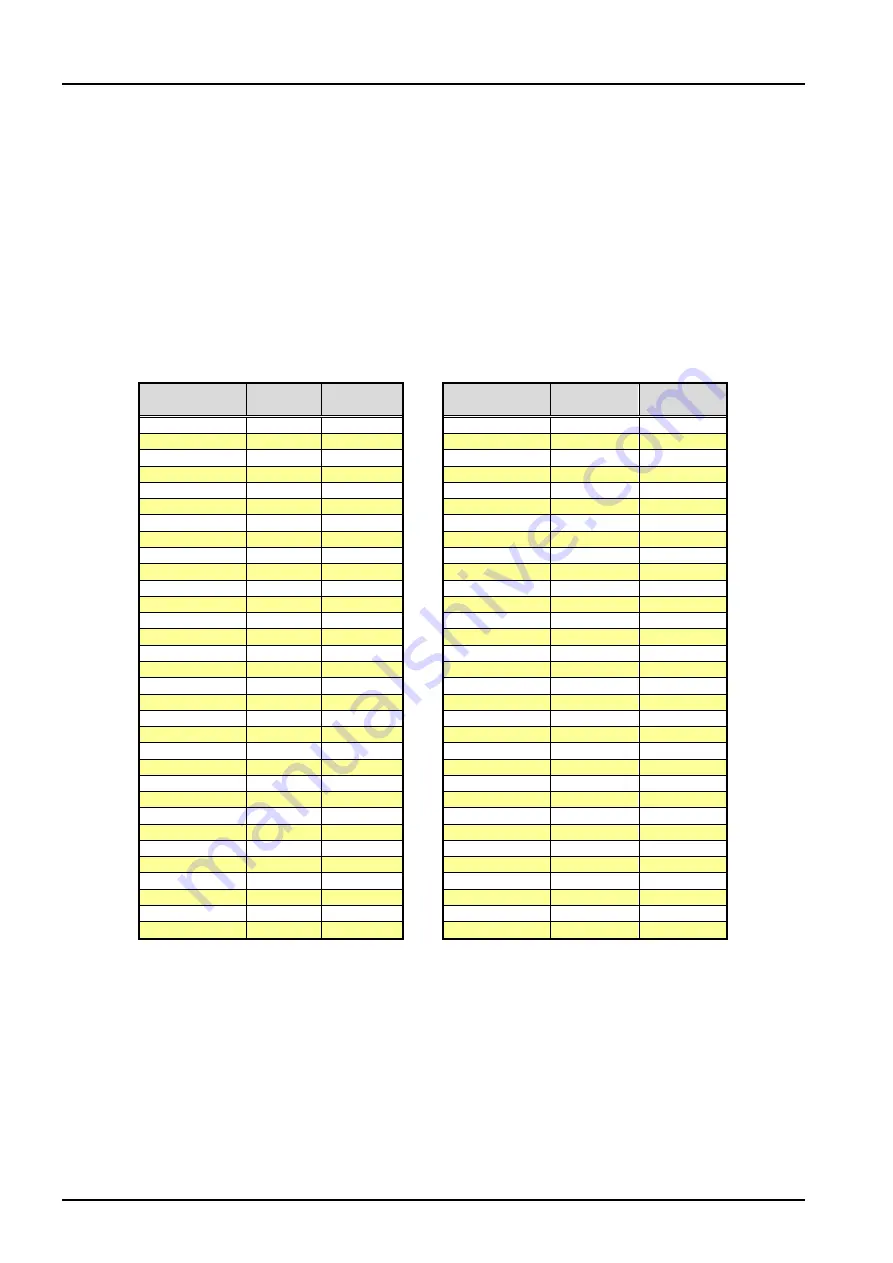
3
Features and Specification of 2D-TZ577 Card
About Output Signal Reset Patterns
3
- 16
3.8 About Output Signal Reset Patterns
Factory default settings are such that startup takes place with all general-purpose output signals being off (0).
You can change the state of general-purpose output signals at power-on by re-specifying the parameters listed
in the table below. Note that these parameters are intended to serve the following purpose as well: performing
general-purpose output signal reset operation (which is carried out with dedicated input signals) and selection of
reset pattern during the execution of Clr command.
Parameter setting options include "off," "on," and "hold." The following table lists parameters which are used on
the 2D
-TZ577 Card for general-purpose output resetting.
Table 3-10
A Listing of Output Signal Reset Pattern Parameters
Parameter
name
Leading
number
Last
number
Parameter
name
Leading
number
Last
number
ORST2000
2000
2031
ORST3024
3024
3055
ORST2032
2032
2063
ORST3056
3056
3087
ORST2064
2064
2095
ORST3088
3088
3119
ORST2096
2096
2127
ORST3120
3120
3151
ORST2128
2128
2159
ORST3152
3152
3183
ORST2160
2160
2191
ORST3184
3184
3215
ORST2192
2192
2223
ORST3216
3216
3247
ORST2224
2224
2255
ORST3248
3248
3279
ORST2256
2256
2287
ORST3280
3280
3311
OR
ST2288
2288
2319
ORST3312
3312
3343
ORST2320
2320
2351
ORST3344
3344
3375
ORST2352
2352
2383
ORST3376
3376
3407
ORST2384
2384
2415
ORST3408
3408
3439
ORST2416
2416
2447
ORST3440
3440
3471
ORST2448
2448
2479
ORST3472
3472
3503
ORST2480
2480
2511
ORST3504
3504
3535
ORST2512
2512
2543
ORST3536
3536
3567
ORST2544
2544
2575
ORST3568
3568
3599
ORST2576
2576
2607
ORST3600
3600
3631
ORST2608
2608
2639
ORST3632
3632
3663
ORST2640
2640
2671
ORST3664
3664
3695
ORST2672
2672
2703
ORST3696
3696
3727
ORST2704
2704
2735
ORST3728
3728
3759
ORST2736
2736
2767
ORST3760
3760
3791
ORST2768
2768
2799
ORST3792
3792
3823
ORST2800
2800
2831
ORST3824
3824
3855
ORST2832
2832
2863
ORST3856
3856
3887
ORST2864
2864
2895
ORST3888
3888
3919
ORST2896
2896
2927
ORST3920
3920
3951
ORST2928
2928
2959
ORST3024
3024
3055
ORST2960
2960
2991
ORST3056
3056
3087
ORST2992
2992
3023
ORST3088
3088
3119
Parameter ORST○○○○
has the default values of "0000000, 00000000, 00000000, and 00000000", and can be
set t
o specify "off," "on," and "hold" (= "0," "off," and "1") for 32 points. Leading number is assigned
from the left
side
.
For example, if ORST2000 is set to "*0000001, 00000000, 11110000, and 00000000," the following will result
when power to the Robot Controller is turned back on:
Output No. 2000:
Holds a state in which it was before power to the robot controller has been turned on
Output No. 2007:
On
Output Nos. 2016 to 2019: On