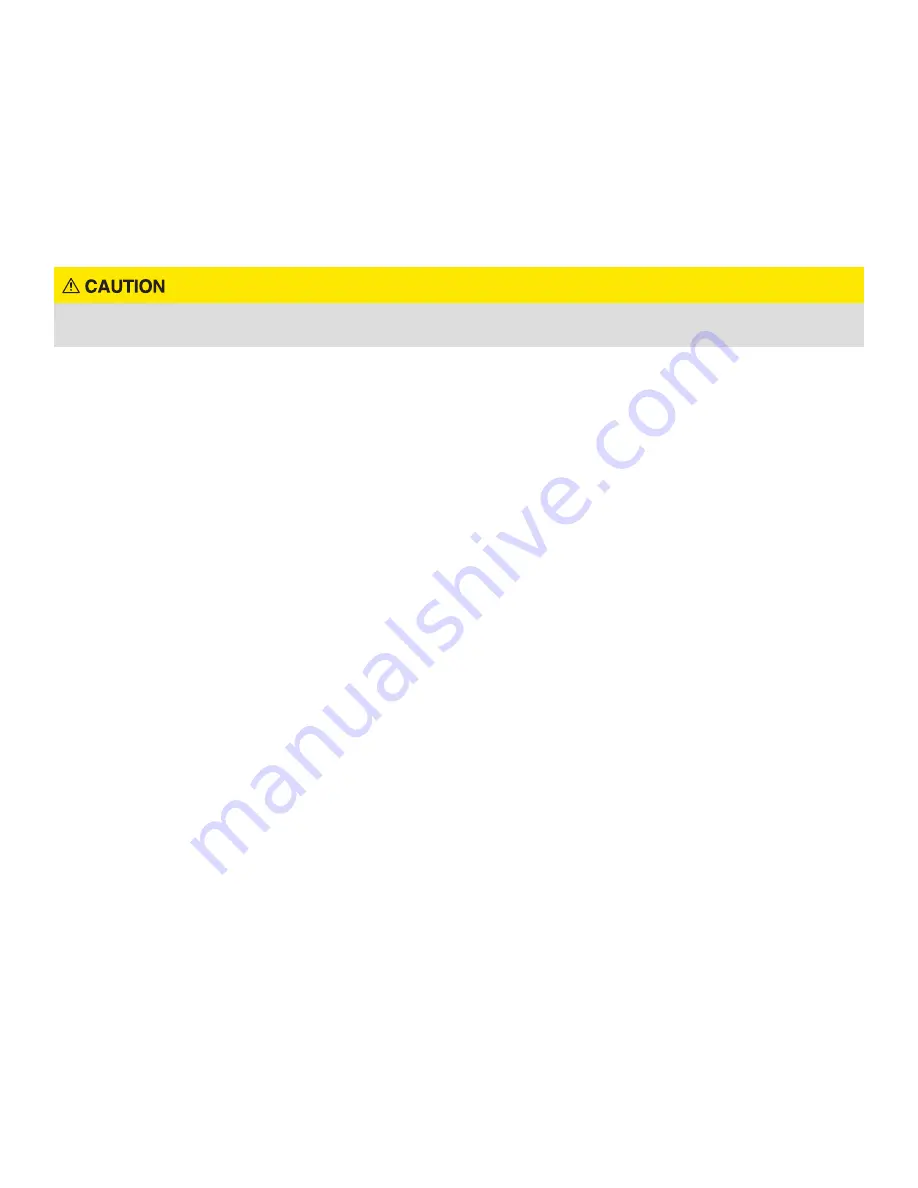
ISOLOK MSA Sampler 9
1.
When checking locations, temporarily attach the L-shaped mounting bracket to the back of the controller, using
the nuts provided .
2.
Be sure the controller is far enough back inside the compartment to allow the door to close without hitting or
rubbing against the controller .
3.
Check to ensure the air line will reach the sampler location without interference with other equipment in the
compartment . The sampler connection line is a 36-inch length of 1/4-inch OD flexible tubing . This air line length
should be kept as short as possible to permit fastest cycle rates .
Mounting
Sampler may require a two-person lift . Please refer to the General Arrangement drawing for weight and dimensional
information .
When the best location for the sampler controller has been determined, mark the position of the mounting bracket
onto the surface . Remove the controller from the mounting bracket . Hold the bracket in position and mark the
location of the four mounting holes onto the compartment wall .
Fastening
Drill four mounting holes to accept the fasteners you select to hold the bracket . Use all four holes and largest fasteners
(screws, bolts, etc .) available to withstand the severe vibration usually encountered in this application .
Tanks with Bulkheads
Walls that seal a wet compartment from a dry area require special handling . The air supply line cannot be routed
around a sealing bulkhead wall without the danger of pinching the tube or blocking the door .
Wall Penetrations
The following procedure is suggested whenever air tube must be routed through a wall between compartments .
Since tank compartment designs vary, this is a general guide intended to be combined with your experience and local
practices .
1.
Locating the hole between compartments: Determine the best place to pass the tube between compartments
after you have decided on a location for both the sampler and sampler controller . Be sure the hole location avoids
interference, pinch-points or wear on flexible line . Choose a hole location that provides the shortest practical
distance between the sampler and controller . This should give maximum slack in the tube for later mounting and
handling of the sampler .
2.
Protecting and sealing tube: Each Sentry ISOLOK sampler includes two bulkhead grommets as standard . If
additional grommets are required, contact Sentry Equipment Corp . Alternately, protective collars can be made on-
site .
3.
Single wall bulkhead: Drill a 3/8-inch (9 .5 mm) diameter hole . Remove burrs and install a grommet in the hole .
Feed the tube through the grommet to its approximate final location .
4.
Double wall bulkhead: Drill two 3/8-inch (9 .5 mm) diameter holes exactly opposite each other to form a passage
through the wall . Remove or push aside any insulating material between the walls that might interfere with the
grommets . Use a pair of grommets, one for each side of wall . Follow the same installation procedure as a single
wall installation, provided above .