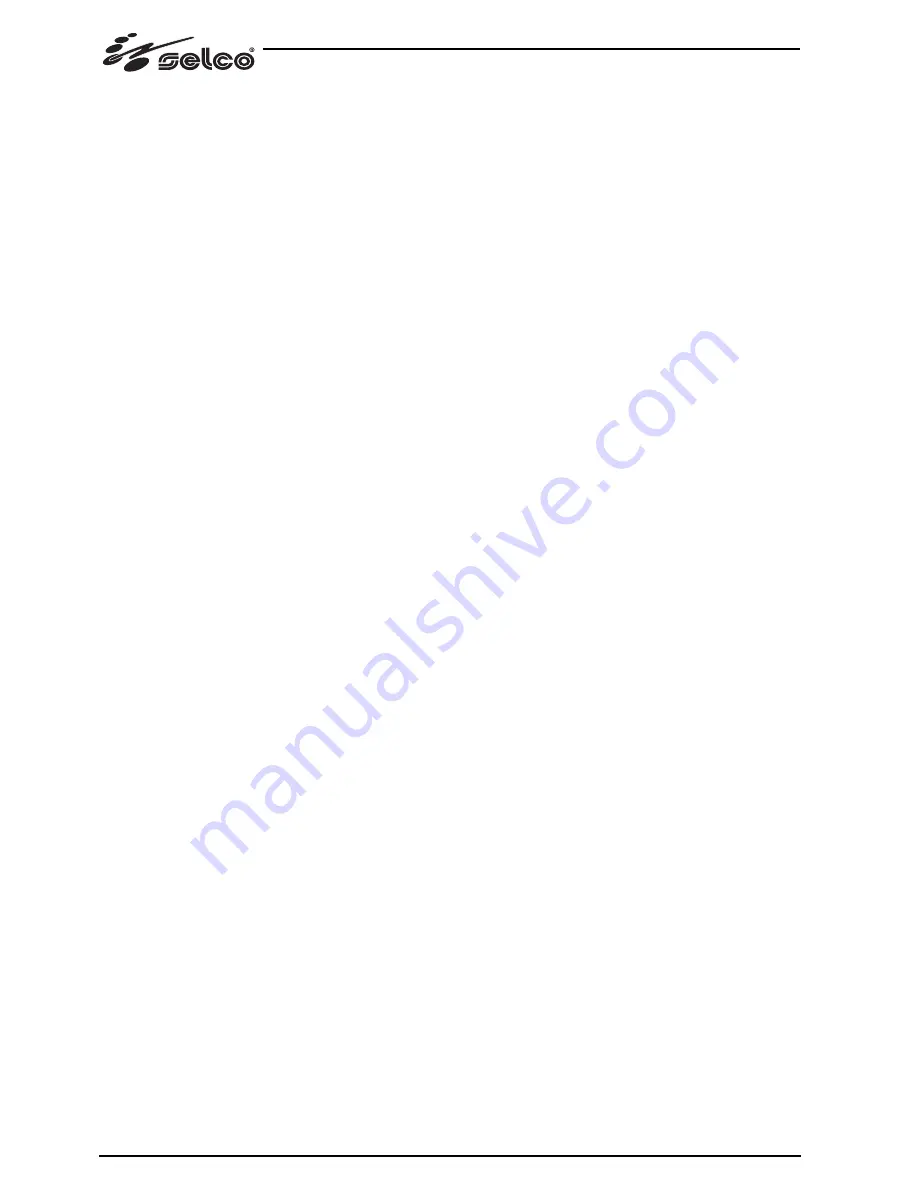
28
Causa
Modalità di esecuzione della saldatura non corretta.
Soluzione Ridurre la distanza tra elettrodo e pezzo.
Avanzare regolarmente durante tutte le fasi della
saldatura.
Inclusioni di tungsteno
Causa
Parametri di saldatura non corretti.
Soluzione Ridurre la corrente di saldatura.
Utilizzare un elettrodo di diametro superiore.
Causa
Elettrodo non corretto.
Soluzione Utilizzare sempre prodotti e materiali di qualità.
Eseguire una corretta affilatura dell'elettrodo.
Causa
Modalità di esecuzione della saldatura non corretta.
Soluzione Evitare contatti tra elettrodo e bagno di saldatura.
Soffiature
Causa
Protezione di gas insufficiente.
Soluzione Regolare il corretto flusso di gas.
Verificare che diffusore e l'ugello gas della torcia
siano in buone condizioni.
Incollature
Causa
Lunghezza d'arco non corretta.
Soluzione Aumentare la distanza tra elettrodo e pezzo.
Aumentare la tensione di saldatura.
Causa
Parametri di saldatura non corretti.
Soluzione Aumentare la corrente di saldatura.
Causa
Modalità di esecuzione della saldatura non corretta.
Soluzione Angolare maggiormente l'inclinazione della torcia.
Causa
Pezzi da saldare di consistenti dimensioni.
Soluzione Aumentare la corrente di saldatura.
Aumentare la tensione di saldatura.
Causa
Dinamica d'arco non corretta.
Soluzione Aumentare il valore induttivo del circuito.
Incisioni marginali
Causa
Parametri di saldatura non corretti.
Soluzione Ridurre la corrente di saldatura.
Utilizzare un elettrodo di diametro inferiore.
Causa
Lunghezza d'arco non corretta.
Soluzione Ridurre la distanza tra elettrodo e pezzo.
Ridurre la tensione di saldatura.
Causa
Modalità di esecuzione della saldatura non corretta.
Soluzione Ridurre la velocità di oscillazione laterale nel riem-
pimento.
Ridurre la velocità di avanzamento in saldatura.
Causa
Protezione di gas insufficiente.
Soluzione Utilizzare gas adatti ai materiali da saldare.
Ossidazioni
Causa
Protezione di gas insufficiente.
Soluzione Regolare il corretto flusso di gas.
Verificare che diffusore e l'ugello gas della torcia
siano in buone condizioni.
Porosità
Causa
Presenza di grasso, vernice, ruggine o sporcizia sui
pezzi da saldare.
Soluzione Eseguire una accurata pulizia dei pezzi prima di
eseguire la saldatura.
Causa
Presenza di grasso, vernice, ruggine o sporcizia sul
materiale d'apporto.
Soluzione Utilizzare sempre prodotti e materiali di qualità.
Mantenere sempre in perfette condizioni il mate-
riale d'apporto.
Causa
Presenza di umidità nel materiale d'apporto.
Soluzione Utilizzare sempre prodotti e materiali di qualità.
Mantenere sempre in perfette condizioni il mate-
riale d'apporto.
Causa
Lunghezza d'arco non corretta.
Soluzione Ridurre la distanza tra elettrodo e pezzo.
Ridurre la tensione di saldatura.
Causa
Presenza di umidità nel gas di saldatura.
Soluzione Utilizzare sempre prodotti e materiali di qualità.
Provvedere al mantenimento in perfette condizioni
dell'impianto di alimentazione del gas.
Causa
Protezione di gas insufficiente.
Soluzione Regolare il corretto flusso di gas.
Verificare che diffusore e l'ugello gas della torcia
siano in buone condizioni.
Causa
Solidificazione del bagno di saldatura troppo rapida.
Soluzione Ridurre la velocità di avanzamento in saldatura.
Eseguire un preriscaldo dei pezzi da saldare.
Aumentare la corrente di saldatura.
Cricche a caldo
Causa
Parametri di saldatura non corretti.
Soluzione Ridurre la corrente di saldatura.
Utilizzare un elettrodo di diametro inferiore.
Causa
Presenza di grasso, vernice, ruggine o sporcizia sui
pezzi da saldare.
Soluzione Eseguire una accurata pulizia dei pezzi prima di
eseguire la saldatura.
Causa
Presenza di grasso, vernice, ruggine o sporcizia sul
materiale d'apporto.
Soluzione Utilizzare sempre prodotti e materiali di qualità.
Mantenere sempre in perfette condizioni il mate-
riale d'apporto.
Causa
Modalità di esecuzione della saldatura non corretta.
Soluzione Eseguire le corrette sequenze operative per il tipo
di giunto da saldare.
Causa
Pezzi da saldare con caratteristiche dissimili.
Soluzione Eseguire una imburratura prima di realizzare la
saldatura.
Cricche a freddo
Causa
Presenza di umidità nel materiale d'apporto.
Soluzione Utilizzare sempre prodotti e materiali di qualità.
Mantenere sempre in perfette condizioni il mate-
riale d'apporto.
Summary of Contents for Genesis 3000 MTE
Page 34: ...34...
Page 128: ...128...
Page 160: ...160...
Page 192: ...192...
Page 224: ...224...
Page 254: ...254...
Page 348: ...348 1 3 1 4 11 35 1 5...
Page 350: ...1 8 IP S IP23S 12 5 mm 60 2 2 1 GT 500 2 2 10 2 3 400V 230V 15 15 2 1 5 350...
Page 361: ...361 1 2 3 2 1 3 1 9 9 encoder 4 encoder 1 2 1 2...
Page 369: ...369 5 6 Reset...
Page 370: ...370 encoder...
Page 371: ...371...
Page 372: ...372 7 7 1 MMA Hot Start Arc Force antisticking 7 2 TIG TIG Tungsten lnert Gas 3370 C H F lift...
Page 374: ...374 7 3 MIG MAG MIG SHORT ARC 1a SHORT a SPRAY ARC b SPRAY ARC 1b 2 3 2 3 1a 1b...
Page 380: ...380 GENESIS 3000 PMC GENESIS 3000 SMC...
Page 388: ...388...