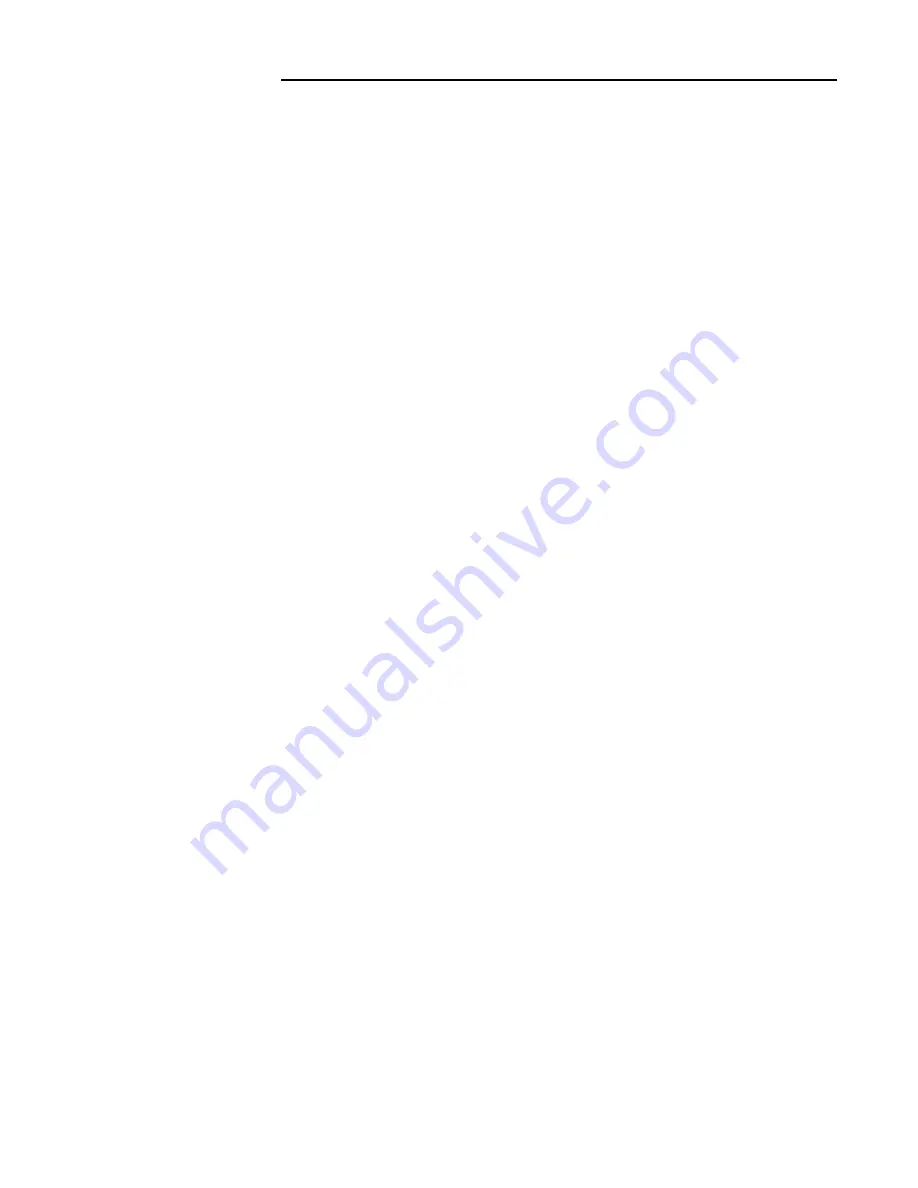
1 General Information
Repair Information
1 - 10
GENERAL REPAIR INFORMATION
In addition to providing specific repair procedures for the
equipment listed at the beginning of this section, this
manual provides the following additional general instruc-
tions for dealing with repairs to various types of compo-
nents.
This information is designed to help you deal more effec-
tively with these components by providing basic service
knowledge and other useful tips.
Bearings & Bushings
Roller bearings, ball bearings, and bushings are used to
provide support to rotating shafts and other parts such as
gears, pulleys, and sprockets that are used to transmit
rotary motion. Over time, bearings and bushings may
require additional lubrication to transmit this rotary
motion with minimal friction, or may need replacement
due to normal operation and wear. Normal service for
bearings and bushings includes removal, cleaning,
inspection, lubrication, and replacement.
REMOVAL
Most bearings and bushings used on the listed equip-
ment can be easily removed by following the appropriate
detailed procedures found throughout this manual. Care
should always be exercised to avoid scratching or dam-
aging the bearing or bushing, the mounting shaft, and
surrounding components. Bearing or bushing removal is
usually necessary when excessive play or wobble is
noticed on the part it supports, when unusual noise or
vibration is apparent, or when a burning smell is present
at the bearing location.
CLEANING
Sealed bearings and bushings can be cleaned by careful
wiping with a cloth. Bearings with one-sided or remov-
able shields and plain bushings can be cleaned by
immersion in safety solvent, and brushing with a part
cleaning brush. Oil-impregnated bushings, and bushings
made of nylon or other synthetic materials, can be
cleaned with safety solvents, or wiped clean, but should
not be immersed in solvent for periods longer than that
necessary to remove heavy or caked-on build-ups of
grease. All petroleum-based solvents are flammable, so
appropriate precautions regarding flames, sparks, and
other ignition sources should always be observed.
Gasoline should never be used because of its volatility
and its highly toxic nature.
INSPECTION
Once cleaned, bearings can be properly inspected for
wear, scratches, visible damage such as corrosion,
cracked seals or scorching, and rough, or noisy, opera-
tion. Bushings can be visually checked for scratches,
uneven wear, or other visual damage.
LUBRICATION
After passing inspection, bearings and bushings should
be lubricated in accordance with factory specifications,
and reinstalled according to the appropriate installation
instructions. New bearings and bushings must also be
properly lubricated before use. For optimal performance,
and as a practical preventive maintenance measure,
bearings and bushings used in pairs or multiple sets
should all be replaced at the same time.
Belts & Pulleys
Belts and pulleys transmit rotary motion from power
sources to work components, providing the force needed
to drive transmissions, operate mower decks, and power
various attachments. This continual use eventually
causes belts to wear out, and over time may also require
the replacement of pulleys and pulley bearings.
Belt wear and various types of damage are easily
checked by visual examination, which is covered in
greater detail elsewhere in this manual. Pulleys may
also be checked visually for wear or apparent damage,
but pulley bearings usually require removal, cleaning,
and inspection to determine if replacement is required.
Belt and pulley life can be optimized by making sure that
proper belt tension and alignment are observed when
belts are installed. Proper belt tension and alignment
should also be maintained by performing periodic checks
and adjustments. In addition, only factory authorized
replacement belts will minimize problems caused by
size, thermal instability, and variations in quality.
Electrical Parts
The electrical parts used on these units have been
specifically engineered for outdoor power equipment,
and are designed to provide years of reliable operation.
As with all electrical components and systems, electrical
contacts must be kept clean and dry, and all terminations
must be securely fastened or connected. Also, all elec-
trical components, wiring, and connectors should be peri-
odically inspected for corrosion, signs of excessive heat
build-up, or other damage that signals that it is time to
repair or replace the item.
Specific procedures for electrical troubleshooting and
most common repairs is covered in separate sections of
this manual.
Summary of Contents for AGCO Allis 400 Series
Page 1: ......
Page 2: ......
Page 21: ...2 Troubleshooting Notes 2 4...
Page 31: ...3 10 3 Maintenance Maintenance Records...
Page 39: ...4 Adjustments Notes 4 8...
Page 79: ...8 Hand Controls Repair Notes 8 10...
Page 112: ...11 6 11 Belt Clutch Replacement Notes...
Page 135: ......
Page 136: ......