEF TYPE-3 M25-1.5
100 PSB1119100
GASKET
179
PSB1119179
MOTOR CORD 14G 4W 35"
101
PSB1119101
BUSHING
180
PSB1119180
PHLP HD SCR M6-1 X 12
102 PSB1119102
ELEVATION LEADSCREW
181
PSB1119181
SET SCREW M6-1 X 8
103 PSB1119103
ELEVATION GIB
182
PSB1119182
FLAT WASHER 6MM
104 PSB1119104
GAS STRUT
183
PSB1119183
CAP SCREW M6-1 X 12
105 PSB1119105
DUST TRAY
184
PSB1119184
EXT RETAINING RING 20MM
106 PSB1119106
SPINDLE HOUSING
185
PSB1119185
BUTTON HD CAP SCR M5-.8 X 10
107 PSB1119107
LOCK WASHER 10MM
186
PSB1119186
CAP SCREW M8-1.25 X 30
108 PSB1119108
CAP SCREW M10-1.5 X 55
187
PSB1119187
LOCK WASHER 8MM
109 PSB1119109
SPINDLE LOCK SHAFT SEAT
188
PSB1119188
CAP SCREW M8-1.25 X 30
110
PSB1119110
SPINDLE LOCK SHAFT