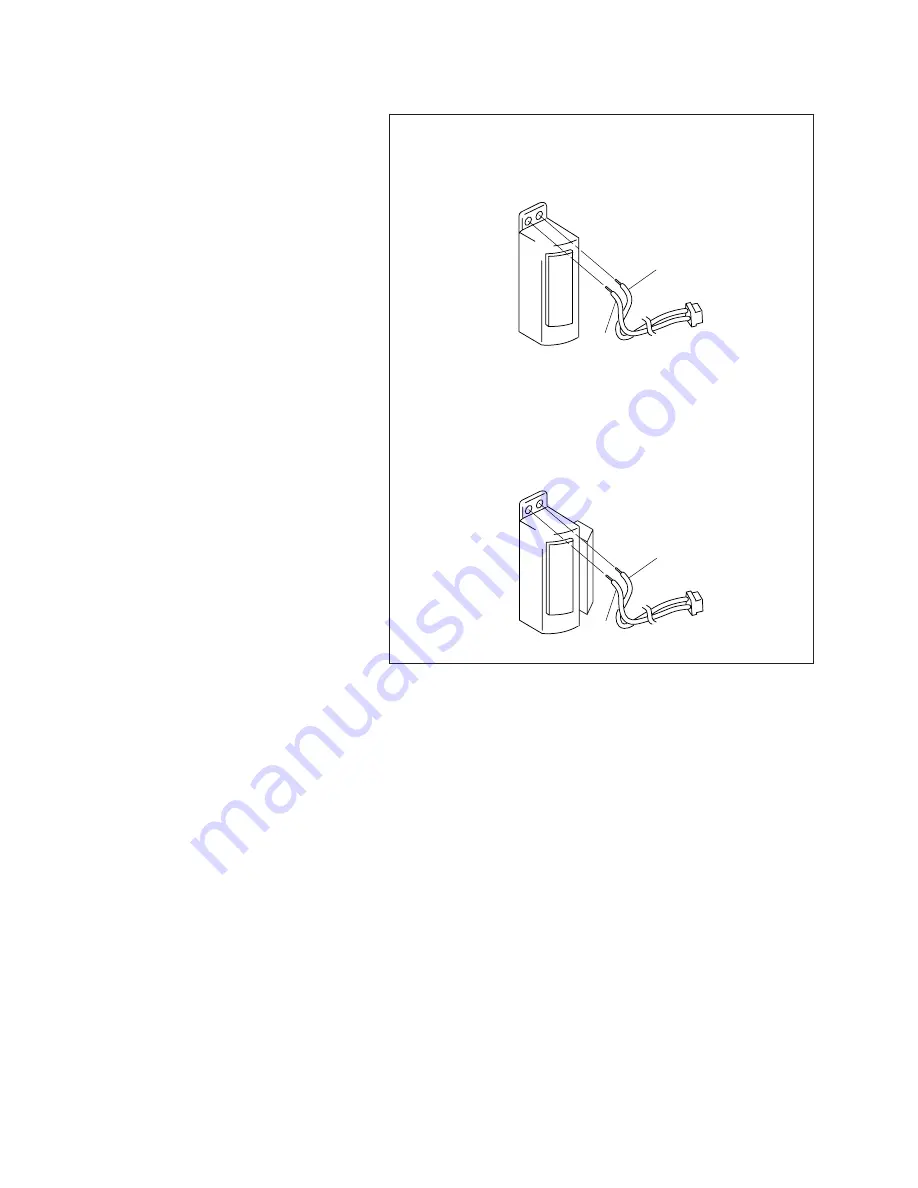
4-110
DVW-790WS/709WS/707 P2V1
DVW-790WSP/709WSP/707P P2V1
4-2. Parts Replacement
3. Harness Removal
Desolder and remove the harness.
4. Harness Soldering
Attach the harness removed at step 3 with solder to
the new FE head.
DVW-707:
10001 through 10055
DVW-707P:
40001 through 40190
DVW-709WS: 10001 through 10125
DVW-709WSP: 40001 through 40255
DVW-790WS: 10001 through 10160
DVW-790WSP: 40001 through 40510
BLK
GRY
BLK
GRY
DVW-707:
10056 and higher
DVW-707P:
40191 and higher
DVW-709WS: 10126 and higher
DVW-709WSP: 40256 and higher
DVW-790WS: 10161 and higher
DVW-790WSP: 40511 and higher