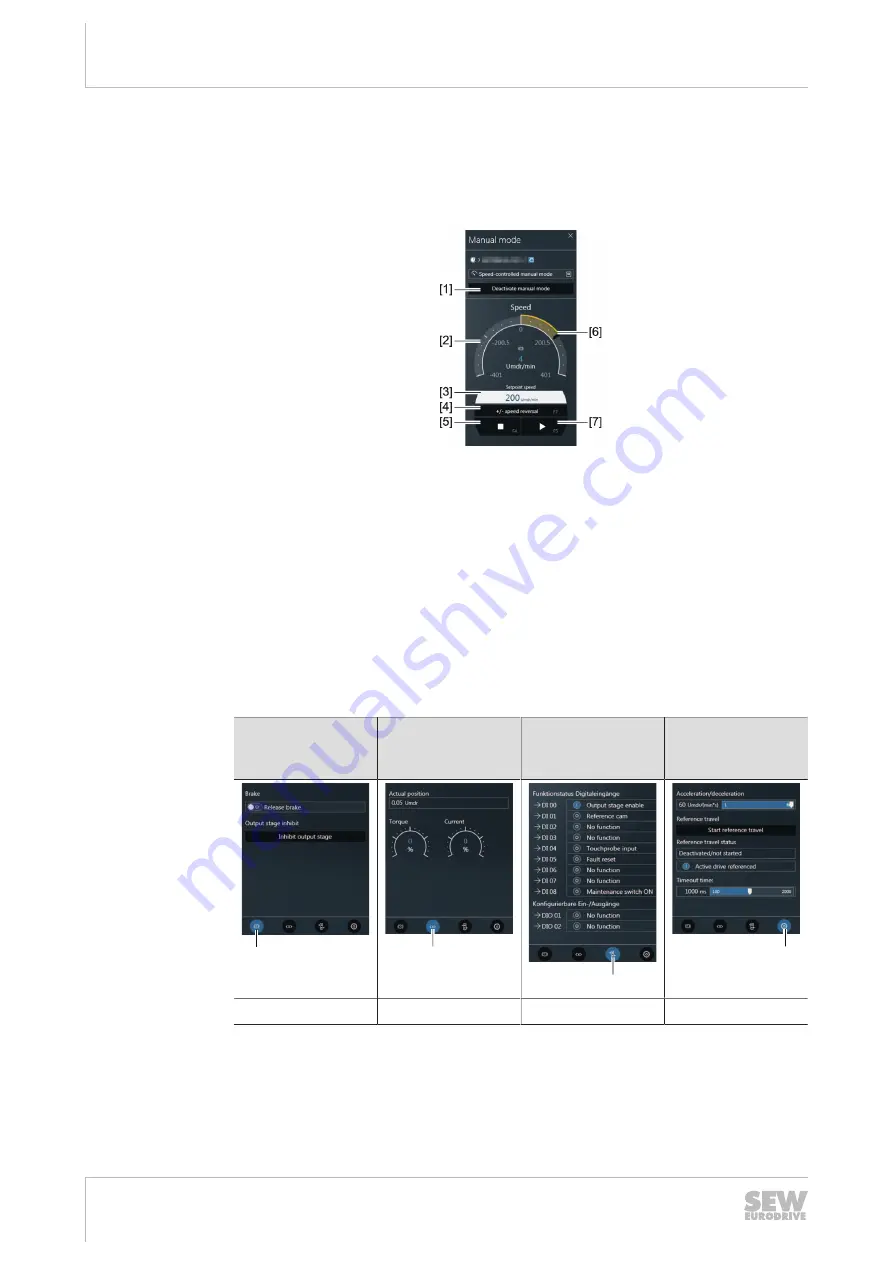
7
Operation
Manual mode with MOVISUITE®
Operating Instructions – MOVIMOT
®
advanced
128
7.3.2
Control in manual mode
Manual mode window
Once manual mode has been successfully activated, you can control the device using
the controls in the MOVISUITE
®
"Manual mode" window.
36028819001133963
Controller
1. Set the setpoint speed using the edit box [3] or graphic input [6].
2. To specify the direction of rotation, click the button [4].
3. To enable the device, click the button [7].
4. To stop the device, click the button [5].
The "Speed" group [2] shows the actual speed of the device.
Advanced functions and displays of manual mode
The following functions are available in manual mode using MOVISUITE
®
:
Release brake
Disable output
stages
Actual values
Digital inputs and
outputs
Acceleration
Reference travel
Timeout
[1]
[2]
[3]
[4]
Key [1]
Key [2]
Key [3]
Key [4]
25891936/EN – 05/2020