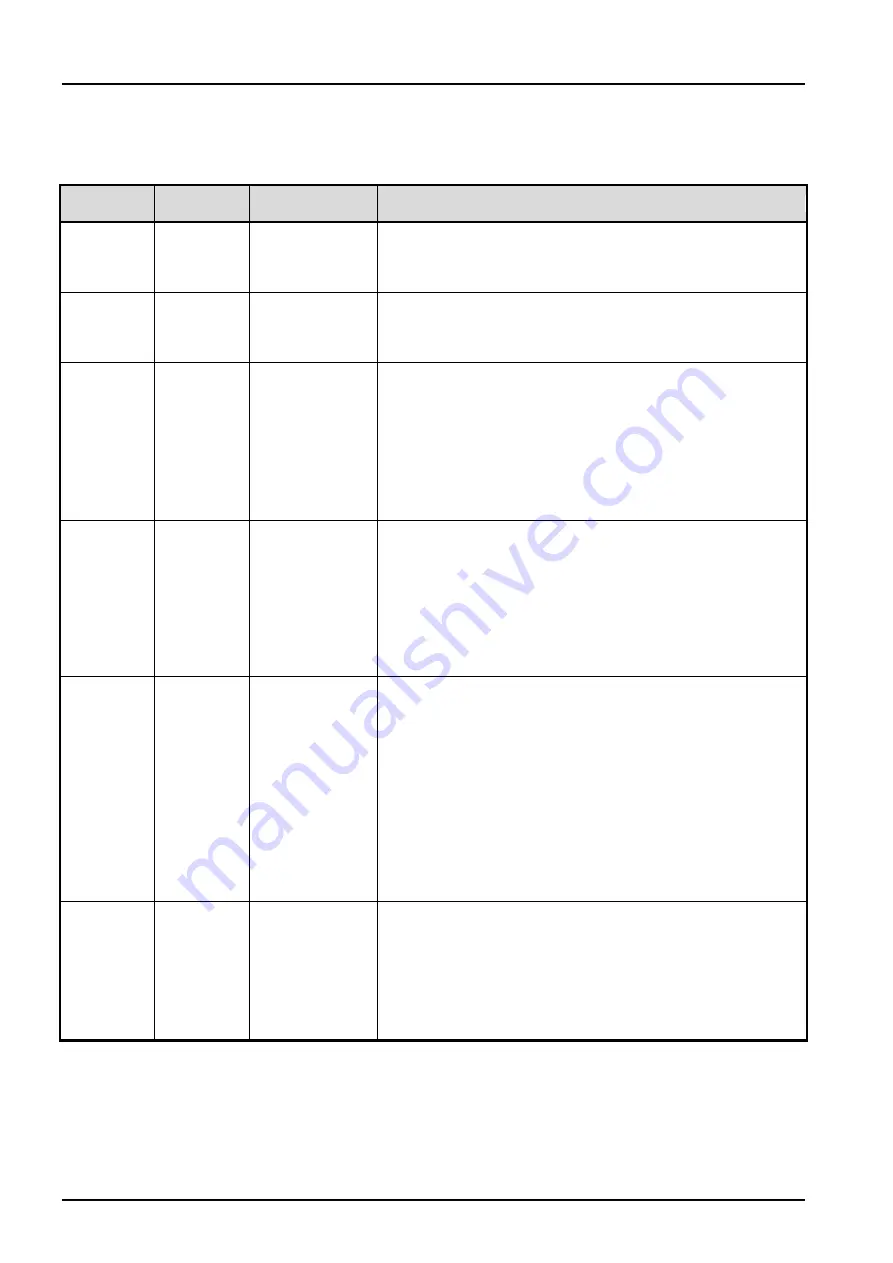
3
Features and Specification of 2D-TZ577 Card
Robot Parameters
3
- 10
3.4 Robot Parameters
Table 3-4
A Listing of Robot Parameters
Us
ed with PROFIBUS
Parameter
name
Initial value
Setting range
Description
STOP2
-1, -1
-
1 /2000 to 3951
A parameter that specifies a dedicated input signal number to
stop robot programs.
(Because the parameter "STOP" is fixed at "0", 2D
-TZ577 Card
uses "STOP2" to define an external stop signal.)
ORST2000
ORST2032
:
ORST3920
00000000,
00000000,
00000000,
00000000
0/1/*
A parameter that specifies value of output send data on the
2D
-TZ577 Card at the time of signal output reset.
(For details about related settings, see Section 3.8 Before
PBMODE
0
0/2
A parameter that switches the
operating mode of the 2D
-TZ577
Card between "normal" and "self-diagnosis."
Normal mode = 0, self-
diagnosis mode = 2
·
When the self-diagnosis identifies an anomaly, an error
message is displayed.
("H.8504: PROFIBUS self
-diagnosis shows occurrence of
an error.")
·
Return the operating mode to normal to continue with
normal operation.
PBMC
1
1/2
A parameter that designates Master Station as Class 1 or Class
2.
Class 1 Master Station is designated at factory default. To use
"Class 2
," choose another parameter setting.
1: Class 1 Master (effected when the station number setting
parameter PBNUM shown below is used)
2:
Class 2 Master (effected when changes of station numbers
are made from Class 2 Master Station
-
with PBNUM not
being used)
P
BNUM
126
-
1 to 125
A
parameter that specifies station number for the 2D
-TZ577
Card.
0 to 125: Station number setting value (Rewriting of station
number settings takes place within the flash ROM as well.)
-1: Station number clear (Station number settings within the
flash ROM are cleared.)
* After the station numbers are cleared, the
value 126
is taken
on.
* If "No_Add_Chg" is specified with "true" when making
station number settings from Class 2 Master Station,
2D-TZ577 Card is disabled for change of station numbers.
To cancel this setting, clear station numbers with "PBNUM
= -1."
E8500
0
0/1
A parameter that is used to temporarily reset an error state
when PROFIBUS
-related error (indicated by a number in the
8500s) occurred.
(1: Resettable (But no communications are to be carried out.) /
0: Always error during the occurrence of an anomaly in the link)
* This parameter does not require power supply resetting
on the Robot Controller. The initial value of 0 will return if
power supply resetting is done.