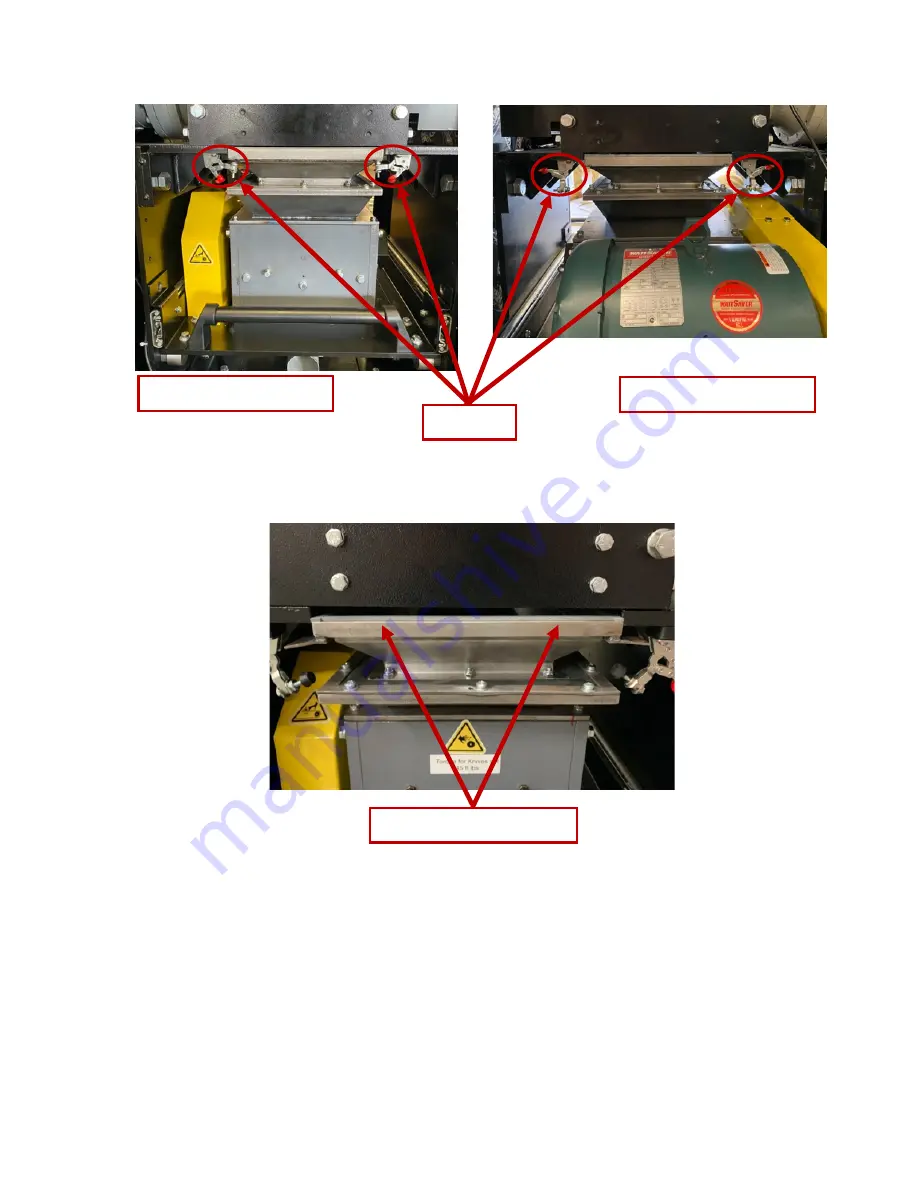
508.366.1488 | www.semshred.com
26
Figure 23. Four latches to unlatch
5.
Pull down the mid-hopper adapter if it doesn’t drop after you release all four latches.
Figure 24. Location of mid hopper adapter
6.
Pull cutting chamber drawer all the way out (Figure 25).
7.
Using a 7/16” socket wrench, remove the four bolts securing the hopper (Figure 26).
Mid hopper adapter
View from front of unit
View from rear of unit
Latches