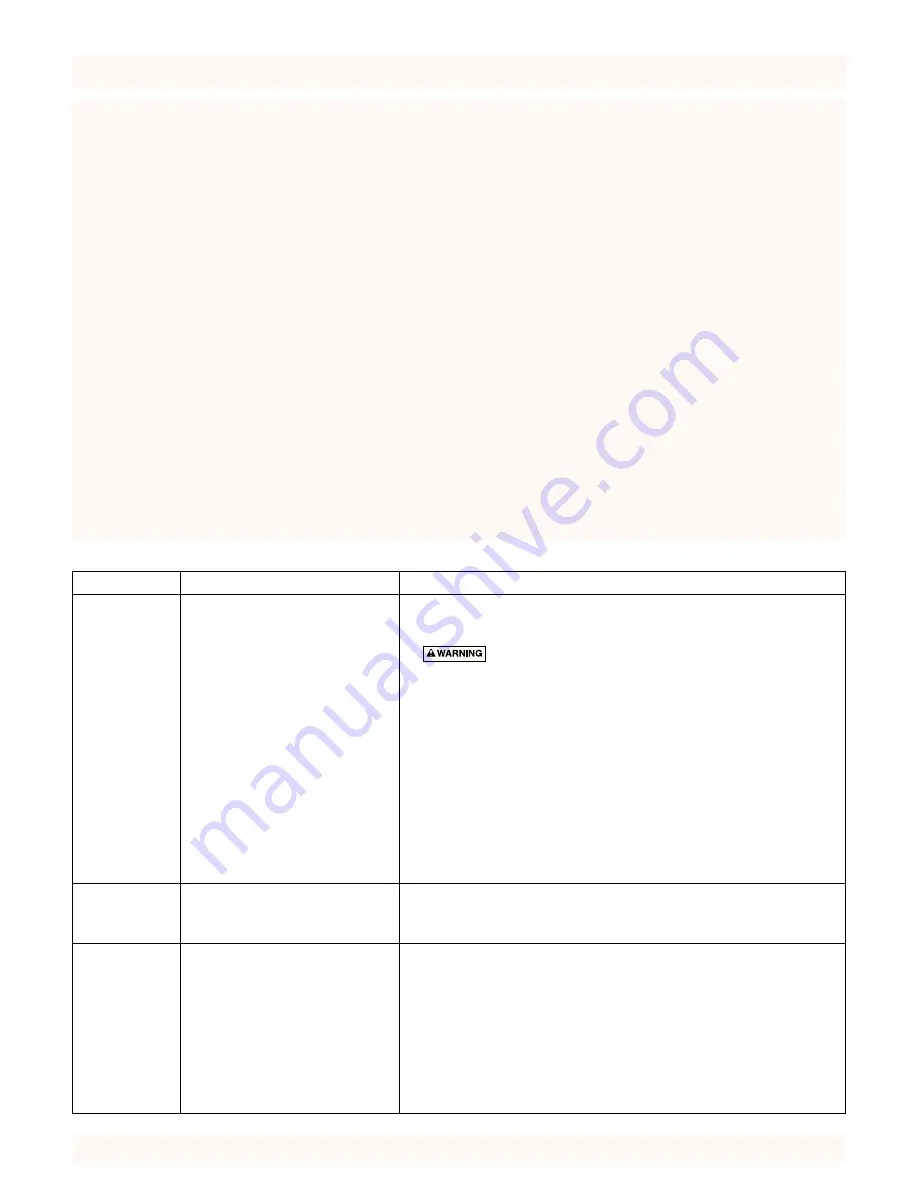
INSTALLATION
set in this position, allow water to be pumped on the
ground until it is completely clear of solids such as silt and
sand. This can be checked by catching some water in a
glass container and waiting a period of time to let the
solids in the water settle to the bottom of the container.
When the water completely clears, open the valve several
turns to increase the flow rate and repeat the checking
procedure for solids.
Continue the flow-checking procedure until the valve is
completely open and water is free of solids.
4. Turn off electric power and remove temporary piping and
wiring. Proceed with final installation.
Pitless Adapter
Follow instructions included with your pitless adapter for in-
stallation.
Well Seal
Tighten the 4 bolts on the well seal, thus compressing the
rubber sealing member and sealing the well casing, the drop
pipe and the cable conduit. A conduit fitting should be used
in order to seal the cable at the top of the well seal. Install
an air vent in the third opening in the sanitary well seal as
shown in the diagrams, Figure 1, Page 4.
Complete Installation and Check Operation
At this point the necessary piping to complete this installa-
tion to the tank should be added.
For suggested methods of piping to the tank, refer to Figures
2 and 3, Page 4, for the pressure tank system being installed.
Where the tank and controls are installed in a basement or
at another location away from the well, it is necessary that
the pipe leading from the tank back to the well be buried
below the frost line to prevent freezing.
When all connections have been made, the pump is ready
for operation.
Turn on switch. The pressure switch will stop the pump at
60 PSI, and will allow it to start again when enough water
has been drawn to reduce the water system pressure to 40
PSI. This can be checked by opening a faucet and drawing
water until the pump starts again.
NOTICE:
Be sure there is no excessive sand in the water.
Sears, Roebuck and Co. and the manufacturer cannot be re-
sponsible for damage to the pump and motor caused by ex-
cessive sand. (See
Well Development.
)
NOTICE
: If there is a chance the pump can over-pump well,
install a Pump Guard (Stock No. 2720) to protect against dry
running.
11
Trouble
Causes
Remedies
Little or no water
A. Water level in a low producing well
A. Lower pump further into well, but make sure it is at least five feet above well bottom.
delivered.
drops too low while pump is operating,
Install a valve in discharge pipe between pump and pressure tank.
causing air lock, loss of prime and
Use valve to restrict flow until discharge rate does not exceed well recovery rate.
possibly seriously damaging pump.
To prevent possibility of dangerous high pressure, install a
relief valve in discharge pipe between pump and flow restriction valve.
Relief valve must be capable of passing full pump flow at 75 PSI.
B. Intake screen partially plugged.
B. Lime or other matter in water may build up on screen.
Pull pump and clean screen.
C. Check valve(s) may be stuck.
C. Make sure that built-in check valve in pump and any check valves in
discharge line are free to open properly.
D. Voltage too low; motor will run
D. Have a competent electrician verify voltage at electrical disconnect box (2-Wire)
slowly, causing low discharge pressure
or control center (3-Wire) while pump is operating. If voltage is low, power company
(head) and high operating current draw.
may need to raise it or installation may require larger wire. Discuss with power
company or licensed electrician.
E.
Standard tanks only: check valve
E. Examine check valve; if stuck free it. If installed backwards (arrow on valve
above bleeder orifice assembly may
body will show direction of flow), reverse it. If valve is defective, replace it with a
be stuck or installed backwards.
new one.
F. Impellers or diffusers worn due to
F. Pull pump and return to Sears for service. Before reinstalling
sand or abrasives in water or run-
pump, sandy or gaseous conditions in well must be corrected.
ning pump while it is air/gas-locked.
Air or milky water
A. Air volume control not functioning,
A. Replace air volume control if necessary.
discharges
causing air to build up in tank.
from faucets.
B. Well water may be gaseous.
B. If your well is naturally gaseous and your system has a standard tank, remove the bleeder
orifices and plug the tees. If condition is serious, check with competent well professionals.
Pump starts too
A. Leak in pressure tank or plumbing.
A. Check all connections with soapsuds for air leaks. Fix any leaks you find. Check
frequently.
plumbing for water leaks. Fix any leaks you find.
B. Pressure switch defective or out of
B. If necessary, replace switch.
adjustment.
C. Check valve leaking.
C. Inspect valves and replace if necessary.
D. Tank waterlogged.
D. Captive Air
®
Tanks: Check tank for leaks; correct if possible. Recharge tanks to 20 PSI
with a 20-40 PSI switch, 30 PSI for a 30-50 PSI switch, 40 PSI for a 40-60 PSI switch, etc.
Standard Tanks: Check tank for leaks; correct if possible. Check bleeder orfices and clean
bleeders; replace if necessary.
E. Drop pipe leaking.
E. Raise one length of pipe at a time until leak is found. When water stands in pipe, there is no
leak below that point.
F. Pressure switch is too far from tank.
F. Move pressure switch to within one foot of tank.
HELPFUL HINTS – TROUBLES, CAUSES & REMEDIES