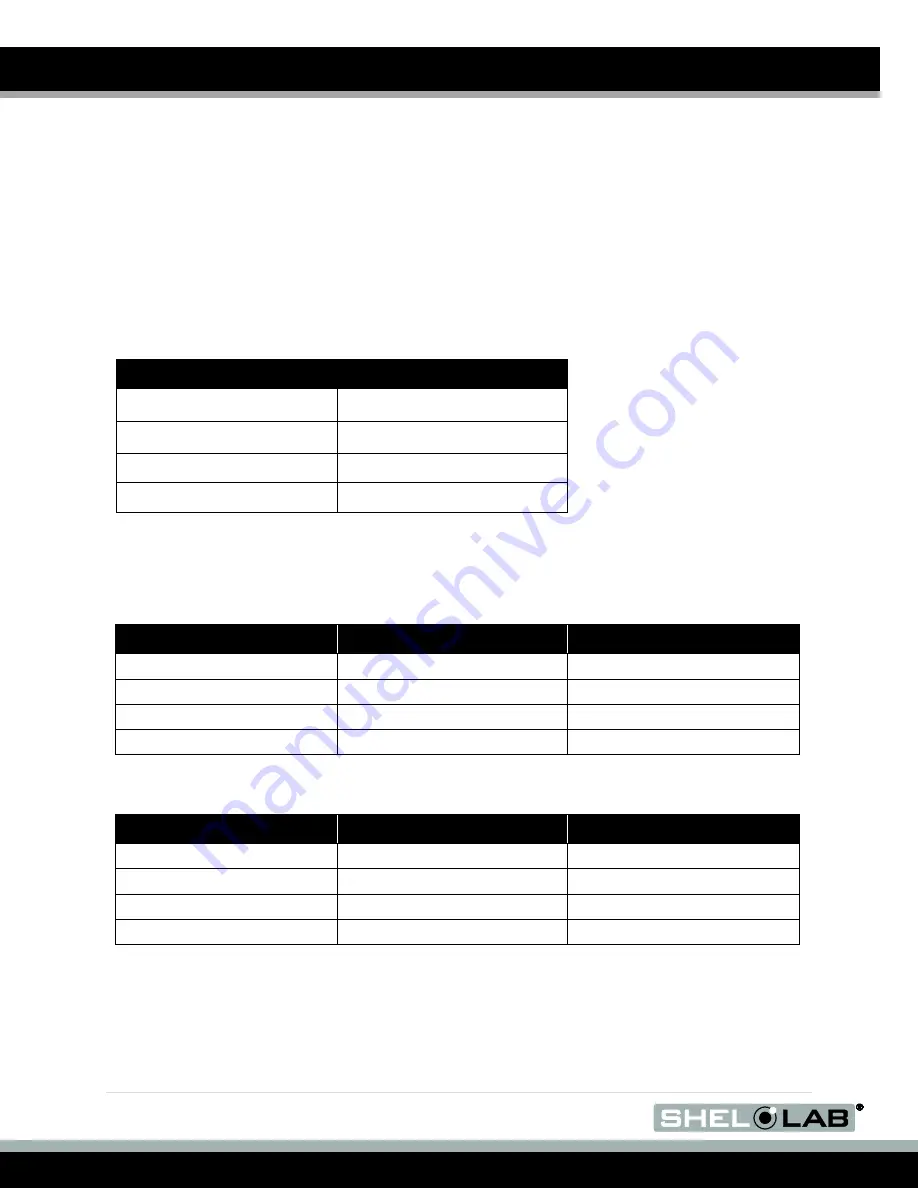
40 |
P a g e
UNIT SPECIFICATIONS
These ovens are 220 - 240 voltage units. Please refer to the oven
’s data plate for individual
electrical specifications.
Technical data specified applies to units with standard equipment at an ambient temperature of
25°C and a voltage fluctuation of ±10%. The temperatures specified are determined in accordance
to factory standard following DIN 12880 respecting the recommended wall clearances of 10% of the
height, width, and depth of the inner chamber. All indications are average values, typical for units
produced in the series. We reserve the right to alter technical specifications at all times.
W
EIGHT
Model
Shipping
SMO10HP-2
660 lbs. / 299.4kgs
SMO14HP-2
555 lbs. / 251.7kgs
SMO34HP-2
675 lbs. / 306.2kgs
SMO38HP-2
1025 lbs. / 465.0kgs
D
IMENSIONS
By Inches
Model
Exterior W × D × H
Interior W × D × H
SMO10HP-2
44 x 28.25 x 55.1 in
30 x 19.75 x 30.1 in
SMO14HP-2
59 x 29 x 57 in
44 x 20.5 x 36 in
SMO34HP-2
43 x 34.25 x 85.5 in
31.5 x 26 x 60.5 in
SMO38HP-2
68.5 x 33 x 78.5 in
48 x 25.5 x 54 in
By centimeters
Model
Exterior W × D × H
Interior W × D × H
SMO10HP-2
112 x 72 x 142 cm
65.5 x 68 x 62 cm
SMO14HP-2
149.8 x 73.6 x 144.8 cm
76 x 50 x 77 cm
SMO34HP-2
109 x 87 x 217 cm
80 x 66 x 153.6 cm
SMO38HP-2
174 x 83x 199 cm
121 x 64.7 x 137 cm
Summary of Contents for SM10HP-2
Page 17: ...17 P a g e GRAPHIC SYMBOLS CONTINUED This page left blank ...
Page 20: ...20 P a g e OPERATION CONTINUED This page left blank ...
Page 27: ...27 P a g e OPERATION CONTINUED This page left blank ...
Page 33: ...33 P a g e OPERATION CONTINUED This page left blank ...
Page 43: ...43 P a g e REPLACEMENT PART LIST This page left blank ...
Page 44: ......