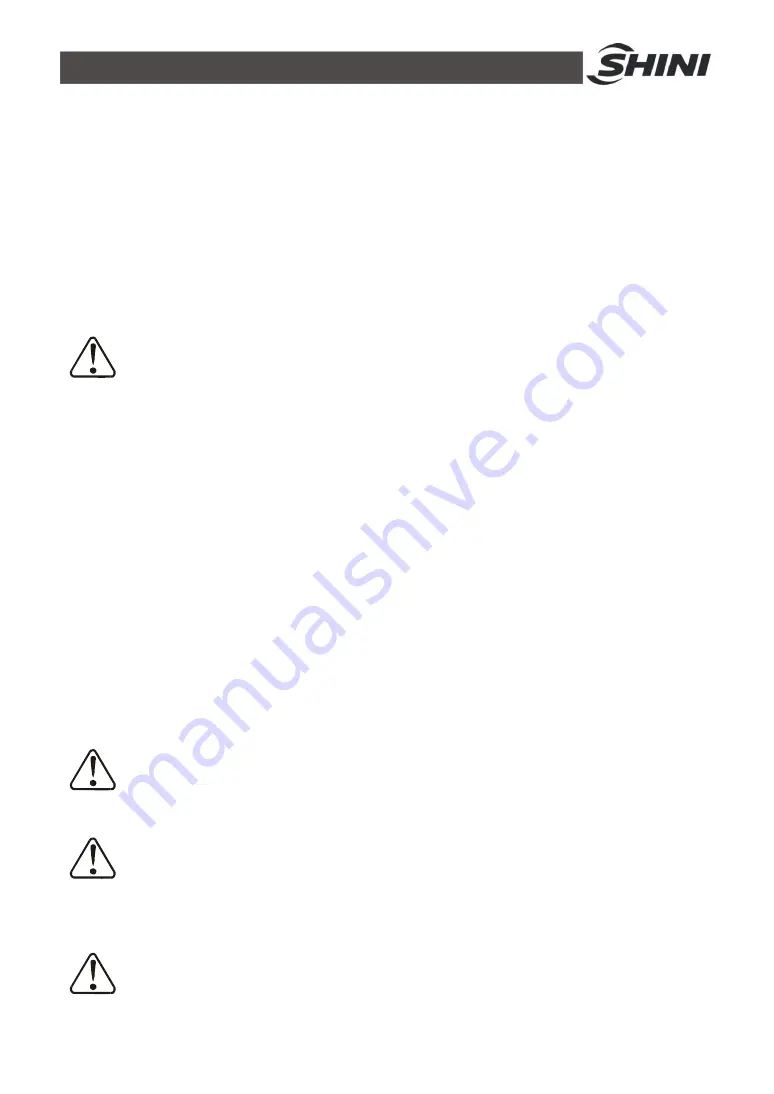
13(41)
4) Use plastic film to cover the machine tightly to prevent the machine from
dust and rains.
Working environment
The machine should be operated:
1) Indoors in a dry environment with max. tempe45
℃
and humidity
no more than 80%.
Do not use the machine:
1) If it is with a damaged cord.
2) On a wet floor or when it is exposed to rain to avoid electric shock.
3) If it has been dropped or damaged until it is checked or fixed by a
qualified serviceman.
4) This equipment works normally in the environment with altitude over
3000m.
5) At least 1m surrounding space is requested when this equipment is
running. Keep this equipment away from flammable sources at least two
meters.
6) In the work area of vibration and strong magnetic force
Rejected parts disposal
When the equipment has run out its life time and can not be used any more,
unplug the power supply and dispose of it properly according to local code.
Fire hazard!
In case of fire, CO
2
dry powder fire extinguisher should be applied.
Flammable materials or materials which are contaminated by flammable
substances/liquid may not be processed in the granulator. Serious risk of
fire or explosion may cause personnel injury.
It is very important to tighten the screw as required torque.