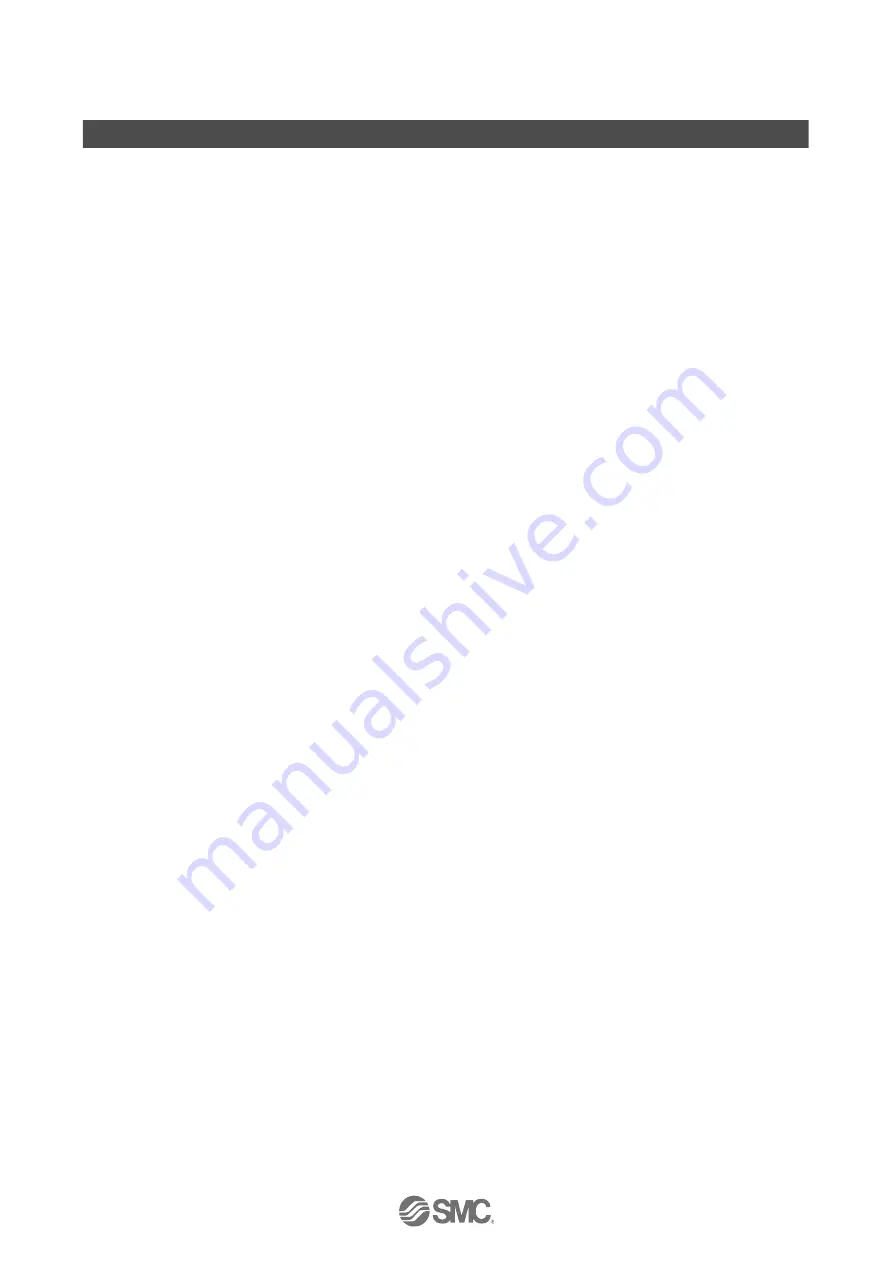
- 13 -
No.EX
※※
-OMU1006-B
2. Product Summary
2.1. Features
SI Unit
The SI (Serial Interface) Unit represents a PROFIsafe on PROFINET IO-device for SMC pneumatic valves. It
can be used to implement a safety function for the directly connected valves and has the following properties:
Designed for use in safety systems up to SIL 3 according to EN 61508.
Designed for use in safety systems up to SIL CL3 according to EN 62061.
Designed for use in safety systems up to Category 3, Performance level (PL) e according to EN ISO
13849.
One safe power supply switch for solenoid valves.
IP67 protection.
Two M12 connectors (4-pin socket, D-coded) for PROFINET IO connection and one M12 connector (4-pin
plug, A-coded) for power supply.
Up to 32 solenoid valves outputs.
Integrated diagnostic and protection function.
Galvanically isolated power supplies.
Factory Reset function supported.
After a factory reset, the unit needs to be powered off and on again.
Corresponding solenoid valve manifolds
SY series SY3000, SY5000, SY7000
JSY series JSY1000, JSY3000, JSY5000
2020-10-30 10:03
DL085648