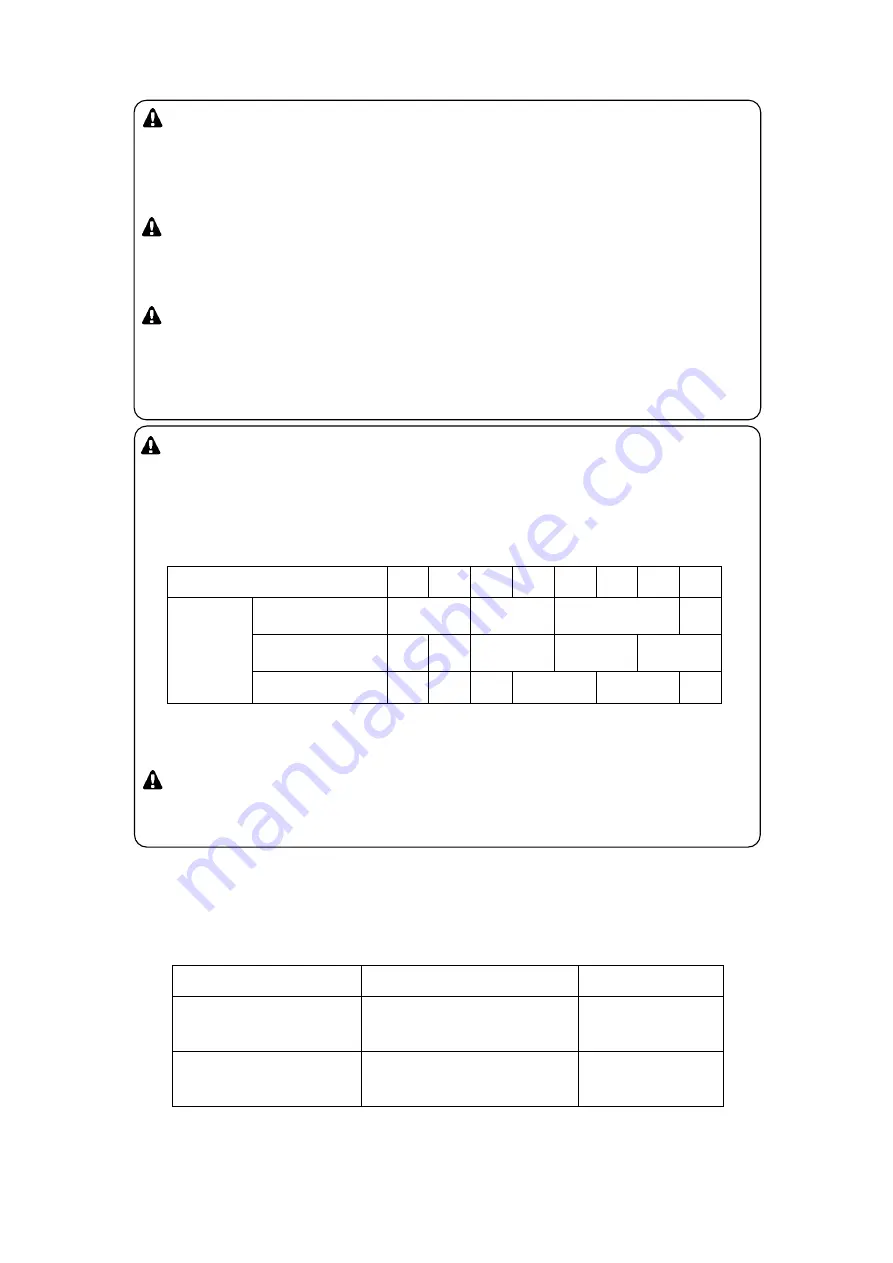
- 26 -
8-5
.
.
.
.
Welding Work
Warning: Suffocation from Welding Fume
•
Always be sure to wear a fume-proof mask when welding as the fumes
generated during welding include harmful gases and dust. Also be
careful that the wind direction is not such that it will cause fumes to be
inhaled and always operate the equipment in a well-ventilated area.
Warning: Fire
•
Keep any ignitable items (such as fuel, gas and paint) or inflammable
items away from the work area due to the scattering of weld spatter that
occurs during welding.
Warning: Electromagnetic Interference
•
Persons using a heart pacemaker are not allowed near the welder or
welding work area while welding is being performed without the
permission of a doctor. The welder generates a magnetic field while
energized that can negatively affect pacemaker operation.
Caution: Injury to Eyes and Skin
•
Always be sure to wear arc-proof glasses (refer to the table below),
clothes that completely cover the skin and other protective gear when
welding to protect the eyes and skin from harmful light rays generated
during welding.
Standards for Arc-Proof Glasses
(
Japanese Industrial Standard
)
Filter No.
7
8
9
10
11
12
13
14
Shielded Metal
Arc Welding
35-75
76-200
201-400
400
Scratch Start TIG
Welding
-
-
100 or less 100-300
301-400
Weld
Current
(A)
Gouging
-
-
-
126-225
226-350
-
•
Always be sure to wear leather gloves, apron, shoe covers, arc-proof
glasses (face shield), safety shoes, hard hat and long-sleeve clothing to
protect against the scattering of weld spatter that occurs during welding.
Caution: Electric Shock
•
If wearing gloves, be sure to always wear gloves with dry insulation
properties. Do not wear gloves that are damaged or wet.
You can select a weld mode with the type of welding being performed. Select a
weld mode by referring to the recommended modes in the table below.
Weld Modes Table (Recommended)
Mode Name
Applications
Welding Position
DROOP-STANDARD
/
GOUGING
Welding of pipes, tanks and
similar items
Gouging
Vertical
and
Upward
CC-CELLULOSE
/
SCRATCH START TIG
Welding of structures and
finishing welding
TIG welding
Horizontal
and
Downward
Summary of Contents for DGW400DM-C
Page 2: ......
Page 44: ...41 14 Engine Wiring Diagram...
Page 45: ...42 15 Generator Wiring Diagram...
Page 46: ...43...
Page 47: ...44...
Page 48: ...45 2013...