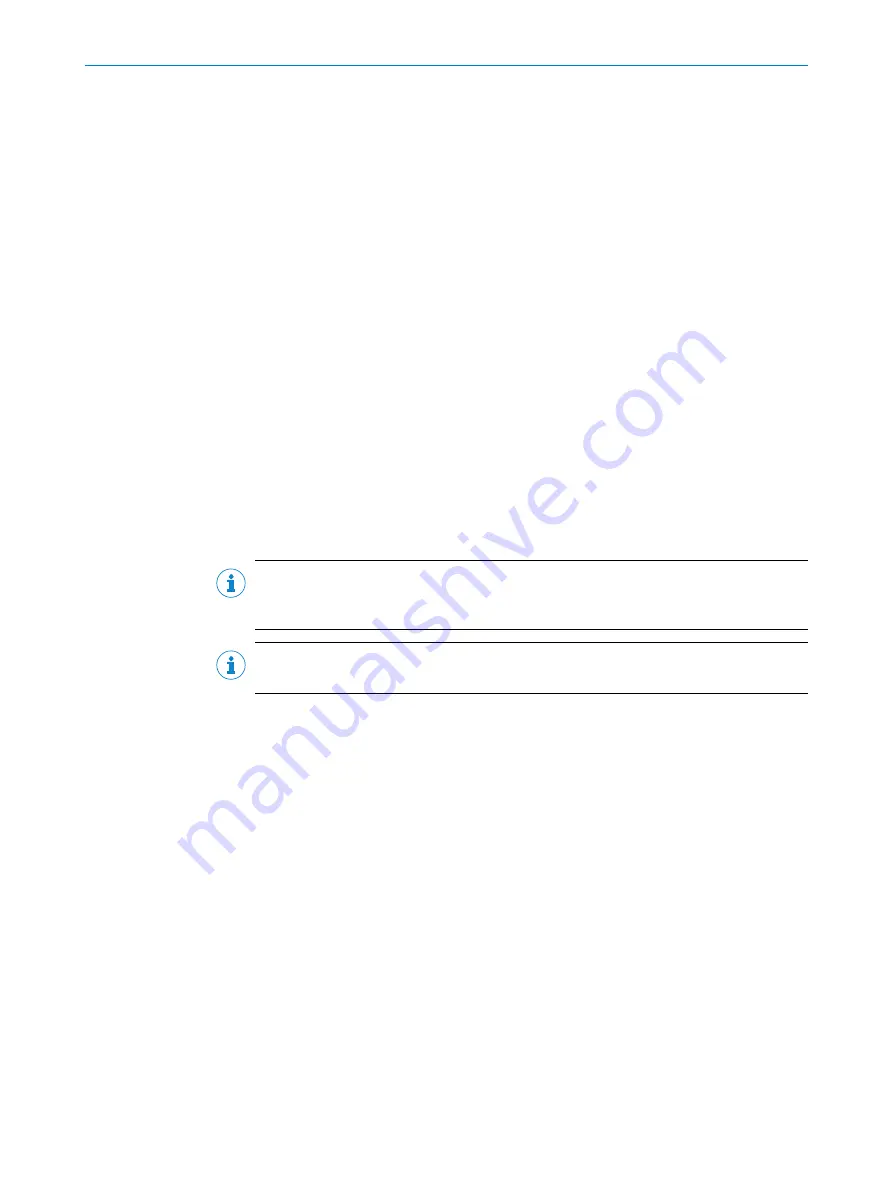
•
1. SICK safety system
•
2. Robot controller
•
3. Safety command devices
1. SICK safety system
The safety system provides output signals for the robot controller and receives input
signals from the primary protective device and the safety laser scanner. In addition, the
safety controller receives input signals from safety command devices for safe handling
of the robot in different situations. The safety logic in the Flexi Classic safety controller
allows triggering of the robot’s safety functions.
2. Robot controller
The robot controller requires the emergency stop and protective stop safety functions.
These safety functions are triggered by the safety controller.
3. Safety command devices
Safety command devices provide the necessary conditions to perform the actions
defined by the safety functions.
Safety system types
The safety system offers two options for performing a reset after a protective stop.
•
sBot Stop with manual reset
•
sBot Stop with automated reset
NOTE
Implementation with automated reset is not suitable for every application. Possible use
must be checked by means of the risk assessment.
NOTE
Restart implementation is the responsibility of the manufacturer.
sBot Stop with manual reset
Manual reset: the reset pushbutton is connected to the safety controller and its signal
is analyzed there. The reset signal is effective for the protective stop. Reset after an
emergency stop and the emergency stop itself must be implemented by the manufac‐
turer (e.g. in the robot controller).
A manual reset and a manual restart are necessary after an emergency stop. Depend‐
ing on the robot controller and the stop category used, several steps may be necessary
for the protective stop. These may include error acknowledgment, switching on the drive
and starting the program.
PRODUCT DESCRIPTION
3
8023421/12KF/2019-01-22 | SICK
O P E R A T I N G I N S T R U C T I O N S | sBot Stop
15
Subject to change without notice