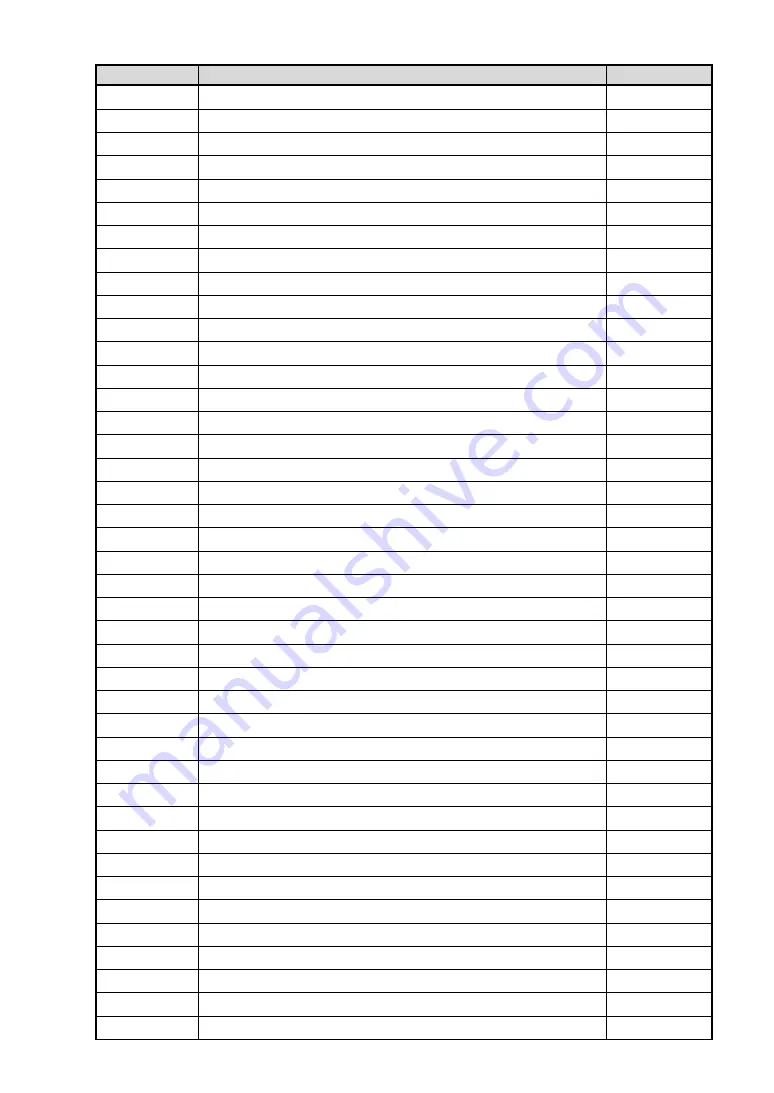
- 107 -
Character
Setting Item, Setting Range
Data
Step 4 EVT5 high limit alarm value
Step 5 SV
Step 5 time
Step 5 Wait value
Step 5 EVT1 alarm value
Step 5 EVT1 high limit alarm value
Step 5 EVT2 alarm value
Step 5 EVT2 high limit alarm value
Step 5 EVT3 alarm value
Step 5 EVT3 high limit alarm value
Step 5 EVT4 alarm value
Step 5 EVT4 high limit alarm value
Step 5 EVT5 alarm value
Step 5 EVT5 high limit alarm value
Step 6 SV
Step 6 time
Step 6 Wait value
Step 6 EVT1 alarm value
Step 6 EVT1 high limit alarm value
Step 6 EVT2 alarm value
Step 6 EVT2 high limit alarm value
Step 6 EVT3 alarm value
Step 6 EVT3 high limit alarm value
Step 6 EVT4 alarm value
Step 6 EVT4 high limit alarm value
Step 6 EVT5 alarm value
Step 6 EVT5 high limit alarm value
Step 7 SV
Step 7 time
Step 7 Wait value
Step 7 EVT1 alarm value
Step 7 EVT1 high limit alarm value
Step 7 EVT2 alarm value
Step 7 EVT2 high limit alarm value
Step 7 EVT3 alarm value
Step 7 EVT3 high limit alarm value
Step 7 EVT4 alarm value
Step 7 EVT4 high limit alarm value
Step 7 EVT5 alarm value
Step 7 EVT5 high limit alarm value
Step 8 SV