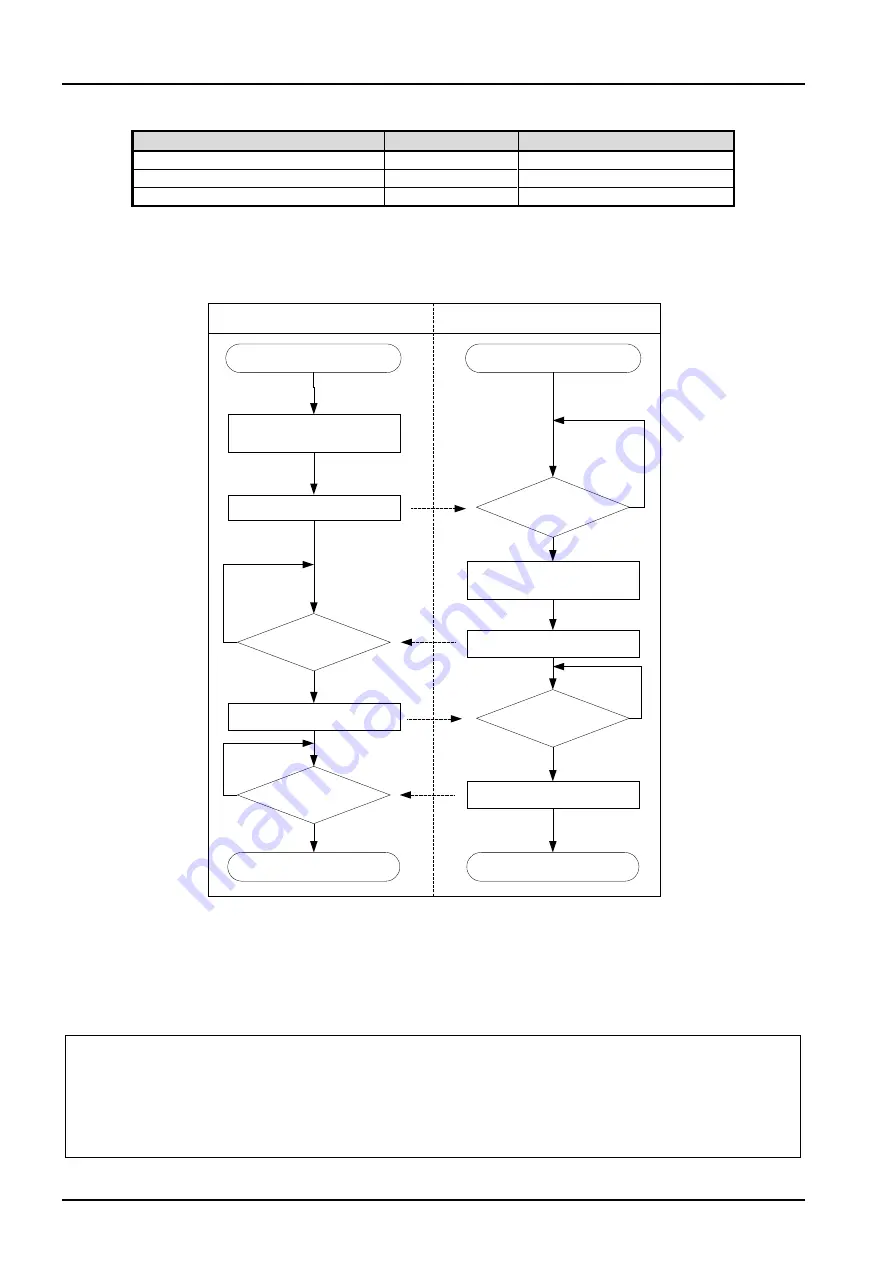
3
Features and Specification of 2D-TZ577 Card
Specification Relative to Robot Language
3
- 14
Table 3-8
An Example of Input/Output Signal Alignment between Master Station and Robot
Meaning
Master Station
*1
Robot
Data send/receive region
Data send region
Input: 2000 to 2015
PLC data write completed flag
WRTFLG
Input No. 2016
Robot data write completed flag
RDFLG
Output No. 2020
(*1)
For the purpose of explanation, a name is given to the Master Station input/output signal alignment.
Actually, you can make any input/output signal alignment in accordance with a Master Station instruction
manual that governs.
Start
End
Write one-word data
(data transmitted)
Write WRTFLG = 1
Input No. 2016 = 1?
Read Input Nos. 2000 to
2015 (data received)
Write Output No. 2020 = 1
RDFLG = 1?
Start
End
Master
Robot
YES
NO
NO
YES
Write WRTFLG = 0
Input No. 2016 = 0?
Write Output No. 2020 = 0
RDFLG = 0?
NO
YES
YES
NO
Figure 3-3
An Example of Use of Interlock
Below is an example of robot program which corresponds to the flowchart shown in Fig. 3-3. For information
about the Master Station-side program (ladder, etc.), refer to the instruction manual for the equipment being
used.
*Loop1: If M_In(2016) = 0 Then *Loop1
Mdata = M_InW(2000)
M_Out(2020) = 1
*Loop2: If M_In(2016) = 1 Then *Loop2
M_Out(2016) = 0