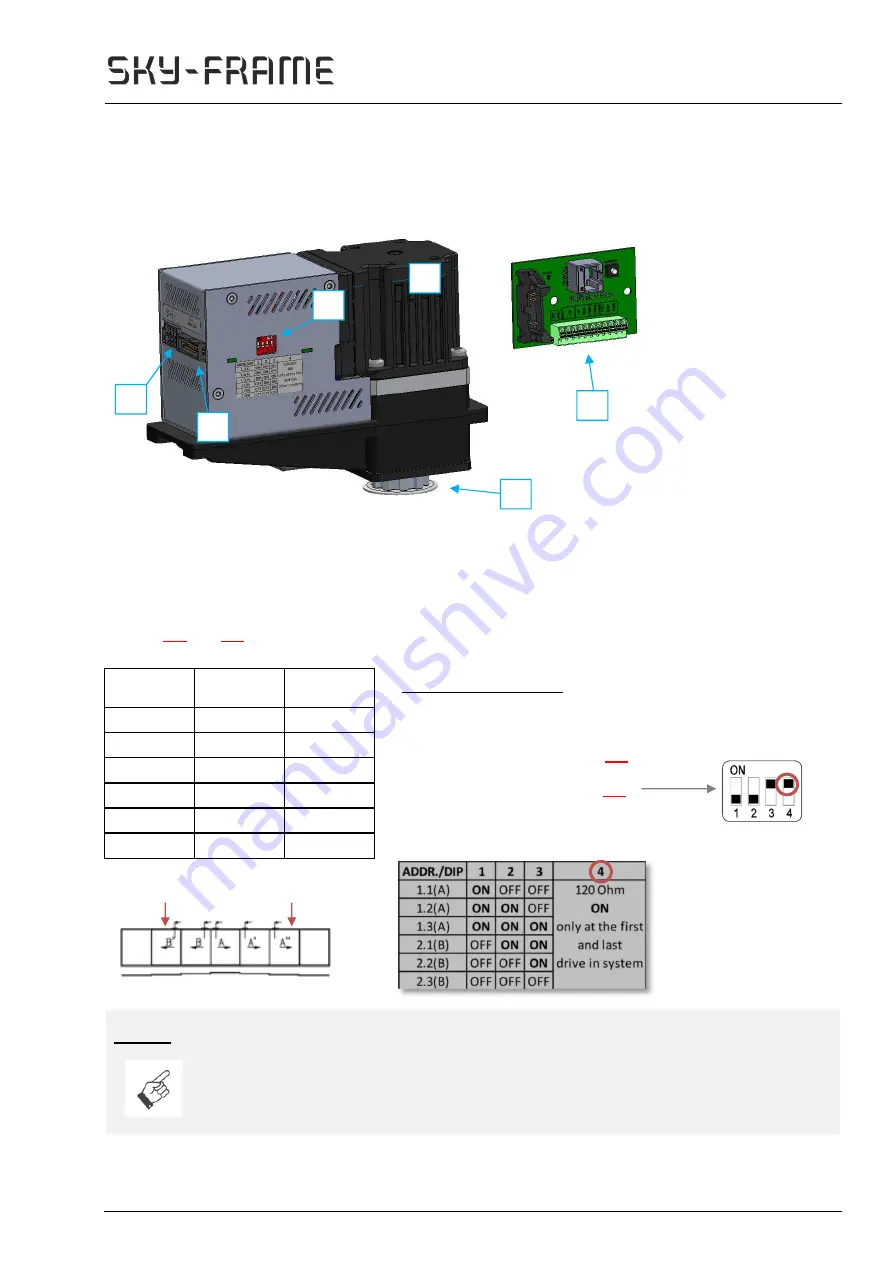
www.sky-frame.com
07.12.2016
13.4.1.18
3.4
Sky-Frame Operator description
The following components can be found in the Sky-Frame Operator:
[1] button interface
[2] servo motor
[3] DIP switch
[4] CAN bus connection
[5] connection for
button interface
[6] drive pinion with
flanged disk
The button interface (see 8.5) for connecting the control button (see 8.3) is only in the connection service
opening of the SFO-M (Master) that opens first ( A ).
3.5
Addressing
The addresses of the drives are set using the DIP switch on the outside of the drive housing.
With the
first
and
last
drive in the system, the terminating resistor must be switched in (DIP 4).
Example of 3+2 system:
Drive 1.1: ON / OFF / OFF / OFF
Drive 1.2: ON / ON / OFF / OFF
Drive
1.3
:
ON / ON / ON /
ON
Drive 2.1: OFF / ON / ON / OFF
Drive
2.2
:
OFF / OFF / ON /
ON
DIP switch settings:
Drive:
first last
2.2
2.1 1.1 1.2
1.3
NOTICE
The drives are already correctly addressed for the relevant system in the factory.
Element
Address
CAN
adress
A
1.1
11
A’
1.2
12
A’’
1.3
13
B
2.1
21
B’
2.2
22
B’’
2.3
23
1
2
3
4
5
6