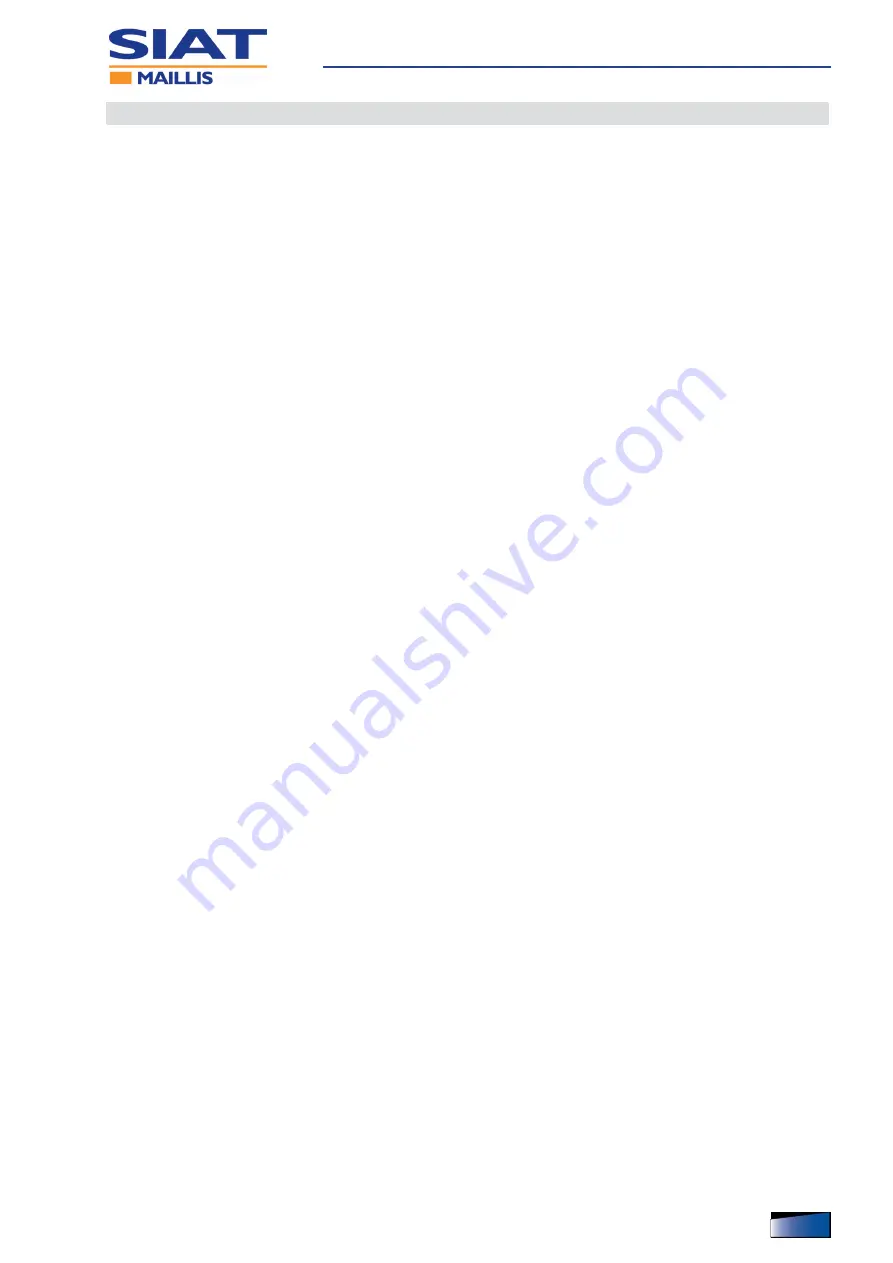
IDM 510-140-0
Control system
63
English language
Operation and maintenance manual
Recommendations on Operation and Use
– Consult the user manual, in particular during the first use, and make sure that you
fully understand its content.
– Find out the position and function of the controls and simulate some operations
(in particular start and stop) in order to acquire familiarity.
– Only use the unit according to the manufacturer’s instructions and do not tamper
with the devices in order to obtain different performance from that expected.
– Make sure that all the safety devices are properly installed and efficient.
– DO NOT use or allow other persons to use the machine if the safety devices are
faulty, disabled and/or incorrectly installed.
– If troubles arise, do NOT continue to use the machine. Stop it immediately and
restart only after restoring the normal operating condition.
– DO NOT leave the machine unattended during operation and DO NOT leave it at
the end of the work without stopping it to safety conditions.
–
In addition to the recommendations, carefully read the SAFETY WARNINGS
(see “General information and safety”) in order to reduce the risks of
man-machine interactions.
–
Caution is always necessary. Safety is also the responsibility of all the per-
sons interacting with the machine throughout its operating life.
Summary of Contents for ProWrap 16_H_FM
Page 14: ...Safety information IDM 510 004 5 12 English language Operation and maintenance manual...
Page 84: ...Control system IDM 510 140 0 82 English language Operation and maintenance manual...
Page 102: ...Disposal and scrapping IDM 510 106 0 100 English language Operation and maintenance manual...