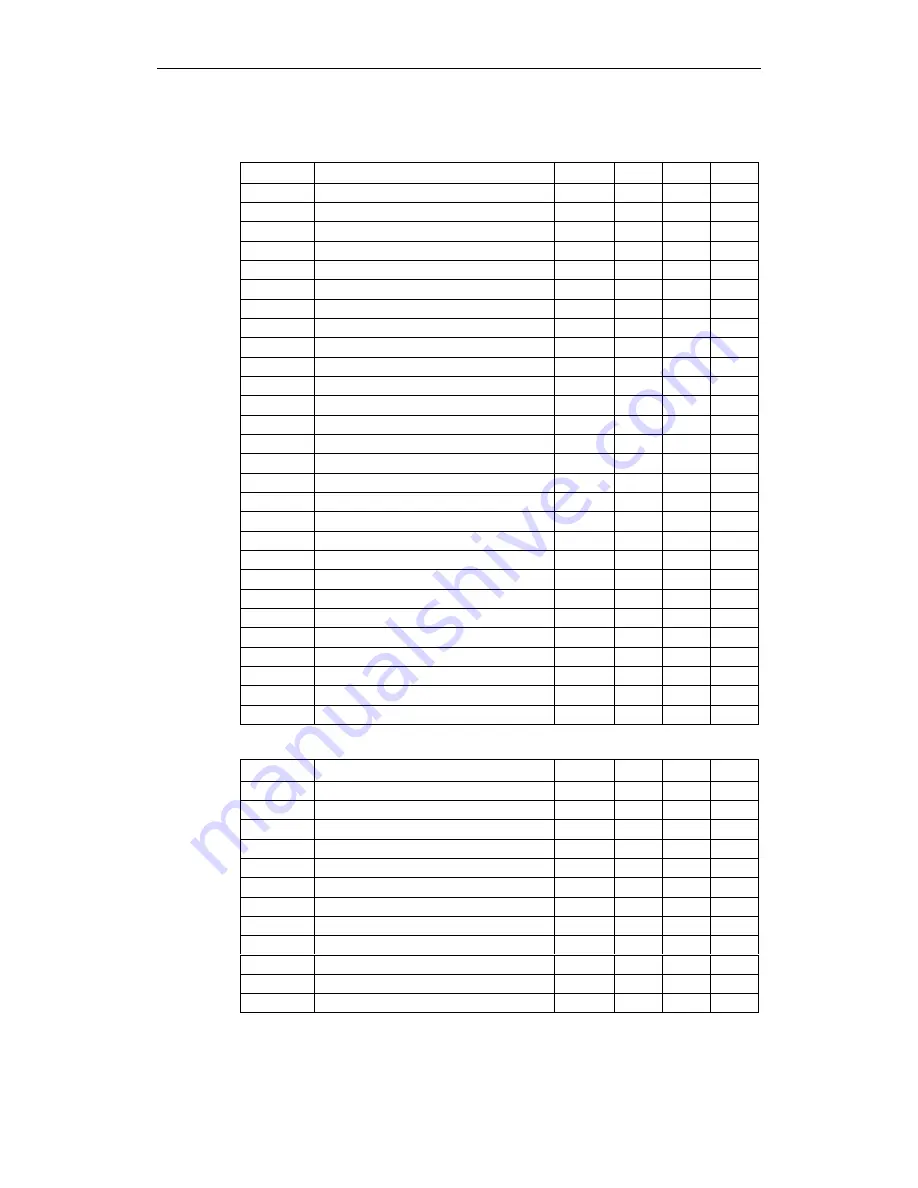
5 System Parameters
International English
MICROMASTER 440 Operating instructions
60
6SE6400-5CA00-0BP0
Drive Features (P0004 = 12)
Par. No.
Parametername
Default
Acc
WS
QC
P0005[3]
Display selection
21
2
CUT
N
P0006
Display mode
2
3
CUT
N
P0007
Backlight delay time
0
3
CUT
N
P0011
Lock for user defined parameter
0
3
CUT
N
P0012
Key for user defined parameter
0
3
CUT
N
P0013[20]
User defined parameter
0
3
CUT
N
P1200
Flying start
0
2
CUT
N
P1202[3]
Motor-current: Flying start
100
3
CUT
N
P1203[3]
Search rate: Flying start
100
3
CUT
N
r1205
Status flying-start on observer
-
3
-
-
P1210
Automatic restart
1
2
CUT
N
P1211
Number of restart attempts
3
3
CUT
N
P1215
Holding brake enable
0
2
T
N
P1216
Holding brake release delay
1.0
2
T
N
P1217
Holding time after ramp down
1.0
2
T
N
P1232[3]
DC braking current
100
2
CUT
N
P1233[3]
Duration of DC braking
0
2
CUT
N
P1234[3]
DC braking start frequency
0
2
CUT
N
P1236[3]
Compound braking current
0
2
CUT
N
P1237
Dynamic braking
0
2
CUT
N
P1240[3]
Configuration of Vdc controller
1
3
CT
N
r1242
CO: Switch-on level of Vdc-max
-
3
-
-
P1243[3]
Dynamic factor of Vdc-max
100
3
CUT
N
P1245[3]
Switch on level kin. buffering
76
3
CUT
N
P1247[3]
Dyn. factor of kinetic buffering
100
3
CUT
N
P1253[3]
Vdc-controller output limitation
10
3
CUT
N
P1254
Auto detect Vdc switch-on levels
1
3
CT
N
P2354
PID tuning timeout length
240
3
CUT
N
Motor Control (P0004 = 13)
Par. No.
Parametername
Default
Acc
WS
QC
r0020
CO: Act. frequency setpoint
-
3
-
-
r0021
CO: Act. frequency
-
2
-
-
r0022
Act. rotor speed
-
3
-
-
r0024
CO: Act. output frequency
-
3
-
-
r0025
CO: Act. output voltage
-
2
-
-
r0027
CO: Act. output current
-
2
-
-
r0029
CO: Flux gen. current
-
3
-
-
r0030
CO: Torque gen. current
-
3
-
-
r0031
CO: Act. torque
-
2
-
-
r0032
CO: Act. power
-
2
-
-
r0038
CO: Act. power factor
-
3
-
-
r0056
CO/BO: Status of motor control
-
3
-
-
http://nicontrols.com