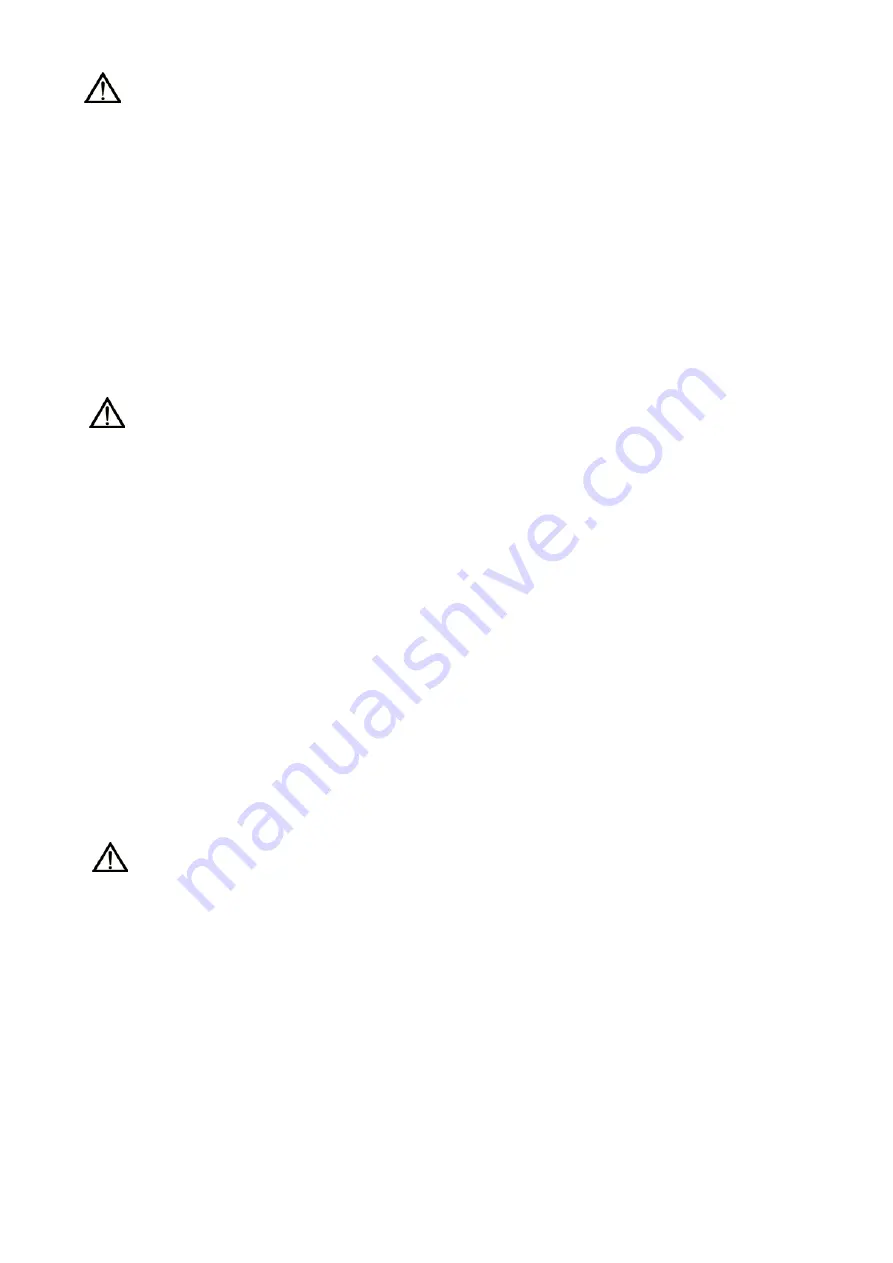
- 8 -
Caution
(1) Do not allow pallets to collide while the lever is standing erect.
If the next pallet collides while the lever is standing erect (after kinetic energy has been absorbed by the
shock absorber), all the energy will be applied to the cylinder body.
(2) When a load directly connected to the cylinder is stopped at an intermediate position
Apply the operating range in the model selection (P.5) only in these cases where the stopper cylinder is
used to stop pallets on a conveyor belt. When using the stopper cylinder to stop loads directly connected
to a cylinder or some other equipment, a lateral load is applied as the cylinder thrust. Please consult SMC
in such cases.
3.
Installation
3-1. Operating air
For compressed air supplied to the cylinder, use air filtered by SMC’s filter such as AF series
and adjusted to specified setting pressure by SMC’s regulator such as AR series.
Warning
(1) Type of fluids
Please consult with SMC when using the product with fluids other than compressed air.
(2) When there is a large amount of condensate.
Compressed air containing a large amount of condensate can cause malfunction of pneumatic
equipment. An air dryer or water separator should be installed upstream from the filter.
(3) Drain flushing
If condensation in the drain bowl is not emptied on a regular basis, the bowl will overflow and allow
the condensation to enter the compressed air lines. This may cause malfunction of pneumatic equipment.
If the drain bowl is difficult to check and remove, installation of a drain bowl with an auto drain option
is recommended.
(4) Use clean air.
Do not use compressed air that contains chemicals, synthetic oils including organic solvents, salt or
corrosive gases, etc., as it can cause damage or malfunction.
(5) Lubricating the non-lube type cylinder
SMC products have been lubricated for life at manufacture, and do not require lubrication in service.
If a lubricant is used in the system, use turbine oil Class 1 (no additive), ISO VG32. Once lubricant is used
in the system, lubrication must be continued because the original lubricant applied during manufacturing
will be washed away.
Caution
(1) Install air filters.
Install air filters at the upstream of the valves. Ensure that the air supply system is filtered to 5 microns.
(2) Take measures to ensure air quality, such as by installing an aftercooler, air dryer,
or water separator.
Compressed air that contains a large amount of drainage can cause malfunction of pneumatic
equipment such as valves. Therefore, take appropriate measures to ensure air quality, such as
by providing an aftercooler, air dryer, or water separator.
(3) Use the product within the specified range of fluid and ambient temperature.
Take measures to prevent freezing, since moisture in circuits will be frozen under 5
℃
, and this may
cause damage to seals and lead to malfunction.
Summary of Contents for RS2H Series
Page 24: ...23...