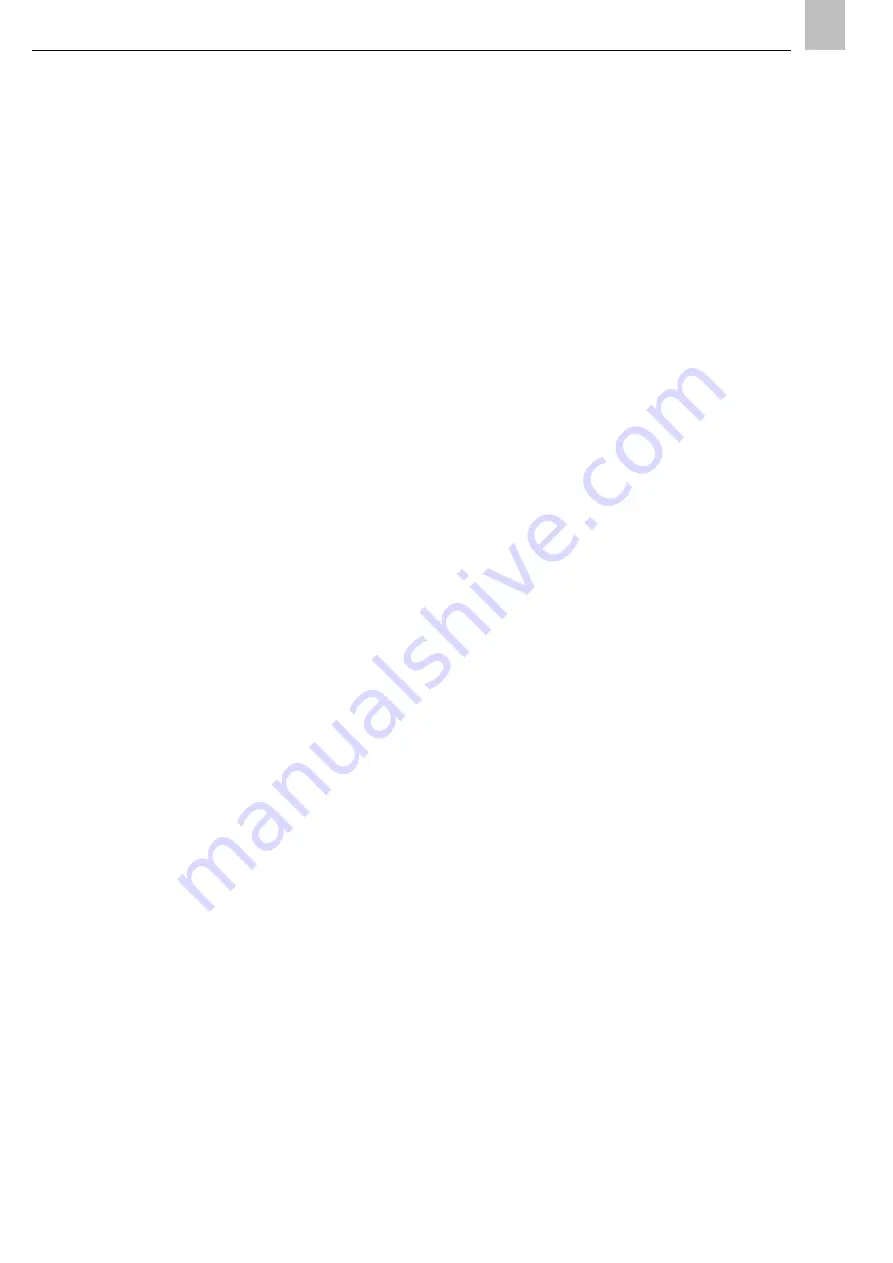
Adjusting the parameters
Page 17
EN
10.1
General
The optimum adjustment of the MQL system
L
UBRI
L
EAN
®
Vario depends on several factors
such as the applicable primary pressure, length
of the aerosol transport lines, type and size of
the tool, cross-section of the cooling channel as
well as the processing procedure. For this
reason it is not possible here to specify absolute
adjustment parameters for the particular
processing situations.
The adjustment parameters illustrated in Fig. 6
are approximate values and should provide you
with an initial orientation for adjusting the MQL
system L
UBRI
L
EAN
®
Vario for your particular
application.
We recommend that you determine and
optimise the necessary adjustment values for
your particular application by performing test
runs so that you can achieve the best results for
your processing procedure.
If the machine has been idle for extended
periods or a tool has been replaced, this can
result in temporary discontinuities in the aerosol
supply to the lubrication point and the
generation of oil mist. The supply of lubricant
will re-stabilise during operation and possible oil
mist that has been generated will disappear.
10.2
Effect of primary pressure
The MQL system L
UBRI
L
EAN
®
Vario obtains the
energy necessary for generating aerosol from
the compressed air supplied to the system.
The system is functional at least 6 bar of primary
pressure and able to generate an aerosol
suitable for most lubricating tasks.
The full output of the system is, however, only
possible with a primary pressure of 8 bar.
10.3
Procedure for adjusting
parameters
The following indications should help you
determine the correct adjustments for the MQL
system and your particular application.
1.
Put the MQL system L
UBRI
L
EAN
®
Vario into
operation by opening the main air valve.
2.
Set the air valve to 6 bar and the lubricant
flow rate to 100 %. With the spindle idle,
check whether the aerosol is able to flow
unimpeded through the channel system of
the machine tool. This is easiest to
recognise if the tool from the tool-receiving
socket is removed. The aerosol must
visibly discharge from the channel system.
3.
Put the tool back into the tool-receiving
socket and hold an oil-free component
surface approximately 1 - 3 mm below the
tool on the discharge channel. If no
lubricant film collects on the component
surface, there is a malfunction in the
channel system of the tool. Check the tool
and tool-receiving socket.
4.
To determine the amount of lubricant that
has been transported in the case of a
rotating tool, spread a smooth and oil free
panel on the machine table. Next, move
the rotating tool until it is approximately
1 - 3 mm above the panel.
10 Adjusting the parameters
Summary of Contents for LUBRILEAN Vario
Page 2: ......
Page 26: ...Technical Data Page 26 EN...
Page 27: ...Notes EN...
Page 28: ...Notes EN...
Page 29: ...Notes EN...
Page 30: ...Notes EN...
Page 31: ......