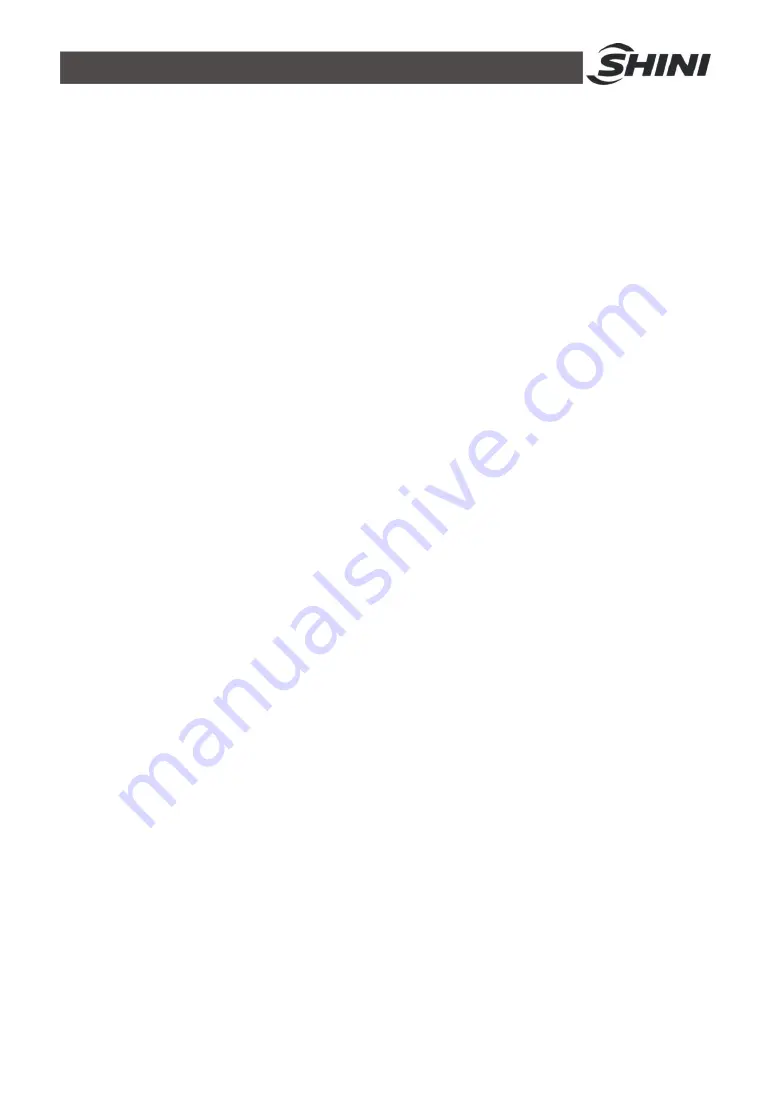
6(44)
Picture 6-10: Installation of Feed Box, Feed Port and Storage Box 3 ............... 35
Picture 6-11: Installation of Feed Box, Feed Port and Storage Box 5 ............... 36
Picture 6-12
:
Step 1 of Gear box Dismantlement ............................................ 36
Picture 6-13: Step 1 of Left /Right Bearing Base Dismantlement ..................... 36
Picture 6-14: Step 2 of Left / Right Bearing Base Dismantlement .................... 37
Picture 6-15: Step 3 of Left/ Right Bearing Base Dismantlement ..................... 37
Picture 6-16
:
Step 1 of Bearing Dismantlement .............................................. 37
Picture 6-17
:
Step 2 of Bearing Dismantlement .............................................. 38
Picture 6-18
:
Step 3 of Bearing Dismantlement .............................................. 38
Picture 6-19: Installation of Reduction Gear 1 .................................................. 38
Picture 6-20: Installation of Reduction Gear 2 .................................................. 39
Picture 6-21: Installation of Reduction Gear 3 .................................................. 39
Picture 6-22: Star Screws ................................................................................. 41
Picture 6-23: Machine Cleaning ........................................................................ 42