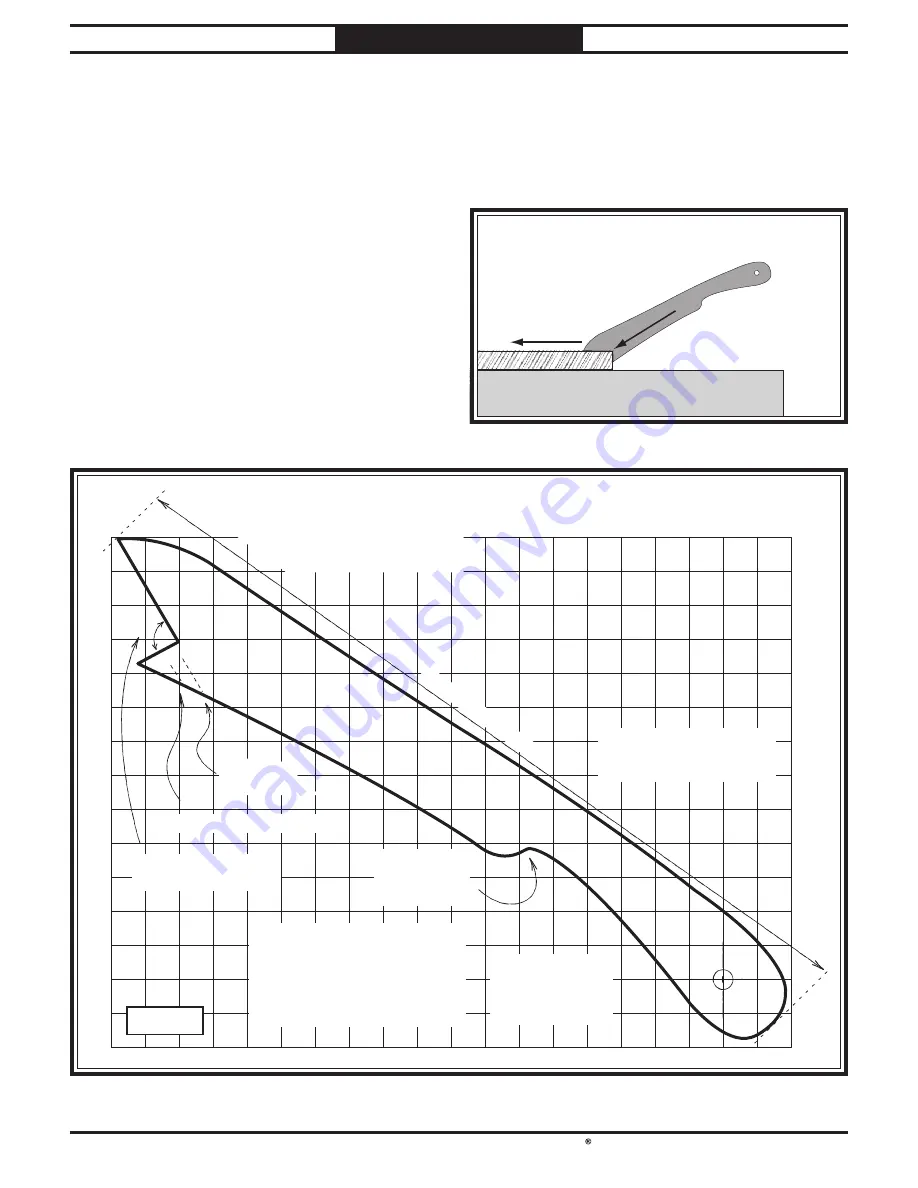
-42-
For Machines Mfd. Since 3/21
South Bend Tools
Model SB1119/SB1120
A C C E S S O R I E S
Making Push Sticks
When used correctly, push sticks reduce the
risk of injury by keeping hands away from the
cutter. In the event of an accident, a push stick
can absorb damage that would have otherwise
happened to hands or fingers. Use push sticks
whenever your hands will get within 12" of the
cutter. To maintain control when shaping large
workpieces, start by feeding with your hands
then use push sticks to finish the operation, so
your hands are not on the end of the workpiece
as it passes through the cutter.
Feeding: Place the notched end of the push stick
against the end of the workpiece (see Figure
65), and move the workpiece into the cutter with
steady downward and forward pressure.
Supporting: A second push stick can be used to
keep the workpiece firmly against the fence while
cutting. When using this method, only apply
pressure before the cutter; otherwise, pushing
the workpiece against or behind the cutter will
increase the risk of kickback.
Figure
Figure 64. Side view of push stick in use.
. Side view of push stick in use.
Figure
Figure 65. Template for a basic shop-made push stick (not shown at actual size).
. Template for a basic shop-made push stick (not shown at actual size).
90º
Cut here to
push
1
⁄
4
" stock
Cut here to push
1
⁄
2
" stock
Notch for placing on
corners of workpieces
15
3
/
4
" Minimum Length
MATERIAL: Only use hardwood,
sturdy plywood, or high-density
plastic. Do not use softwood
that may break under pressure
or metal that can break teeth
from the blade!
SANDING: Sand
edges to remove
rough edges and
increase comfort.
SIZING: Push stick must
be at least 15
3
⁄
4
" long.
Use
1
⁄
2
"–
3
⁄
4
" thick material.
Notch to help
prevent hand
from slipping
1
⁄
2
" Grid
Making a Push Stick
Use this template to make
your own push stick.