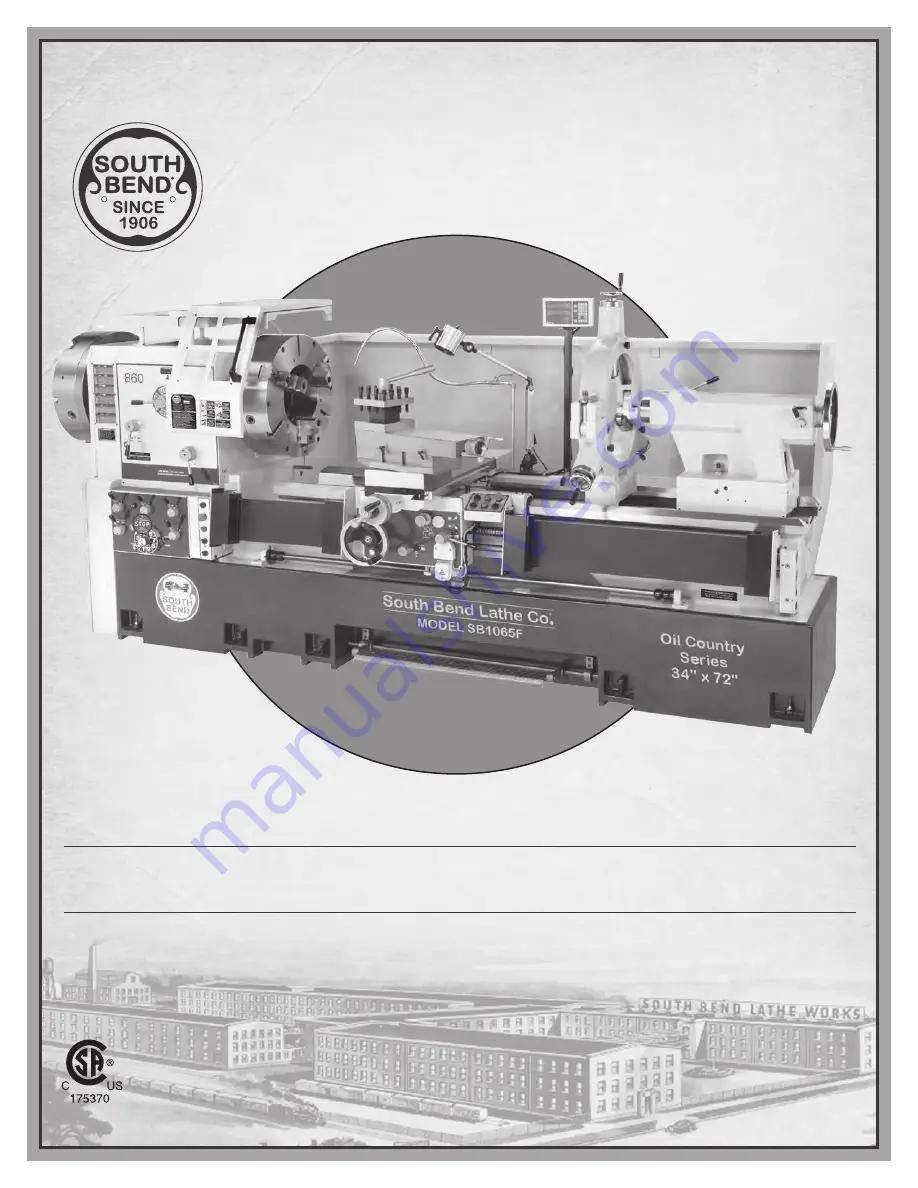
®
A Tradition of Excellence
South Bend Tools
©
December
, 2021 by South Bend Tools
For Machines Mfd. Since 07/19 (V1.12.21)
BIG BORE LATHE
MODEL SB1065F 34" X 72"
MODEL SB1069F 38" X 212"
MODEL SB1066F 34" X 132"
MODEL SB1070F 42" X 132"
MODEL SB1067F 34" X 212"
MODEL SB1071F 42" X 212"
MODEL SB1068F 38" X 132"
OWNER'S MANUAL
Model SB1065F
Shown with Optional
Accessories
Summary of Contents for Oil Country Series
Page 65: ...South Bend Tools...
Page 66: ......