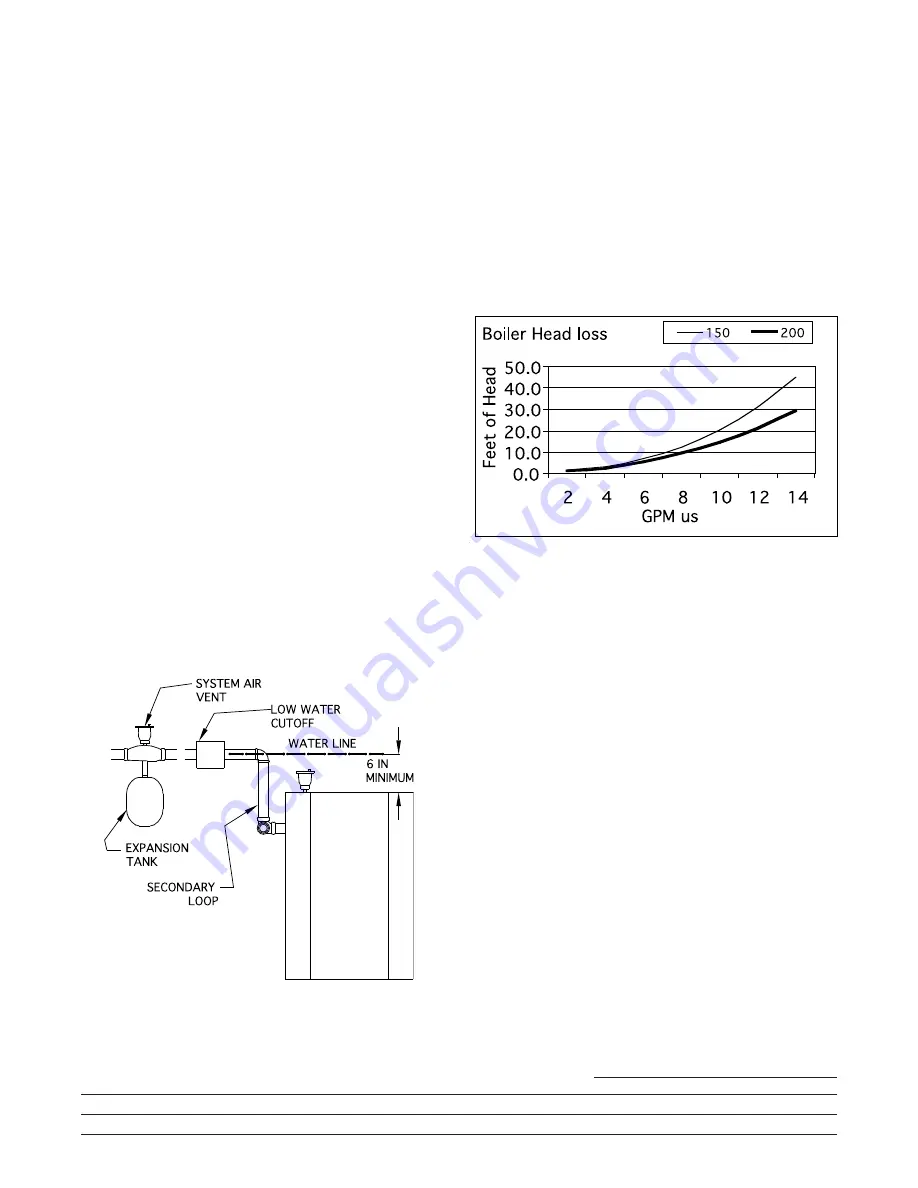
GT INSTALLATION AND OPERATION INSTRUCTIONS
Page 12
Hot water boilers are designed to operate with airless
water in the system. The GT boiler is provided with
a
1/8 in
,
3 mm
, air vent located on the top of the unit.
This air vent is intended to vent the boiler on initial
startup. This device will
NOT
continuously vent air
collecting in the primary loop and is not intended
to be the primary venting device. The air scoop as
shown in Figure 21 is the primary venting location. It is
recommended that an additional air scoop be used in
the secondary plumbing. If air continues to be a problem
an air scrubber must be used.
NOTE: Only inhibited propylene glycol solutions
should be used if freeze protection is required.
Avoid using mixtures greater than 30%, unless
the size of the boilers’ circulator(s) is increased
accordingly. Under no circumstances should a 50%
mixture be exceeded.
Low Water Cut Off, LWCO
If a LWCO is used ensure that the water line of the “Low
Water Cutoff” is at least
6 in
,
152 mm
, above the top of the
boiler, Figure 21. It is recommended that the LWCO be
situated so that it can be tested without removing water
from the boiler. Tri-cocks and a gauge glass are highly
recommended. Valves shall not be installed between
the LWCO and the boiler. Use an air vent if installed as
per our diagram to be used as a vacuum breaker and to
eliminate air upon fi lling.
Figure 21 - LWCO & Air Vent Piping
PRIMARY LOOP PLUMBING
This low mass boiler requires a continuous minimum
water fl ow for proper operation. The heat exchanger in
this boiler is more restrictive than a conventional boiler.
The system pump must be sized to overcome the head
loss of the boiler, Figure 22. Greater consideration must
be given to the capabilities of the circulating pump(s) in
the primary-loop. This includes the pump used for an
indirect tank.
Figure 22 - Boiler Head Loss
Table 3 lists the recommended circulators for use as the
primary and indirect loop pumps.
Figure 23 shows the proper way to plumb a primary loop
for single boiler installations.
MULTIPLE BOILER PRIMARY LOOP
Figure 24 shows the proper way to plumb a primary loop
for multiple boiler installations.
SECONDARY LOOP PLUMBING
Figures 25 and 26 show some typical primary/ secondary
piping systems. It is the responsibility of the installing
contractor to determine which system best meets the
need of the installation. Contractor modifi cations to these
instructions may be required, based upon the existing
piping and system design.
Table 3 - Recommended Primary and Indirect Loop Circulators
Minimum
Max. Temp.
Minimum Primary &
Restriction
Flow
Rise
Indirect Pump Size
Model
Head Loss
GPM
,
L/s
°F
,
°C
B&G Grundfos Taco
GT150
7 ft at 6 GPM
,
2.1 m at 0.4 L/s
6
,
0.4
45
,
25
NRF-33
UP 26-64
0010
GT200
10 ft at 8 GPM
,
3 m at 0.5 L/s
8
,
0.5
45
,
25
PL-36
UP 26-99
0011
Summary of Contents for GT-150
Page 19: ...GT INSTALLATION AND OPERATION INSTRUCTIONS Page 19 Figure 30 Multiple 4 Wire Zone Valves...
Page 22: ...GT INSTALLATION AND OPERATION INSTRUCTIONS Page 22 Figure 33 Boiler Ladder Diagram...
Page 23: ...GT INSTALLATION AND OPERATION INSTRUCTIONS Page 23 Figure 34 Boiler Connection Diagram...
Page 40: ...WESTCAST INC 260 NORTH ELM STREET WESTFIELD MA 01085 TEL 413 562 9631 FAX 413 562 3799...