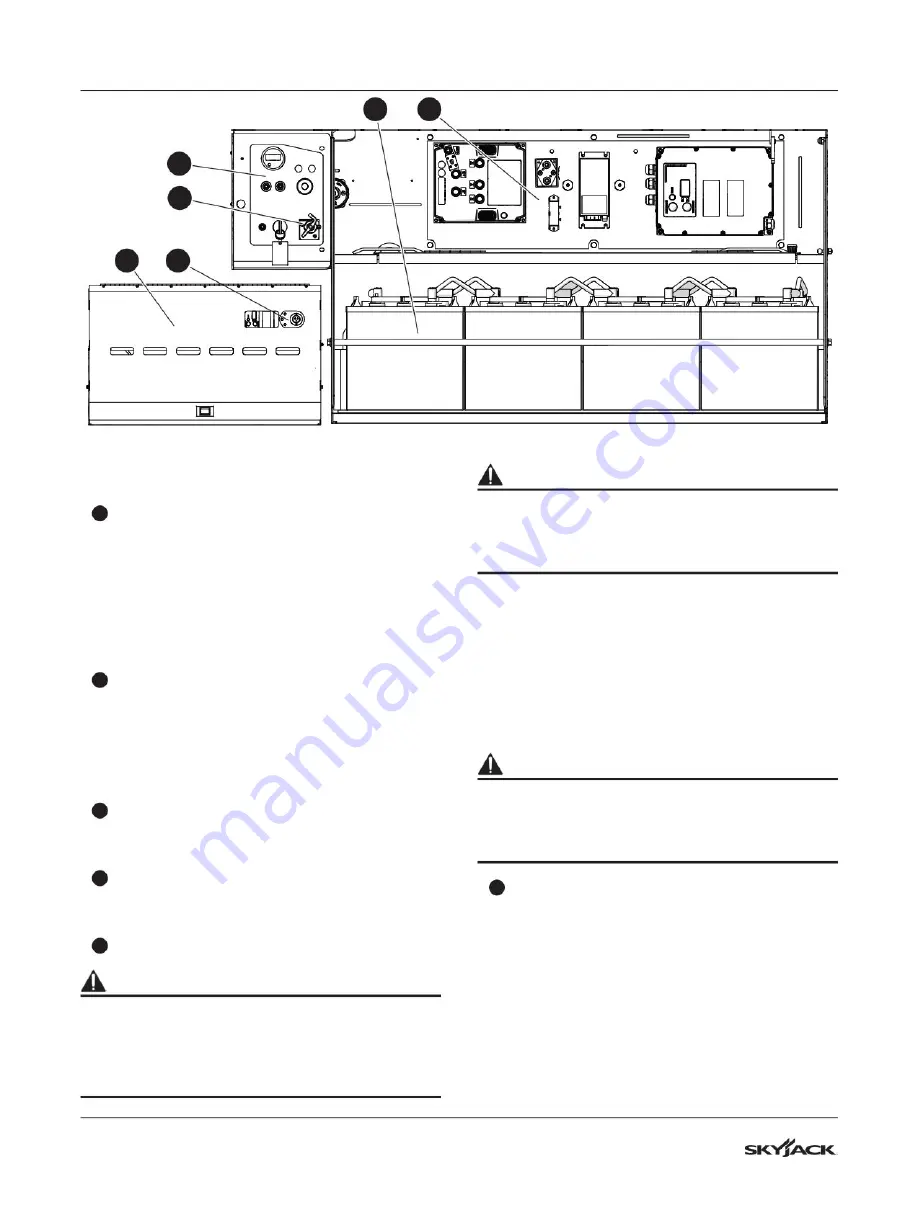
36
SJ6832 RTE
221844ACAI
Section 4 – Inspections Before Operation
Visual and daily maintenance inspections
4.2-6 Electrical compartment
Do the inspection that follows:
1
Electrical compartment cover
▪
Make sure that the access door is latched
tightly and in good condition.
▪
Make sure that the hinges and lockable latch
on the access door are latched tightly and in
good condition.
▪
Make sure that the hinges have sufficient
lubrication.
2
Main power disconnect switch
▪
Turn the
main power disconnect
switch to the
off position.
▪
Make sure the switch rotates and stays in the
on and off position.
▪
Make sure the cables are not loose.
3
Base controls
▪
Make sure there is no visible damage, and all
the switches are in their off/neutral positions.
4
AC power socket
▪
Make sure the that the socket is free of dirt or
blockages.
5
Batteries
WARNING
Explosion hazard. Keep flames and sparks away.
Do not smoke near the batteries. Batteries release
explosive gas while you charge them. Charge the
batteries in a well-ventilated area. If you do not
obey, there is a risk of death or serious injury.
WARNING
Corrosion hazard. Do not touch battery acid. Wear
the correct PPE. If the battery acid touches you,
immediately flush the area with cold water and get
medical aid.
1.
Do an inspection of the battery cases for
damage.
2.
Make sure all the battery connections are
tight.
3.
If applicable, check the battery fluid levels. If
the plates do not have a minimum 13 mm
of solution above them, add distilled or
demineralized water.
WARNING
Only use original or manufacturer-approved parts
and components for the MEWP. If you do not obey,
there is a risk of death, serious injury, or machine
damage.
6
Motor controller panel
▪
Make sure the panel is correctly installed, and
in good condition.
▪
Make sure there is no visible damage.
▪
Make sure all electrical connections are tight.
4
2
3
1
5
6
Summary of Contents for SJ6832 RTE Series
Page 1: ...221844ACAI August 2021 CE OPERATION MANUAL ROUGH TERRAIN SCISSORS SJ6832 RTE...
Page 4: ...4 SJ6832 RTE 221844ACAI Notes...
Page 14: ...14 SJ6832 RTE 221844ACAI Notes...
Page 20: ...20 SJ6832 RTE 221844ACAI Notes...
Page 52: ...52 SJ6832 RTE 221844ACAI Notes...
Page 60: ...60 SJ6832 RTE 221844ACAI Notes...
Page 76: ...76 SJ6832 RTE 221844ACAI Notes...
Page 108: ...108 SJ6832 RTE 221844ACAI Notes...
Page 110: ...110 SJ6832 RTE 221844ACAI Notes...
Page 111: ......
Page 112: ...www skyjack com...