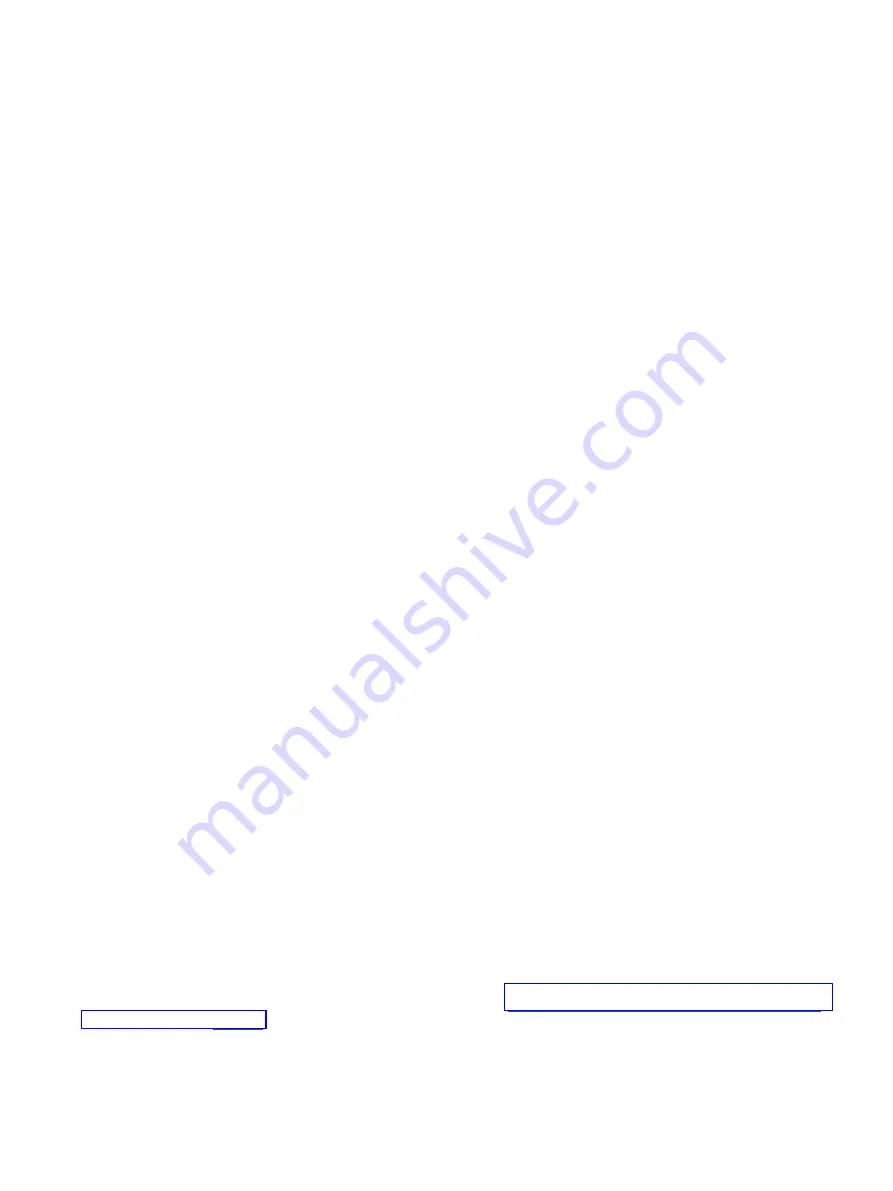
3KC0 manual transfer switching equipment
Manual, 09/2018, L1V30368969105-01
7
Introduction
1
1.1
Purpose of this manual
This manual describes the functions, commissioning and operation of the following transfer
switching equipment:
●
3KC0 manual transfer switching equipment (MTSE)
(MTSE = Manually Operated Transfer Switching Equipment)
This manual describes the following topics:
●
Product specifications
●
Mounting
●
Connection
●
Operation
●
Commissioning
●
Accessories
●
Corrective maintenance and fault rectification
●
Application examples
1.2
Target groups and required basic knowledge
This manual is intended for:
●
Users
●
Electrically skilled persons
●
Switchgear manufacturers
●
Maintenance personnel
A general knowledge of low-voltage power distribution is required to understand this manual.
Scale
The diagrams are not shown in the original size (1:1 scale).
Technical Support
You can find further support on the Internet (