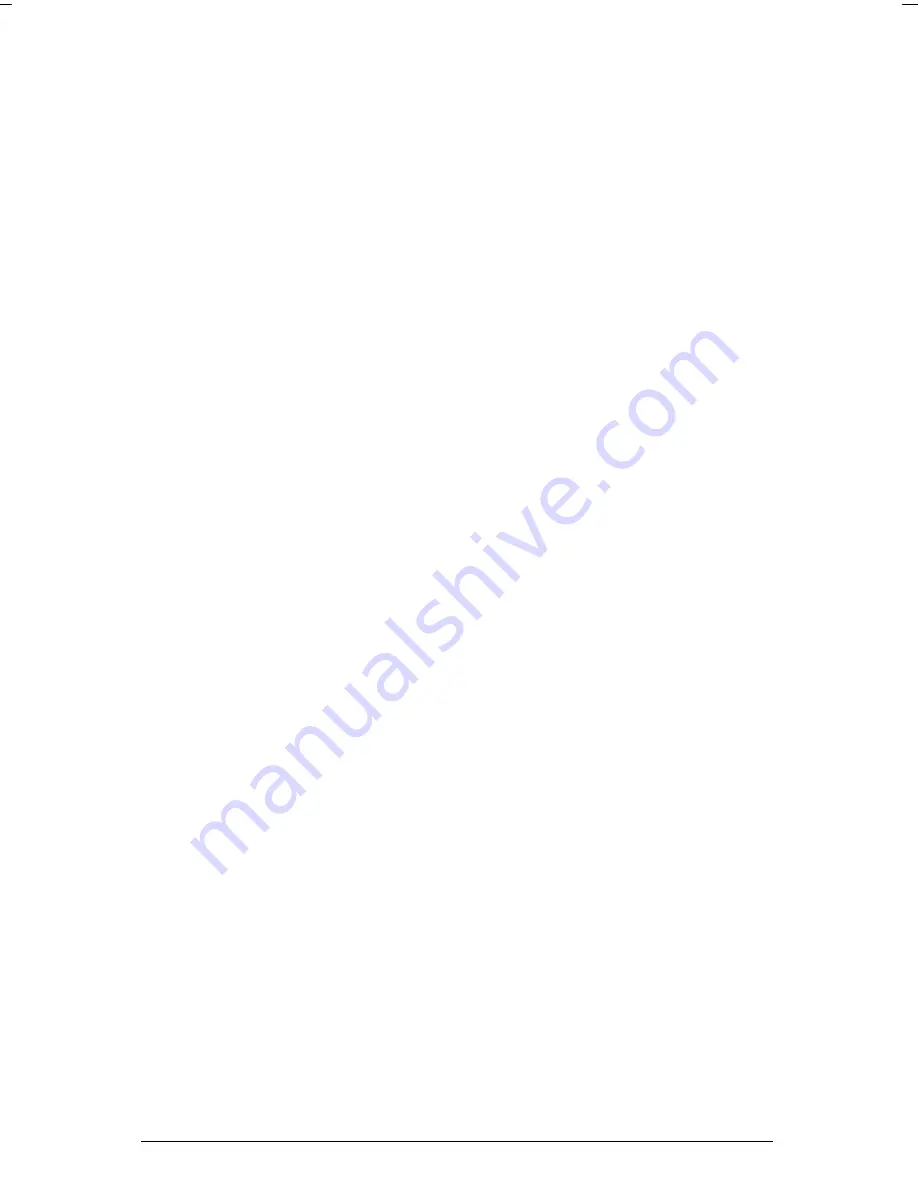
7ML19985CK03
Pointek CLS 300 – INSTRUCTION MANUAL
Page 23
Delay
The alarm actuation can be delayed for either, or both,
ON
alarm and
OFF
alarm conditions.
•
Set
S1-1
and
S1-2
. (Refer to Setup\ Switch Bank on p. 19.)
•
Adjust the delay time from 1 to 60 seconds by setting potentiometer
P1
Operation
After completing the setup, replace the Pointek CLS lid and lid clip. The unit is now in service,
providing level detection of your process.
Summary of Contents for Pointek CLS300
Page 1: ...POINTEK CLS 300 CAPACITANCE LIQUIDS SOLIDS Instruction Manual December 2001 OINTEK CLS 30 ...
Page 30: ...Notes ...
Page 31: ......
Page 32: ...c 7ML19985CK03 ...