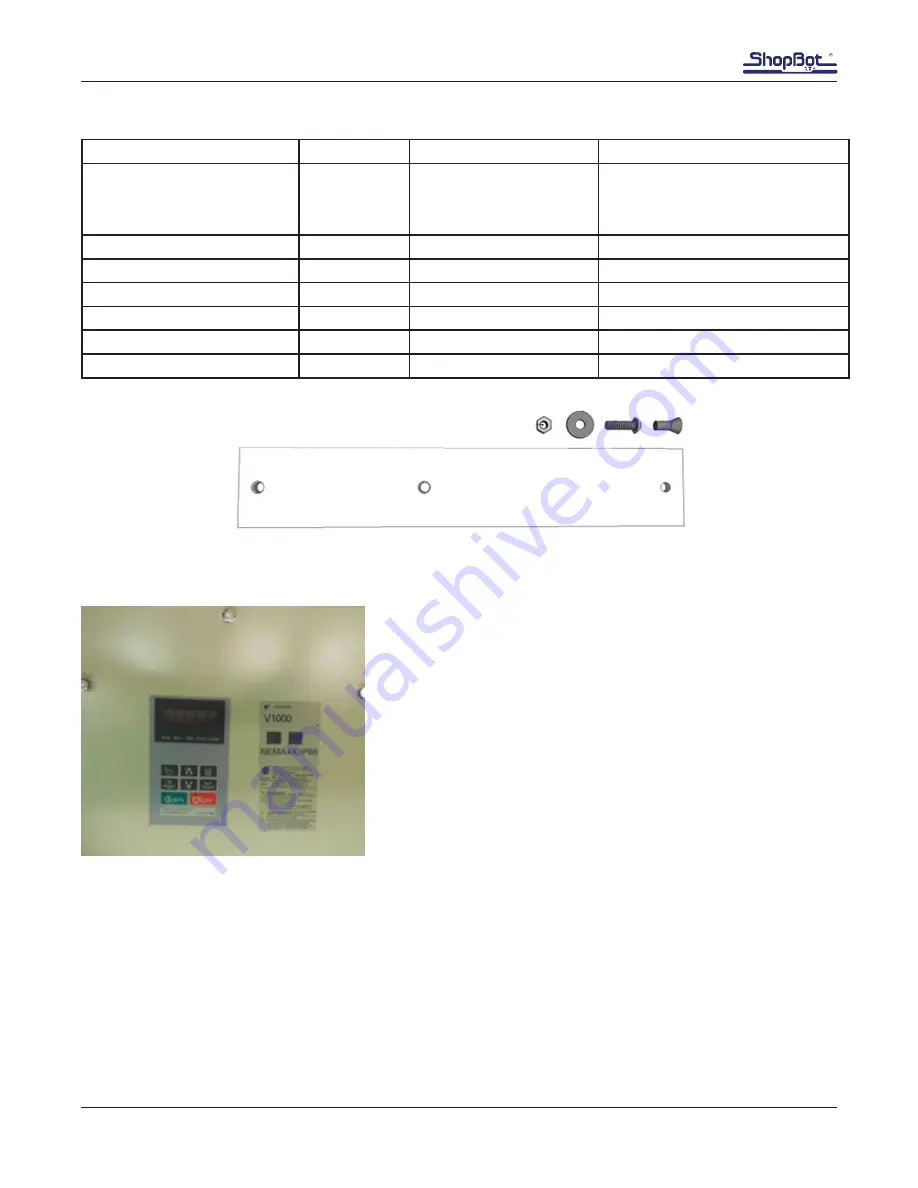
Section 6: Spindle and VFD Installation • May 2, 2016
© Copyright 2016 ShopBot Tools, Inc.
page 6-2
Hardware
Part Name
Quantity
ShopBot Part Number
Notes
Yaskawa V1000 VFD
1
Part numbers vary based on the
options available. Refer to paper
work to determine model.
VFD Mounting Kit V1000
1
003065
FHSCS 1/4-20x5/8
2
003064
BHSCS 1/4-20x3/4
4
002135
flat washer 1/4 USS Z G5
6
000534
Nylock hex nut 1/4-20 Z
6
000454
VFD mounting strap
2
003036
Determining the VFD Model
There are two main types of VFDs, a 10” model and a 16”
model. These can be easily differentiated by their size and
model numbers. Model numbers are found on the front of the
VFD underneath the “RUN” and “STOP” buttons as shown on
left.
There are five different amperage configurations. These will
not impact installation, but it may be beneficial information for
tech support.
Voltage Amperage (Determines Size)
An example model number is shown below.
The model number is CIMR–VU2A0040GAA.
The first bold and underlined number in the written example is the voltage.
2 = 200-240 Vac, 3-phase
4 = 380-480 Vac, 3-phase
Summary of Contents for PRSalpha
Page 38: ...Section 3 Gantry Installation May 2 2016 Copyright 2016 ShopBot Tools Inc page 3 8 ...
Page 49: ...Section 4 Cable Carrier Installation May 2 2016 Copyright 2016 ShopBot Tools Inc page 4 11 ...
Page 50: ...Section 4 Cable Carrier Installation May 2 2016 Copyright 2016 ShopBot Tools Inc page 4 12 ...
Page 56: ...Section 5 Control Box Installation May 2 2016 Copyright 2016 ShopBot Tools Inc page 5 6 ...
Page 66: ...Section 6 Spindle and VFD Installation May 2 2016 Copyright 2016 ShopBot Tools Inc page 6 10 ...
Page 78: ...Section 8 Wire and Cable Routing May 2 2016 Copyright 2016 ShopBot Tools Inc page 8 8 ...
Page 80: ...Section 9 PRS Alpha Control Box Wiring May 2 2016 Copyright 2016 ShopBot Tools Inc page 9 2 ...