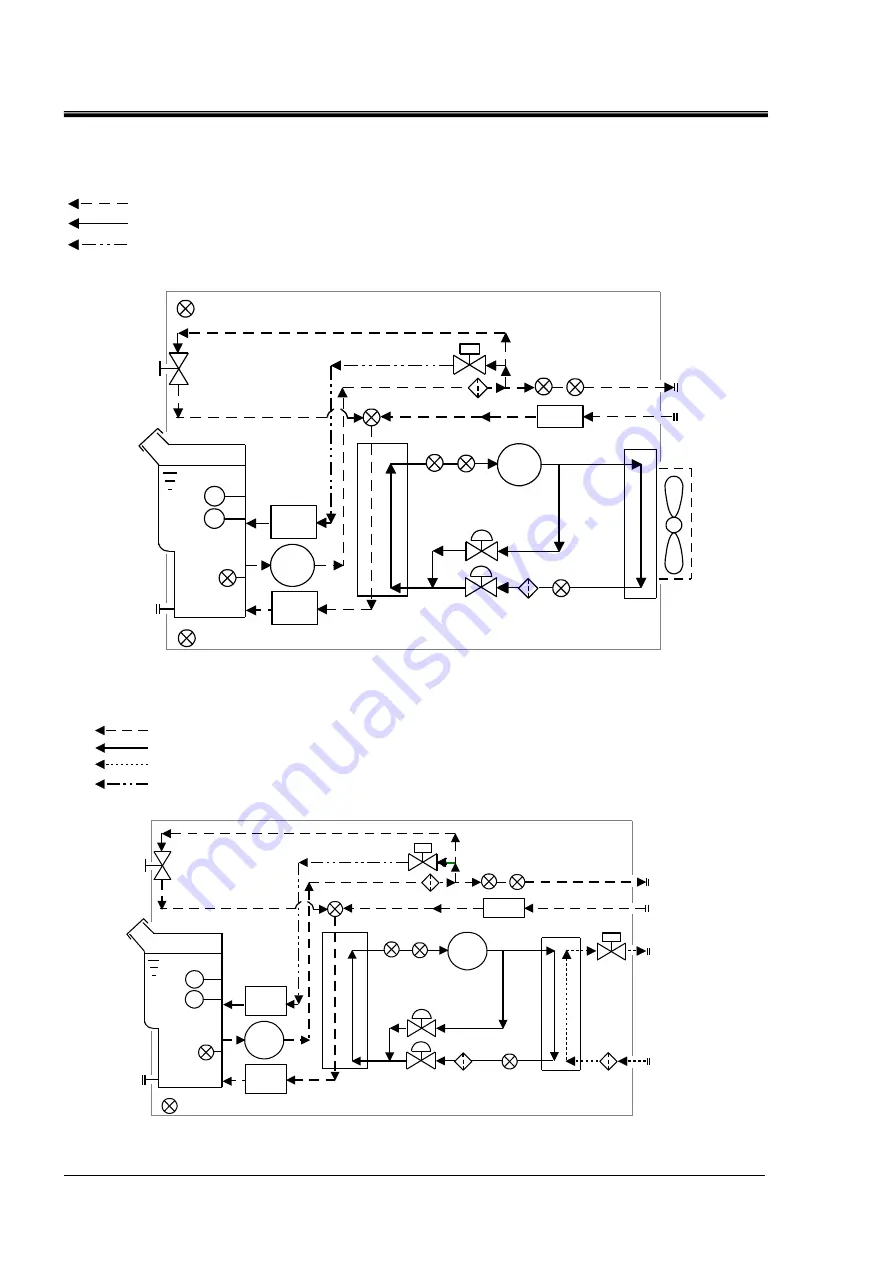
HRX-OM-W002-A
Chapter 9
Documents
9.3
Flow Chart
HRR Series
9-10
9.3 Flow Chart
9.3.1
HRR
‐
A
‐
20
‐
Fig.
9-5 Flow Chart(HRR
-A
-20-
)
9.3.2
HRR
‐
W
‐
20
‐
Fig. 9-6 Flow Chart (HRR
-W
-20-
)
Comp
Expansion 1
Temp.
sensor
Expansion 2
Press.
sensor
Heat exchanger
Flow
sensor
Tank
Level switch
Pump
DI
filter
Temp. sensor
Temp.
sensor
Press.
sensor
Solenoid valve for option-D
Press.
sensor
Circulating fluid
return port
Bypass valve
Particle
filter
Strainer for outlet
Electrical
conductivity
sensor
for option-D
Drain
Strainer
Water leakage sensor
Circulating fluid
outlet
Option - D
Temp.sensor
Circulating fluid circuit
Refrigerant circuit
Electric conductivity circuit
(For option -D 【Electric conductivity control】
Comp
Expansion 1
Temp.
sensor
Expansion 2
Press.
sensor
Heat exchanger
Flow
sensor
Tank
Level switch
Pump
DI
filter
Temp. sensor
Temp.
sensor
Press.
sensor
Solenoid valve for option-D
Press.
sensor
Circulating fluid
return port
Bypass valve
Particle
filter
Strainer for outlet
Electrical
conductivity
sensor
for option-D
Drain
Strainer
Water leakage sensor
Y - Strainer
Heat exchanger
Circulating fluid
outlet
Facility water outlet
Facility water inlet
Option - D
Circulating fluid circuit
Refrigerant circuit
Facility water circuit
Electric conductivity circuit
(For option -D 【Electric conductivity control】