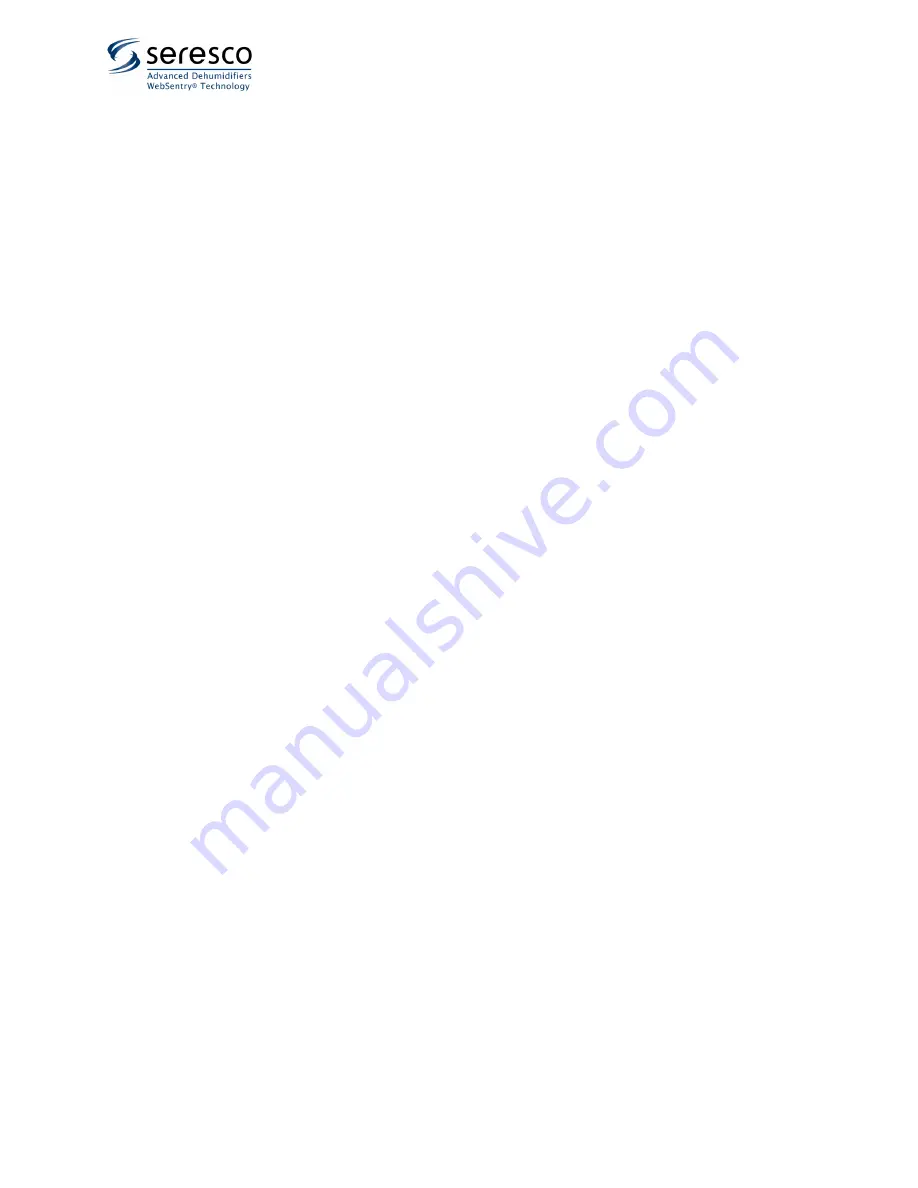
M
–
Basic
Maintenance
OMM.M.S.ZZ.00
M
‐
3
June
2018
Specific
Components
Maintenance
Actual
maintenance
plan
may
vary
from
installation
to
installation,
yet
there
are
several
key
components
from
maintenance
prospective.
If
needed,
contact
respective
component
manufacturer
for
additional
maintenance
information.
Filters
Ensure
air
filters
are
clean.
Dirty
air
filters
will
negatively
affect
dehumidifier
performance
and
lifetime
Frequency
of
filters
replacement
will
vary
based
on
air
quality,
dehumidifier
usage,
facility
type,
etc.
Make
sure
to
replace
filters
regularly
Replace
with
filters
of
equivalent
size
and
rating
–
refer
to
dehumidifier
details
(compartment
stickers,
etc.)
Insulation
Inspect
dehumidifier
insulation,
exposed
to
airstream
for
microbial
growth
(i.e.,
mold).
If
there
is
evidence
of
microbial
growth
on
the
interior
insulation,
the
insulation
should
be
removed
and
replaced
prior
to
operating
the
dehumidifier.
Air
‐
Side
Coils
Warning:
Hazardous
chemicals!
Cleaning
agents
can
be
highly
acidic
or
alkaline.
Handle
all
chemicals
carefully
and
use
appropriate
personal
protective
equipment
(PPE).
Refer
to
the
cleaning
agent
manufacturer's
Materials
Safety
Data
Sheet
(MSDS)
for
safety
and
handling
information.
Failure
to
follow
all
safety
instructions
could
result
in
serious
injury
or
death.
Warning:
Hazardous
pressures!
Coils
containing
refrigerant
under
pressure
must
not
be
cleaned
using
a
solution
over
150
ºF.
Failure
to
follow
these
safety
precautions
could
result
in
coil
bursting,
which
could
result
in
serious
injury
or
death.
To
clean
the
coil
Disconnect
all
electrical
power
to
the
equipment
Use
a
soft
brush
to
remove
loose
debris
from
the
coil
Mix
a
high
‐
quality
coil
cleaning
detergent
with
water
according
to
the
manufacturer's
instructions
Clean
coil
according
to
suggested
instructions
Thoroughly
rinse
both
sides
of
the
coil
and
the
drain
pan
with,
clean
water
Straighten
any
coil
fins
that
have
been
bent
during
the
cleaning
process
Confirm
the
drain
line
is
clear
Replace
all
panels
and
parts
and
restore
electrical
power
to
the
equipment
Summary of Contents for CLASSIC NE-002
Page 3: ...B Table of Content B 2 This page is left blank...
Page 10: ...C General Information OMM C S SL 01 C 7 February 2020 Pic C 4 B...
Page 17: ...D Layout and Components D 6 This page is left blank...
Page 21: ...E Sequence of Operation E 4 This page is left blank...
Page 25: ...F Interface and Communication F 4 This page is left blank...