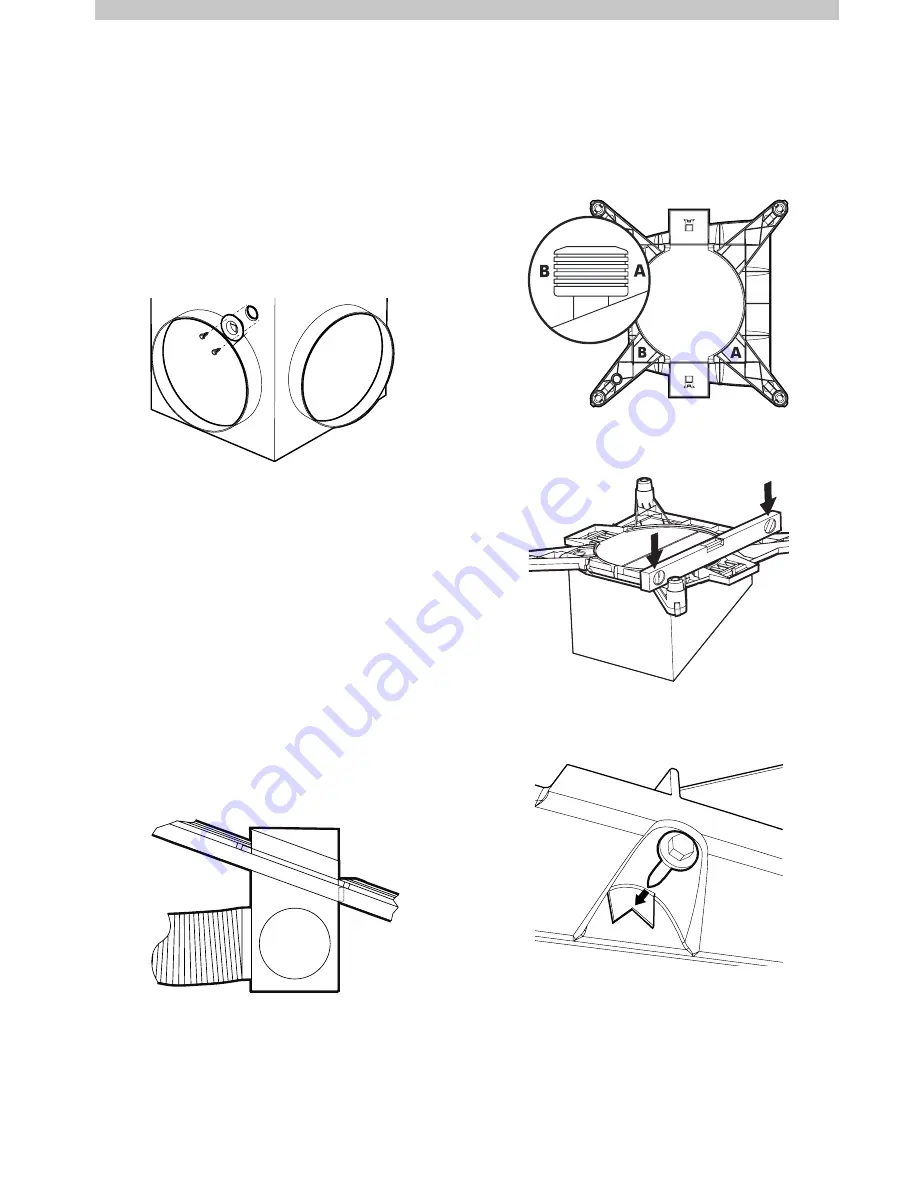
LCQ / LCS / LCQI / BMQ / CPQ / TBQ / TBS / TBQI / TBSI EVAPORATIVE COOLER INSTALLATION MANUAL
|
5
ILL969-B
Fit the transition onto the dropper as shown. Ensure that it is
orientated correctly, as shown by the engraved detail on the
transition.
ILL967-B
ILL1683-A
MOUNTING THE DROPPER
PREPARING THE DROPPER
The 550 x 550mm (21.7 x 21.7”) dropper duct must have a raw
edge or safe edge at the top. Do not fold in a flange as this may
interfere with the transition and/or AutoWinterseal.
For Australia Only
Cut a 50mm diameter cable exit hole in the dropper then
fit and screw the cable grommet into position. Locate the
hole so the cables will not interfere with the operation of the
AutoWinterseal.
Install the dropper and securely fix it to the roof structure on 3
sides. This may require the addition of extra structural timber.
Important!
The dropper must never sit directly on ceiling joists
or beams, as this may cause noise or vibration issues, and
possible ceiling damage.
Ensure the top of the dropper is level and square in all directions
(use a spirit level). This helps with levelling the cooler.
The installer must ensure the dropper is suitable, and is secured
adequately for wind conditions at the site. Additional restraints
may be required if the cooler is more than 200mm (8”) higher
than the roof timbers, or design wind velocity at the site
exceeds 43m/s (141fps).
In exposed or very high wind areas use 16 screws, minimum
shank diameter 5.2mm (7/32”) to secure the dropper. In areas
subject to hurricanes/windstorms or where the cooler is located
more than 8m (26’) above the ground seek advice from a
structural engineer.
SECURING THE DROPPER & TRANSITION
The dropper may now be flashed to the roof. Make sure there is
no chance of water entering the roof space.
Check the level of the transition on the dropper, with a spirit
level placed across the flats in both directions.
ILL1049-B
Check the level of the transition on the dropper, with a spirit
level placed across the flats in both directions.
Once level, begin securing the transition to the dropper using
the screws provided. There are eight ‘V’ notch locations for
screws.
Only use the screws provided. These must be used in the correct
positions to prevent interference with the AutoWinterseal. All eight
(8) screws must be used. Check the level periodically before
driving in all the screws.
Ensure the duct insulation is firmly held against the duct
connector flange on the dropper.
ILL1646-A