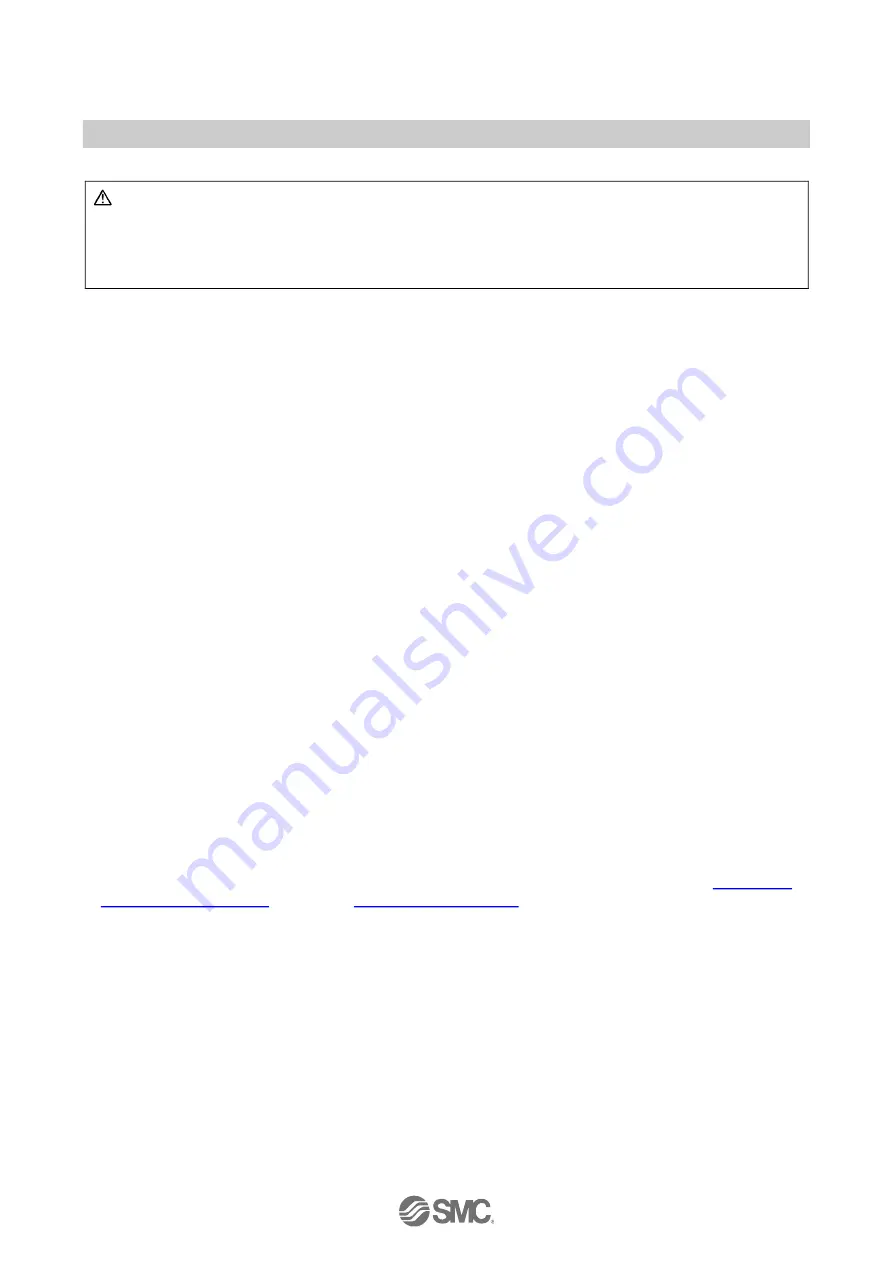
- 11 -
No.EX
※※
-OMU1006-B
1.2. Electrical safety
WARNING: Loss of safety function/hazardous shock currents
Incorrect installation can result in the loss of the safety function as well as hazardous shock currents.
Observe the notes on electrical safety.
Plan the products used and their installation in the system according to the specific requirements.
Recheck plants and systems retrofitted with PROFIsafe.
1.2.1. Direct/indirect contact
Protection against direct and indirect contact according to EN61010-2-201 must be ensured for all
components connected to the system. In the event of an error, hazardous voltages must not occur
(single-fault tolerance).
Measures required:
Using power supply units with safe isolation (SELV or PELV).
Decoupling circuits, for any connConfiguration is defective, or initial commissioning has ection to circuits
which are not SELV or PELV circuits using phoptocouplers, relays, and other components which meet
the requirements of safe isolation.
1.2.2. Power supply units for 24 V supply
Only use power supply units that are SELV or PELV according to EN 61010-2-201
Under and over voltage detection is included in this product. Outside of the nominal range 19 to 33 VDC will
result in error conditions.
The power supply unit must have a minimum current capability of 5 A.
1.2.3. Insulation rating
When selecting the equipment, please take into consideration the transient and surge voltages, which may
occur during operation.
The SI Unit is designed for use with connecting cables that are less than 30 m long and do not go outside of
a building. If these requirements are not met, then external measures must be taken to protect the unit.
(reference immunity requirements of EN 61131-2)
1.3. Safety of the machine or system
The machine/system manufacturer and the operator are responsible for the safety of the machine or system
and the application in which the machine or system is used.
1.3.1. Draw up and implement a safety concept
In order to use the SI Unit, a safety concept is required for your machine or system. This includes a hazard
and risk analysis as well as a test report (checklist) for validating the safety function: refer to
Section 1.4
"Directive and standards"
and refer to
"Appendix C: Checklists"
.
The target safety integrity level (SIL according to IEC 61508, SILCL according to EN 62061 or performance
level and category according to EN ISO 13849-1) is ascertained on the basis of the risk analysis. The safety
integrity level ascertained determines how to connect and parameterize the SI Unit within the safety
function.
1.3.2. Validate hardware and parameterization
Carry out a validation every time you make a safety-related modification to your overall system.
Use your test report to ensure that:
The safe products are connected to the correct actuators.
The variables have been linked to the safe actuators correctly.
2020-10-30 10:03
DL085648